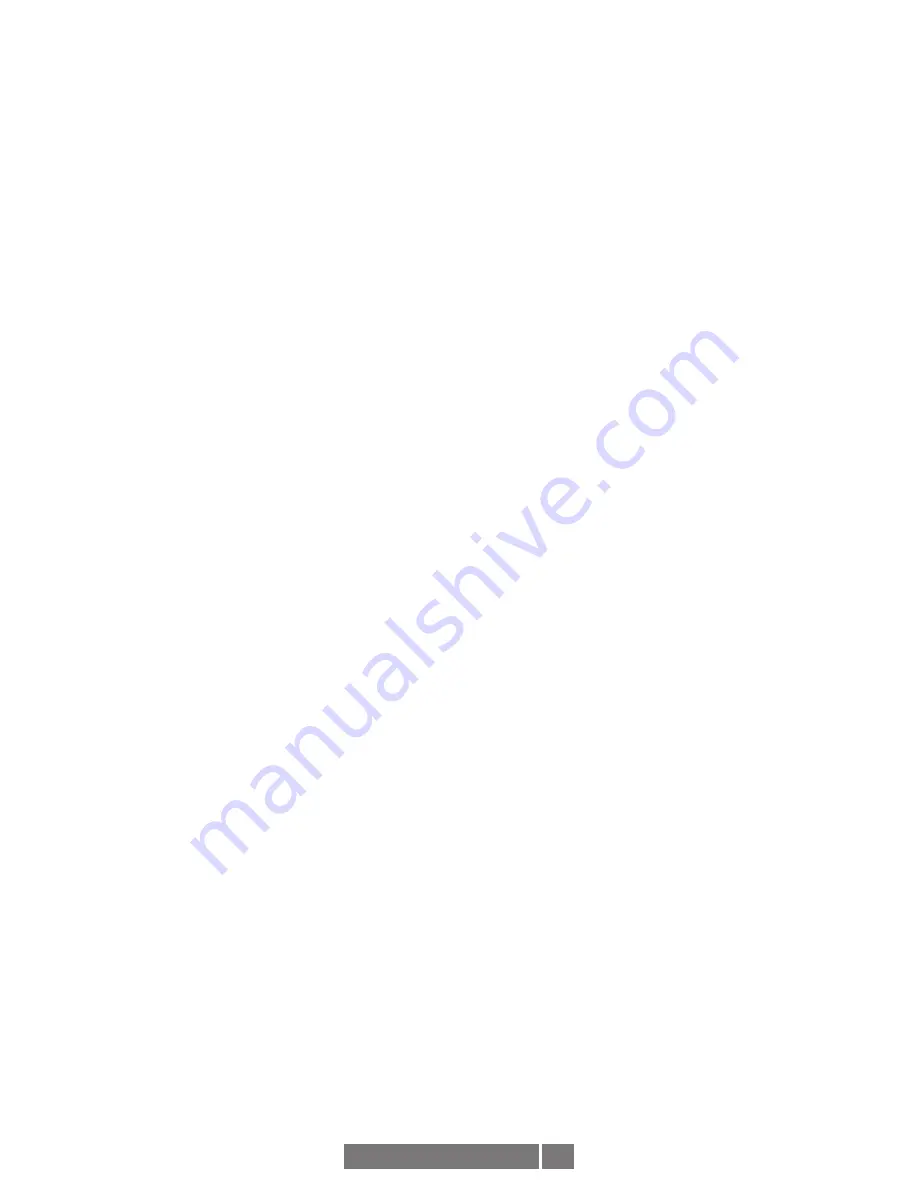
M6C-4, M6C-5
2
A40346
Equipment needed for installation
Supplied:
1. M6C
2. Clamping Collar
3. Anti-rotation Bracket
4. Thread Locker (blue)
5. Screw, Button Hd
6. Screw, Socket cap 1/4-20 x .62
7. Nut, 1/4-20
8. Washer, Flat 1/4 (2)
9. Washer, Lock, 1/4
10. Washer, Shoulder, Insulating
11. Washer, Flat, Insulating (2) 3/8-16 x .50
12. Anti Seize (copper)
Not Supplied:
7/32” Hex wrench (T-handle style)
3/16” Hex wrench (T-handle style)
Clean machine shaft of any dirt and check for any burrs or damage.
The hollow shaft M6C is intended to be installed with a torsionally rigid
flexible anti-rotation arm. See specifications for maximum shaft and
bearing load ratings. The encoder should not be rigidly mounted.
Instructions for Installation of the Standard Flexible Anti-
Rotation Bracket:
Install the anti-rotation bracket to the motor side of the M6C using two
3/8-16 screws and thread locker.
Remove screws from clamping collar, apply anti-seize compound
supplied to the inside of the collar and thread locker supplied to the
threads and reinstall. Place clamping collar loosely on the inboard
end of the shaft. Carefully slide M6C onto the shaft.
