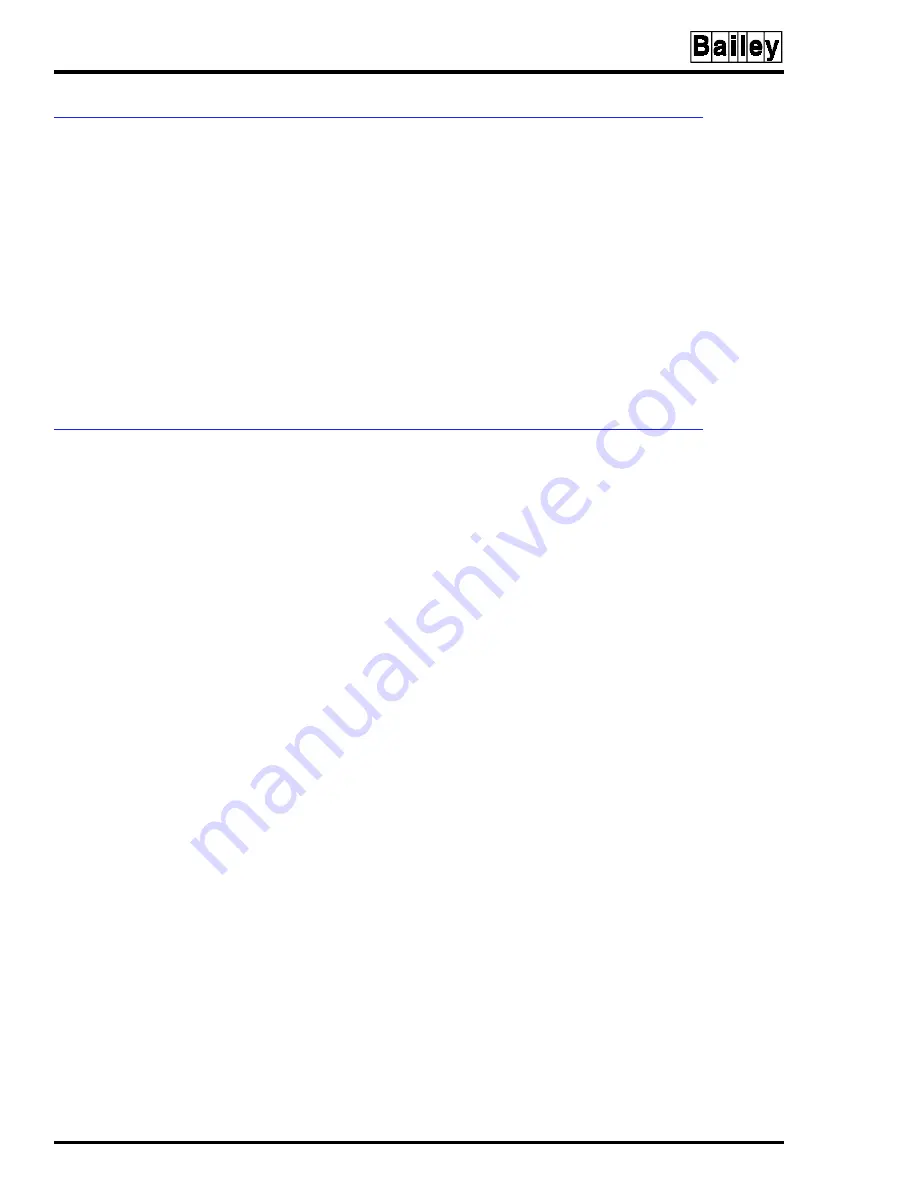
THEORY OF OPERATION
CONTROL LOOP OPERATION
2 - 2
I-E96-314A
®
Frequency Counter Slave
The FCS detects turbine rotation by counting pulses it receives
from a magnetic pickup on the turbine shaft. Additionally, it
keeps a 24 bit timer value corresponding to the period of the
pulse count. It stores these values in a buffer and sets a data
available status bit to notify the MFP that it has current data.
FCS operation is automatic. It continuously updates the count
and holds it for the MFP.
For the MFP to work with the FCS, it requires Function Code
145 in its configuration. Function Code 145 defines the slave
address, high/low speed alarms and high/low rate of change
alarms. The block output is frequency in hertz. The frequency
counter slave continuously checks itself and notifies the MFP if
a failure occurs.
Hydraulic Servo Slave
The HSS provides control of servo valves in a turbine speed
control system. The MFP sends data to the hydraulic servo
slave which directs the control of a hydraulic actuator (via the
servo valve). By sending a position demand to the HSS, the
MFP initiates a change in turbine speed. The position demand
travels over the slave expander bus to the HSS. An on-board
microcontroller reads the demand and loads it into a D/A con-
verter. The resulting analog value drives the servo valve. The
servo valve loads hydraulic fluid to one side of a double acting
hydraulic actuator. The hydraulic actuator opens or closes a
fuel throttle valve to change the turbine speed.
For the MFP to work with the HSS it requires Function Code
150 in its configuration. Function Code 150 defines the slave
address, mode of operation (calibration or normal), calibration
cycle time and stores calibration data. The twelve output
blocks include actuator position, LVDT null position, and sta-
tus outputs for the module and process equipment.
A linear variable differential transformer measures actuator
position. The HSS supplies a 1000 Hz excitation voltage on the
primary side of the LVDT. The secondary of the LVDT develops
a differential voltage proportional to the position of the hydrau-
lic actuator. The HSS converts the differential voltage to digital
data and sends it to the MFP. Using the data the HSS stores
(during valve calibration) in its configuration specifications
(S8-S9), it translates the LVDT secondary differential voltage
into actuator position feedback. The HSS is self checking and
notifies the MFP if a failure occurs.
The operator can initiate manual control of the turbine throttle
valve if a HSS communication failure occurs. The HSS provides
inputs that the user hard wires to a +24 VDC source. The oper-
ator directs the HSS to raise or lower the actuator through