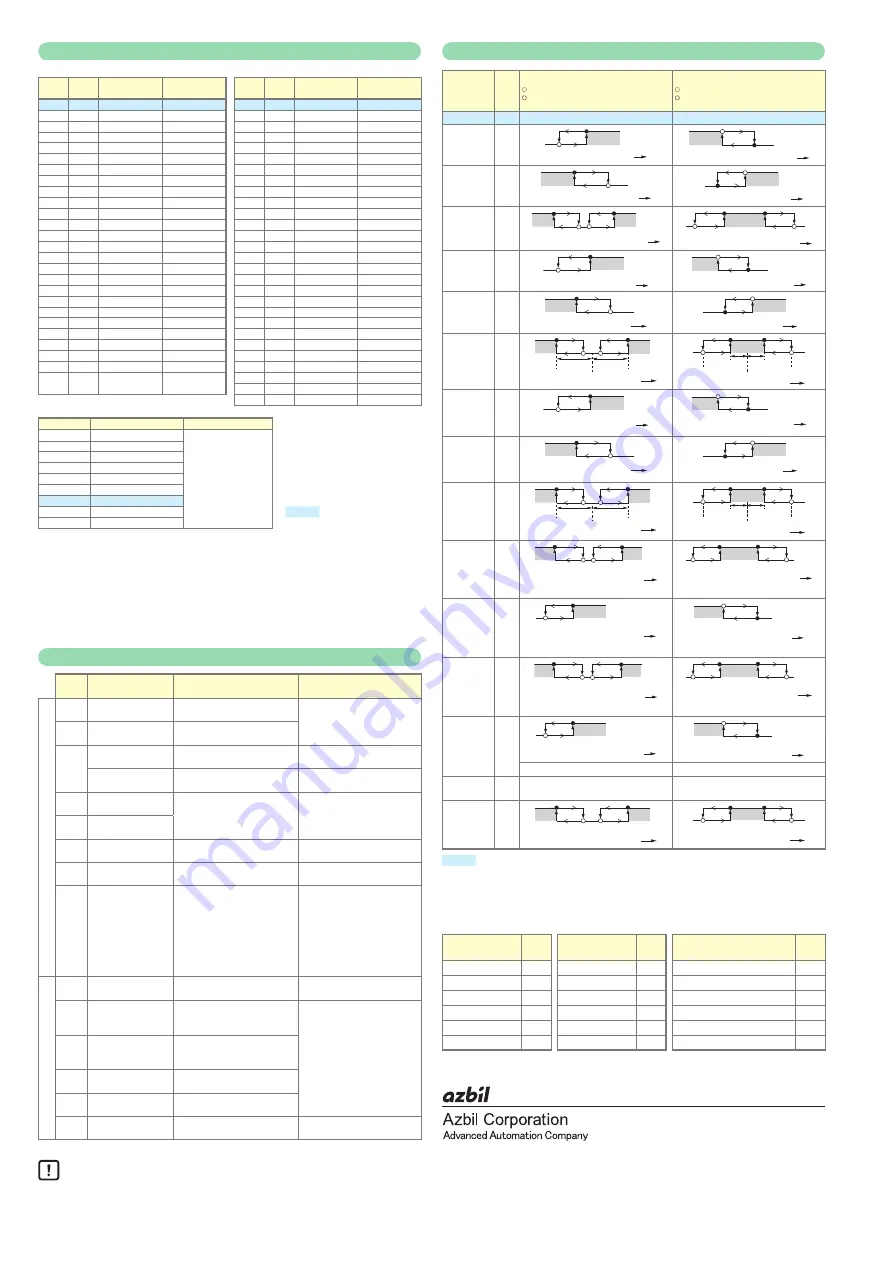
8
1-12-2 Kawana, Fujisawa
Kanagawa 251-8522 Japan
URL
: https://www.azbil.com
(11)
Specifications are subject to change without notice.