DO NOT FORCE.
Encoder should slide on easily. After verifying M6C fit onto shaft,
remove M6C, apply anti seize compound (supplied) to shaft and re-
install M6C (see shaft engagement). Tighten screws on clamping collar
evenly until snug, then firmly tighten.
DO NOT USE A STANDARD
RIGHT ANGLE WRENCH.
Use only a T-handle hex wrench or torque
wrench with hex bit.
Secure free end anti-rotation bracket to frame. Use supplied insulating
hardware if necessary as shown. Adapter kits are available for NEMA
56C and 8 1/2” mounting faces.
Optional torque arm kits are available (supplied with instructions).
Shaft Engagement For End-of-Shaft Mounting Applications:
See table on last page.
For shaft lengths greater than the maximum engagement allowed, end
of shaft mounting may still be employed by locating the encoder away
from the motor using a spacer between the motor and anti-rotation
bracket.
Corrective Action for Excess Housing Movement (Wobble)
The hollow shaft M6C design eliminates the potential for bearing and
coupling failures from misalignment, however, excessive housing
movement (wobble) may cause undesirable vibrations. The higher the
RPM, the more severe the vibration will be from housing movement.
In a typical installation a housing movement of 0.007” TIR or less (as
measured at the outside diameter of the main encoder body) will not
have an adverse effect. If excessive housing movement is detected in
the installation:
1. Check the shaft the M6C is mounted on for excessive shaft
runout. NEMA MG1 calls for 0.002” TIR or less.
2. Verify that the M6C engagement with the motor shaft conforms
to the engagement rules on page 4. In general, maximizing
engagement will minimize housing movement.
3. Verify that the mounting shaft diameters conform to the rules
on page 4. Excessive housing movement occurs when the
clearance between the motor shaft and pulse generator shaft
allows the two center lines to miss match.
4. Loosen the clamping collar and rotate the motor shaft 180°
within the M6C hollow shaft sleeve.
5. Make sure the clamping collar is tightened equally on both
sides.
6. Move the split in the clamping collar over a solid portion of
the M6C shaft.
If excessive housing movement still exists after the above steps, it
may be necessary to physically bias the attitude of the encoder on
the motor shaft while the clamping collar is being tightened. Either
by eye or using dial indicators, note the position around the outside
diameter of the encoder that is most out of position from true while
turning the motor shaft slowly. With the motor shaft no longer turning,
loosen the clamping collar. While applying moderate force by hand
against the outside diameter of the encoder on the side opposite
where the out of true position was observed, retighten the clamping
collar. Several iterations may be necessary if the first attempt under
or over compensates. This method may be used to help compensate
for undersized shafts, shaft runout, bent clamping fingers, and other
problems.
WIRING INSTRUCTIONS
The M6C can be wired for single phase, two-phase, with or without
complements, with or without markers. See wiring diagram.
WARNING
• Do not wire the M6C Encoder while energized. Doing
so may damage the encoder, and/or cause risk of
fire or explosion.
• All cable entry devices used in the increased safety
enclosure shall be certified for the type of increased
safety enclosure “e” rated IP66, suitable for the
conditions of use and correctly installed.
• Unused apertures in the increased safety enclosure
shall be closed with a suitably certified Ex “e”
blanking elements , rated IP66
• For ambient temperatures below -10°C and above
+ 60°C use wiring suitable for both minimum and
maximum ambient temperatures. At maximum
ambient wire & cable glands must be rated 100°C
or
better
Termination Instructions
• Wire conductor size shall meet the following cross-section
requirements:
- Solid wire range: AWG 20 to 12 [0.52 to 4.0mm2]
- Stranded wire range: AWG 20 to 14 [0.52 to 2.5mm2]
• Wire strip length: 0.32 inch to 0.50 inch [8mm to 12.7mm]
• Push terminal screw driver in access hole (near terminal middle)
to open the terminal.
• Insert stripped wire in the terminal until wire bottoms when
using stranded wire make sure all strands are captured in
terminal.
• While keeping wire in position remove screw driver to close the
terminal.
For bidirectional operation of the encoder, proper phasing of the two
output channels is important. Phase A channel leads phase B channel
for clockwise shaft rotation as viewed from the anti-drive or accessory
end of the motor (M6C mounting end).
CORRECTIVE ACTION FOR PHASE REVERSAL
1)
Remove Power.
2) Exchange wires on cable, either at encoder cable end, or at
speed controller end (but not both).
a)
Single Ended 2 Phase Wiring
(see wiring diagram)
Exchange A and B at the use end of the wires.
b)
Differential 2 Phase Wiring
(see wiring diagram)
Exchange
either
A with A– in the phase A pair
OR
B with B–
in the phase B pair but
NOT
both.
3) Apply Power.
4) Verify encoder feedback is correct, using hand rotation of
shaft, or jog mode of the speed controller.
Refer to the system drawing for specific cable requirements where
applicable.