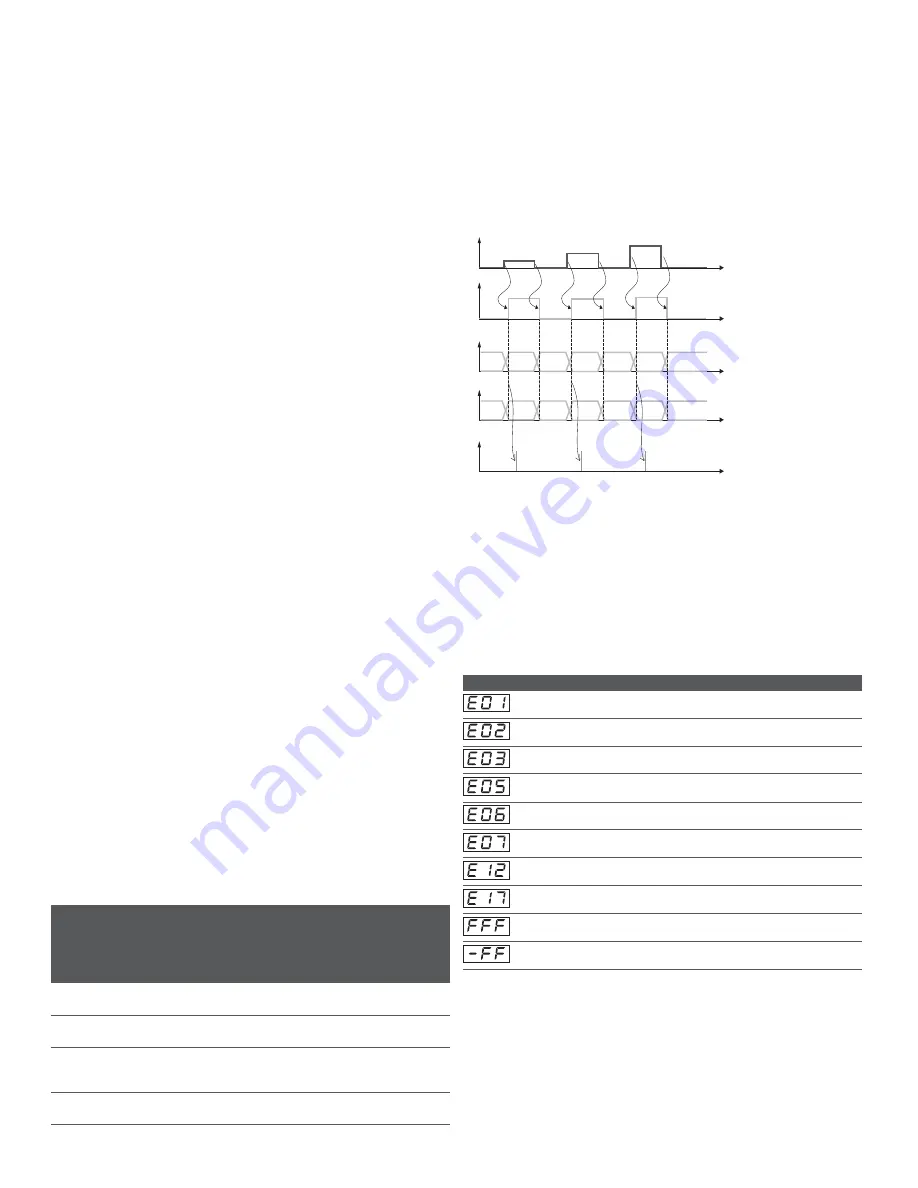
Measuring the dynamic pressure
The system vacuum reached in free suction is measured. The measurement
duration is approx. 1 s. To evaluate a valid dynamic pressure value therefore, after
the start of suction the system should suction freely for at least 1s, i.e. the suction
point may not be occupied by a component yet.
Measurement values below 5 mbar or above the threshold value H1 are not
considered valid dynamic pressure measurements and discarded. The result of the
last valid measurement is sustained.
Measurement values above the threshold value (H2-h2) and at the same time below
the threshold value H1 result in a Condition Monitoring event.
Quality evaluation
To evaluate the entire gripping system the ejector calculates a quality evaluation
based on the measured system leakage.
The higher the leak rate in the system the lower the quality of the gripping system.
Vice versa, a low leak rate results in high quality evaluation.
Calculating performance
Similar to the quality evaluation, the performance calculation is used to evaluate the
system state. Based on the determined dynamic pressure an assessment of the
performance of the gripping system can be made.