PV input range table
[Thermocouple]
[RTD]
C0
1
set value
Sensor
type
Range
(°C)
Range
(°F)
C0
1
set value
Sensor
type
Range
(°C)
Range
(°F)
1
K
-200 to +1200
-300 to +2200
41
Pt100
-200 to +500
-300 to +900
2
K
0 to 1200
0 to 2200
42
JPt100 -200 to +500
-300 to +900
3
K
0.0 to 800.0
0 to 1500
43
Pt100
-200 to +200
-300 to +400
4
K
0.0 to 600.0
0 to 1100
44
JPt100 -200 to +200
-300 to +400
5
K
0.0 to 400.0
0 to 700
45
Pt100
-100 to +300
-150 to +500
6
K
-200.0 to +400.0 -300 to +700
46
JPt100 -100 to +300
-150 to +500
7
K
-200.0 to +200.0 -300 to +400
47
Pt100
-100 to +200
-150 to +400
8
J
0 to 1200
0 to 2200
48
JPt100 -100 to +200
-150 to +400
9
J
0.0 to 800.0
0 to 1500
49
Pt100
-100 to +150
-150 to +300
10
J
0.0 to 600.0
0 to 1100
50
JPt100 -100 to +150
-150 to +300
11
J
-200.0 to +400.0 -300 to +700
51
Pt100 -50.0 to +200.0
-50 to +400
12
E
0.0 to 800.0
0 to 1500
52
JPt100 -50.0 to +200.0
-50 to +400
13
E
0.0 to 600.0
0 to 1100
53
Pt100 -50.0 to +100.0
-50 to +200
14
T
-200.0 to +400.0 -300 to +700
54
JPt100 -50.0 to +100.0
-50 to +200
15
R
0 to 1600
0 to 3000
55
Pt100 -50.0 to +100.0
-50 to +200
16
S
0 to 1600
0 to 3000
56
JPt100 -60.0 to +40.0
-60 to +100
17
B
0 to 1800
0 to 3300
57
Pt100 -60.0 to +40.0
-60 to +100
18
N
0 to 1300
0 to 2300
58
JPt100 -40.0 to +60.0
-40 to +140
19
PL II
0 to 1300
0 to 2300
59
Pt100 -40.0 to +60.0
-40 to +140
20
WRe5-26
0 to 1400
0 to 2400
60
JPt100 -10.00 to +60.00
-10 to +140
21
WRe5-26
0 to 2300
0 to 4200
61
Pt100 -10.00 to +60.00
-10 to +140
22
Ni-Ni·Mo
0 to 1300
0 to 2300
62
JPt100
0.0 to 100.0
0 to 200
23
PR40-20
0 to 1900
0 to 3400
63
Pt100
0.0 to 100.0
0 to 200
24
DIN U -200.0 to +400.0 -300 to +700
64
JPt100
0.0 to 200.0
0 to 400
25
DIN L -100.0 to +800.0 -150 to +1500
65
Pt100
0.0 to 300.0
0 to 500
26
Gold iron
chromel
0.0K to 360.0 K
0 to 360 K
66
JPt100
0.0 to 300.0
0 to 500
67
Pt100
0 to 500
0 to 900
68
JPt100
0 to 500
0 to 900
[DC voltage/DC current]
C0
1
set value
Input type
Range
81
0 to 10 mV
The scaling and deci-
mal point position can
be changed variably
in a range of –1999 to
+9999
82
-10 to +10 mV
83
0 to 100 mV
84
0 to 1 V
86
1 to 5 V
87
0 to 5 V
88
0 to 10 V
89
0 to 20 mA
Initial value
90
4 to 20 mA
*1
• The accuracy of the B thermocouple is ±4.0 %FS for a range of 260 °C or less, ±0.4 %FS for 260
to 800 °C and ±0.2 %FS for 800 to 1800 °C. The PV values under 20 °C are not shown.
• The accuracy of the No.15 (sensor type R) or No.16 (sensor type S) is ±0.2 %FS for a range of 100
°C or less, and ±0.15 %FS for 100 to 1600 °C.
• The accuracy of the No.23 (sensor type PR40-20) is ±2.5 %FS for 0 to 300 °C, and ±1.5 %FS for
300 to 800 °C, ±0.5 %FS for 800 to 1900 °C.
• The accuracy of the No.26 (sensor type gold iron chromel) is ±1.5 K.
• The accuracy of the No. 55 to 62 and 81 are ±0.15 %FS ±1digit for each ranges.
*2 The indicated low limit for a B thermocouple is 20°C. However, if ROM version 1 of the instrument
information bank (
I
d02
) is prior to 2.04, the value is -180°C.
List of alarm codes
Alarm
code
Failure name
Cause
Corrective action
Input failur
e
AL0
1
PV input failure
(Over-range)
Sensor burnout, incorrect wiring,
incorrect PV input type setting
Check the wiring.
Set the PV input type
again.
AL02
PV input failure
(Under-range)
Sensor burnout, incorrect wiring,
incorrect PV input type setting
AL03
CJ failure
Terminal temperature is
faulty (thermocouple).
Check the ambient
temperature.
PV input failure
(RTD)
Sensor burnout, incorrect
wiring
Check the wiring.
AL05
RSP input failure *
1
(over range)
Sensor line break, incorrect
wiring, incorrect RSP range
setting
Checking wiring or reset
RSP range code.
AL06
RSP input failure *
1
(under range)
AL07
MFB input failure Motor line break, incorrect
wiring
Checking wiring or confirm
the MFB input.
AL
10
Motor adjust-
ment failure
Motor line break, incorrect wir-
ing, motor power supply failure.
Checking wiring, confirm the
motor power supply, reset.
AL
1
1
CT input failure
(Over-range)
(CT input 1 or 2,
or both)
A current exceeding the
upper limit of the display
range was measured. The
number of CT turns or the
number of CT power wire
loops is incorrectly set, or
wiring is incorrect.
•
Use a CT with the cor-
rect number of turns for
the display range.
