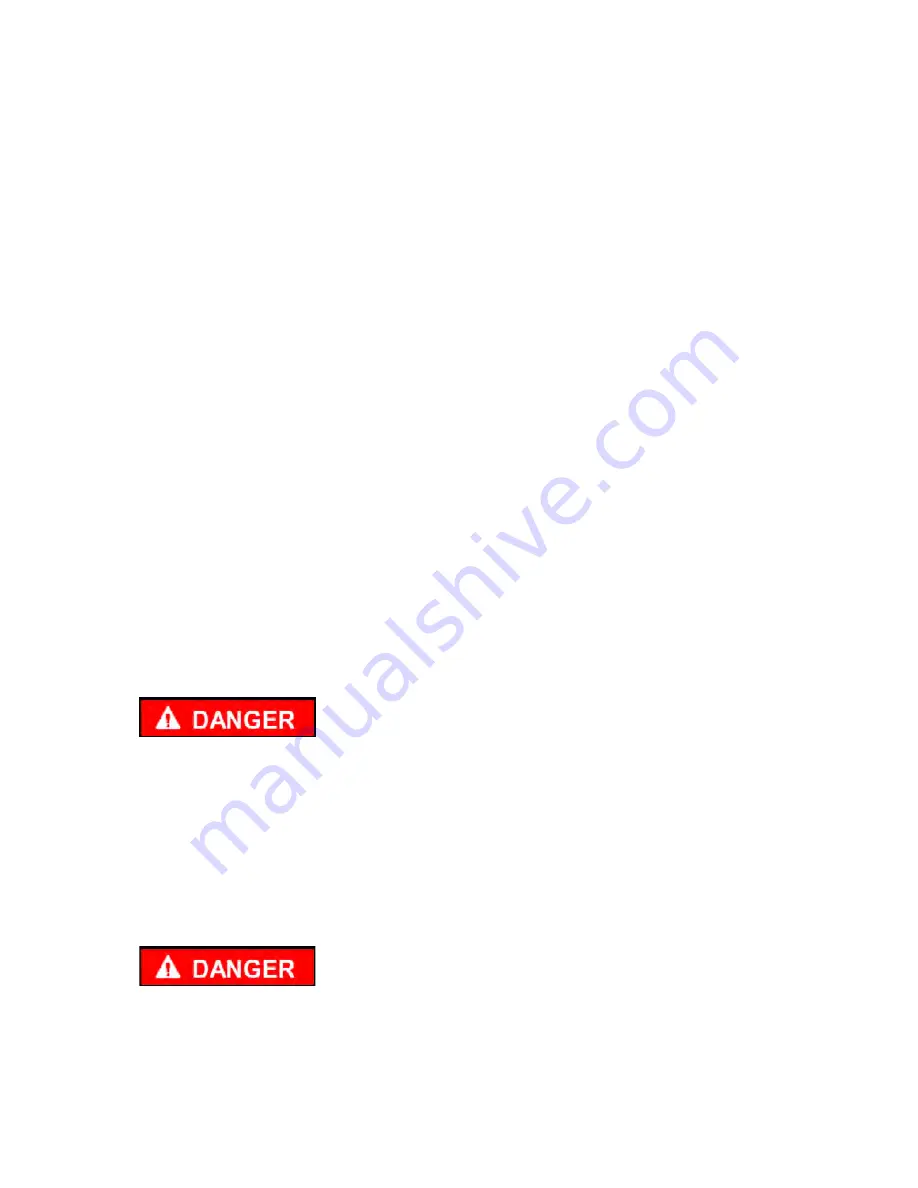
20
© 2013 Axxiom Manufacturing, Inc.
3.8 Abrasive Selection
Abrasive selection is likely the most difficult decision related to the blast operation. Choice of
abrasive is based on factors such as blast application type, desired finish and coating
requirements, characteristics of object to be blasted, cost and ability to recycle, available
equipment, safety, and environmental constraints.
There are many abrasives available that are either natural, manufactured, or processing by-
products. Abrasives are available in varying sizes, shapes, and hardness. These characteristics
determine the resulting effect on the surface to be blasted and limitations of its use. The effects
on the blasted surface are measured by its degree of cleanliness and the surface profile.