Optimally designed gripping systems result in low dynamic pressure and thus high
performance, vice versa badly designed systems exhibit low performance values.
Dynamic pressure results that are higher than the threshold value of (H2-h2) always
result in a performance evaluation of 0%. A performance evaluation of 0% is also
issued for a dynamic pressure value of 0 mbar (which is an indication for an invalid
measurement).
Diagnostic buffer
The Condition Monitoring warnings and general error messages of the device are
stored in a diagnostic buffer.
This storage contains the last 38 events starting with the latest and it can be read
out via an IO-Link parameter. The currently valid counter reading of the suction cycle
counter cc1 is included with each event, to allow subsequent chronological
association of the events with other processes within the system. For the precise
data presentation of the diagnostic buffer see the respective device description file
(IODD).
Recording of these events is also active in the SIO mode and the stored contents are
retained after a power failure. The storage is manually deleted with the IO-Link
system command “Clear diagnostic buffer” or by resetting the device to the factory
settings.
EPC data buffer
To allow long-term monitoring and trend analysis of the most important key figures
of a handling process, the ejector contains a ten-step data buffer. It is available for
storage of the measurement values of the evacuation time t
1
, the leak rate and the
dynamic pressure (vacuum with free suctioning) determined in the current suction
cycle.
The values are always automatically stored in conjunction with the implementation
of the above described Autoset function in Condition Monitoring. The currently valid
counter reading of the suction cycle counter cc1/ct1 is included with each data set,
to allow their subsequent chronological association with other processes within the
system. The contents of the EPC diagnostic buffer can be read out via an IO-Link
parameter whose precise data presentation can be found in the respective device
description file (IODD). The stored contents are retained after a power failure.
EPC values in the process data
For the quick and convenient recording of the events of the functions Condition
Monitoring, Energy Monitoring and Predictive Maintenance, they are also made
available via the process input data of the device. For this purpose, the top 3 bytes of
the process input data are designed as a multi-functional data section, consisting of
an 8-bit value (“EPC value 1”) and a 16-bit value (“EPC value 2”).
The contents of this data currently provided by the ejector can be switched via the
process output data with the 2 bits “EPC Select”. The four possible assignments of
this data are shown in the following table:
PDO
PDI
EPC
select:
EPC value 1 (8-bit)
EPC value 2 (16-bit)
EPC
select
acknowledge
00
Current input pressure
(unit 0.1 bar)
Current vacuum value
(unit 1 mbar)
0
01
Condition Monitoring
Evacuation time t
1
(unit 1 ms)
1
10
Leak rate
(unit 1 mbar/s)
Last measured dynamic
pressure
(unit 1 mbar)
1
11
Supply voltage
(unit 0.1 V)
Air consumption
(unit 0.1 NL)
1
AVENTICS
| ECD-IV/ECD-LV | R412026283–BAL–001–AA | English
19
Depending on the design of the automation system, the switching takes place with a
certain delay. The bit EPC Select Acknowledge is available in the process input data
to allow the efficient reading in of the various value pairs by a control program.
The bit always accepts the values shown in the table. The process described in the
following diagram is recommended for reading out all EPC values:
Always start with EPC Select = 00 and then select the next desired value pair,
e.g. EPC Select = 01. Now wait for the EPC Select Acknowledge bit to switch from
0 to 1. This ensures that the transferred values correspond to the selection and can
be adopted by the control.
Now switch back to EPC Select = 00 and wait for the EPC Select Acknowledge bit to
be reset to 0 by the ejector. Now you can carry out the process for the next value pair,
e.g. EPC Select = 10 in the same way, and so on.
7
Troubleshooting
Error
The ejector's error messages are shown on the display.
EPC select:
[PDOut 0.5...0.4]
EPC select acknowledge
[PDIn 0.3]
EPC value 1
[PDIn 1]
EPC value 2
PDIn 3...2]
Control adopts valid EPC
values
1 = Pressure
2 = CM
3 = Leakage
4 = Voltage
5 = Vacuum
6 = Evacuation time
7 = Dynamic pressure
8 = Air consumption
Symbol
Error code
Electronics error - EEPROM
Electronics error – Internal communication
Zero-point adjustment for the vacuum sensor outside of
±
3% FS
Actuator supply voltage too low
(display alternating with current vacuum value)
Manual operation not possible during the “Blow-off” operating state
Supply voltage too low
Short circuit in output 2/OUT signal output
Supply voltage too high
Vacuum created exceeds the measurement range
Overpressure in the vacuum circuit
00
00
00
11
10
01
1
1
1
1
4
5
6
7
8
5
5
5
3
2
Содержание ECD-IV
Страница 30: ......