•
Reset the number of CT
turns.
•
Reset the number of CT
power wire loops.
•
Check the wiring.
Unit failur
e
AL70
A/D conversion
failure
A/D converter is faulty.
Replace the unit.
AL95
Parameter failure Power is shut-down while
the data is being set, or
data is corrupted by noise.
•
Restart the unit.
•
Set the data again (set
data for
AL95
/
97
and
adjustment data for
AL96
/
98
.
•
Replace the unit.
AL96
Adjustment data
failure
Power is shut-down while
the data is being set, or
data is corrupted by noise.
AL97
Parameter failure
(RAM area)
Data is corrupted by noise.
AL98
Adjustment data
failure (RAM area)
Data is corrupted by noise.
AL99
ROM failure
ROM (memory) is faulty.
•
Reset the unit.
•
Replace the unit.
*1 Displays in RSP mode
Handling Precautions
•
If ROM version 1 (
i
d02
) of the instrument information bank
is 2.04 or earlier, CT input failure (
AL
1
1
) is not displayed.
Event type
Operation
type
Set
value
Direct action
: shows that the ON/OFF is changed at this value.
: shows that the ON/OFF is changed at a point
that "1U" is added to this value.
Reverse action
: shows that the ON/OFF is changed at this value.
: shows that the ON/OFF is changed at a point
that "1U" is added to this value.
No event
0
Always OFF
Always OFF
PV high
limit
1
ON
HYS
Main setting
PV
ON
HYS
Main setting
PV
PV low limit
2
Main setting
PV
ON
HYS
Main setting
PV
ON
HYS
PV high/low
limit
3
Main setting *1 Sub-setting *1
PV
ON HYS
ON
HYS
Main setting *1 Sub-setting *1
PV
ON
HYS
HYS
Deviation
high limit
4
ON
HYS
SP + Main setting
PV
ON
HYS
SP + Main setting
PV
Deviation
low limit
5
SP + Main setting
PV
ON
HYS
SP + Main setting
PV
ON
HYS
Deviation
high/low
limit
6
Main setting Sub-setting
SP
PV
ON
HYS
ON
HYS
ON
HYS
HYS
Main setting Sub-setting
SP
PV
Deviation
high limit
(Final SP
reference)
7
ON
HYS
SP + Main setting
PV
ON
HYS
SP + Main setting
PV
Deviation
low limit
(Final SP
reference)
8
SP + Main setting
PV
ON
HYS
SP + Main setting
PV
ON
HYS
Deviation
high/
low limit
(Final SP
reference)
9
Main setting Sub-setting
SP
PV
ON
HYS
ON
HYS
ON
HYS
HYS
Main setting Sub-setting
SP
PV
Heater 1
burnout/
Over-current
16
CT1 at output ON
Main setting *1
Sub-setting *1
ON HYS
ON
HYS
ON
HYS
HYS
Main setting *1
Sub-setting *1
CT1 at output ON
OFF before measuring the CT1 current value OFF before measuring CT1 current value
Heater 1
short-circuit
17
ON
HYS
Main setting
CT1 at output OFF
ON
HYS
Main setting
CT1 at output OFF
OFF before measuring CT1 current value OFF before measuring CT1 current value
Heater 2
burnout/
Over-current
18
CT2 at output ON
Main setitng *1 Sub-setting *1
ON HYS
ON
HYS
ON
HYS
HYS
Main setting *1
Sub-setting *1
CT2 at output ON
OFF before measuring CT2 current value OFF before measuirng CT2 current value
Heater 2
short-circuit
19
ON
HYS
Main setting
CT2 at output OFF
ON
HYS
Main setting
CT2 at output OFF
OFF before measuring CT2 current value OFF before measuring CT2 current value
Alarm
(status)
23 ON if alarm occurs (alarm code AL01 to 99).
OFF in other cases.
OFF if alarm occurs (alarm code AL01 to 99).
ON in other cases.
High and
low limits of
MFB value*
2
33
Main setting*1 Sub-setting*1
MFB
ON
HYS
ON
HYS
ON
HYS
HYS
Main setting*1
Sub-setting*1
MFB
: initial value
*1 If the main setting is greater than the sub-setting, operations are performed with the
main setting and sub-setting automatically swapped.
*2 Motor feedback
Event types other than the above:
Operation type
Set
value
Operation type
Set
value
Operation type
Set
value
SP high limit
10
Loop diagnosis 1
20
During AT (status)
27
SP low limit
11
Loop diagnosis 2
21
During SP ramp
28
SP high/low limit
12
Loop diagnosis 3
22
Control action (status)
29
MV high limit
13
READY (status)
24
ST setting standby (status)
30
MV low limit
14
MANUAL (status)
25
Estimated position contorol (status)
31
MV high/low limit
15
RSP (status)
26
Timer (status)
32
1st edition: Dec. 2007 (W)
3rd edition: May 2019 (B)
© 2007–2019 Azbil Corporation. All Rights Reserved.