Standards and required levels of these measurements are established by organizations such as
Steel Structures Painting Council (SSPC), National Association of Corrosion Engineers
(NACE) and coating manufacturers. See Section 12.5 for contact information of these
organizations. Use these sources to obtain information regarding all aspects of surface
preparation and abrasive selection guidelines.
Schmidt® abrasive blasters are designed for high production open abrasive blasting with a
wide range of abrasives. It is the responsibility of the employer and operators to select the
proper abrasive. It is the responsibility of the employer to make certain that the abrasive
selected is safe to use for abrasive blasting.
Critical:
Always obtain the Material Safety Data Sheet (MSDS) for the abrasive to be used.
The MSDS provides the chemical makeup of the abrasive. Do Not use abrasives containing
toxic materials. Refer to OSHA 29 CFR for acceptable limits of various toxic substances and
additional measures to be taken to protect operating personnel. Always use abrasives containing
less than 1% of crystalline silica. Always use a NIOSH approved respirator when handling,
loading and cleaning up abrasives. Organic substances which are combustible may only be used
in automated blast systems with ventilation that meets OSHA 29 CFR 1910.94.
3.9 Breathing Air Quality
All blast operators must be supplied with and required to use NIOSH approved air-fed
respirators. Breathing air supplied to these respirators must meet Grade D air quality standards
as specified by OSHA 29 CFR 1910.134(i) and the Compressed Gas Association Specifications
ANSI/CGA G-7.1. Consult these specifications when selecting a source of breathing air.
Breathing air must be clean, dry, contaminant-free, and provided at a pressure and volume
specified by NIOSH. Use NIOSH approved air filters on all sources of breathing air. See
Section 3.10.
Breathing air filters do not remove carbon monoxide or any other toxic gases. Use a carbon
monoxide monitor to detect unacceptable levels. Consult OSHA 29 CFR 1910.134(i).
Many sources of breathing air are available such as air cylinders, free-air pumps, oil-less air
compressors, and oil lubricated air compressors. The most commonly used is the same air
compressor that is used for the blast air which most often is oil lubricated. Breathing air
provided by an oil-lubricated air compressor can contain carbon monoxide and therefore
requires the use of a carbon monoxide detector (See Section 3.10). Carbon monoxide can be in
the compressed air produced by an oil-lubricated air compressor when it is operated at
extremely high temperature; therefore, a high temperature alarm is required to alert the
operators when this condition exists.
Oil lubricated air compressors can produce carbon monoxide. Carbon monoxide can cause
asphyxiation and result in death. Use a high-temperature alarm and a carbon monoxide monitor
when an oil lubricated air compressor is used to supply breathing air. Consult OSHA 29 CFR
1910.134(i).
Содержание SCHMIDT
Страница 5: ...5 2013 Axxiom Manufacturing Inc 5 7031 077 6 7034 001 Figure 0 1 b Warning decal summary continued...
Страница 6: ...6 2013 Axxiom Manufacturing Inc...
Страница 17: ...17 2013 Axxiom Manufacturing Inc Figure 2 6 Mini Abrasive Blaster Lifting Diagram...
Страница 42: ...42 2013 Axxiom Manufacturing Inc THIS PAGE INTENTIONALLY BLANK...
Страница 44: ...44 2013 Axxiom Manufacturing Inc 9 1 a Mini Abrasive Blaster w Pneumatic Control System...
Страница 45: ...45 2013 Axxiom Manufacturing Inc 9 1 b Pneumatic Control System Parts List 3 5 20 cu ft...
Страница 46: ...46 2013 Axxiom Manufacturing Inc 9 2 a Thompson Valve...
Страница 47: ...47 2013 Axxiom Manufacturing Inc 9 2 b Thompson Valve II...
Страница 48: ...48 2013 Axxiom Manufacturing Inc 9 3 Automatic Air Valve...
Страница 49: ...49 2013 Axxiom Manufacturing Inc 9 4 a G2 Pneumatic Deadman...
Страница 50: ...50 2013 Axxiom Manufacturing Inc 9 4 b Deadman Valves Pneumatic...
Страница 59: ...59 2013 Axxiom Manufacturing Inc NOTES...