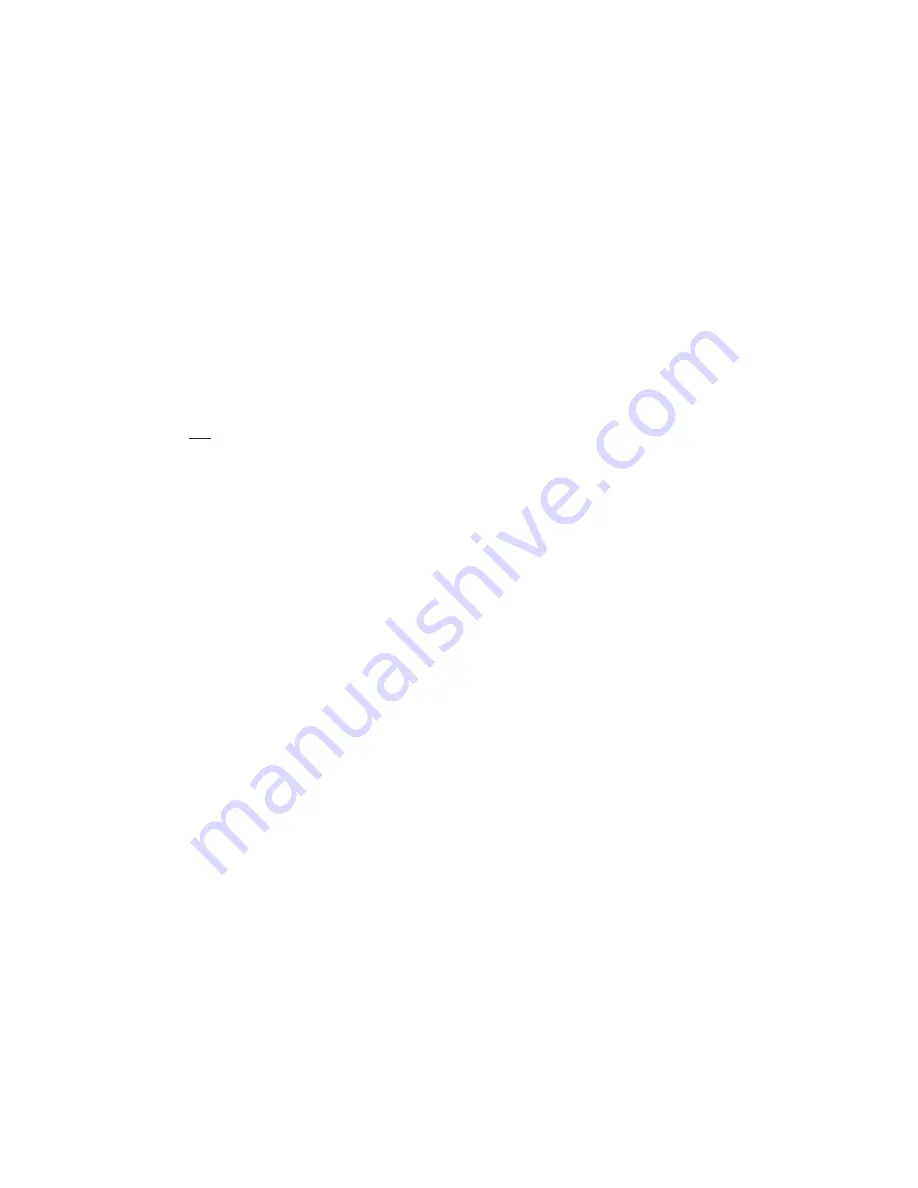
4
Solderability/ Soldering Process
The leads of the
devices
are gold plated for good solderabil-
ity and are compliant with
JEDEC standard
JESD22-B102.
The recommended soldering method for the AFBR-1012
transmitter and AFBR-2012 receiver devices is wave sol-
dering (260° C/ 5sec.)
The preconditioning for the qualification tests “Tempera-
ture Shock (TS)” and “Temperature Humidity Bias (THB)”
was done by dip soldering with a solder temperature of
260° C for 5 seconds (distance to package: 3 mm) accord-
ing to JEDEC standard J-STD-020D.
The qualification test “Resistance to soldering heat - Stan-
dard soldering technique (RSH-ST)” was done by dip sol-
dering with a solder temperature of 260° C for 10 seconds
(distance to package: 3 mm) according to JEDEC standard
JESD22-B106D.
The devices are not adapted for reflow soldering.
If SMD components are assembled on the same PCB the
AFBR-1012/-2012 devices shall be assembled afterwards.
They must not be subjected to reflow solder stress.
Note: This Application Note describes only the FOT solder-
ing. The device maker must also consider the maximum
temperature of the connector or pigtail.
Hand Soldering/ Rework
Hand soldering or rework is not allowed during an auto-
motive production process.
If hand soldering is necessary the following guidelines
must be considered:
x
Heating the devices to 100° C for 24 hours
x
Soldering time below 350° C must be limited to less
than 3 seconds.
x
Do not allow the lead temperature measured on the
lead close to the mold package to exceed 350° C.
Please note: Hand soldering and rework is a badly repro-
ducible process. Hand soldering may cause stresses in the
mold package, which affects optical performance and/or
reliability if the guidelines above are not observed.
Cleaning
The optical surface of the
devices
may get contaminat-
ed with dust and other contaminants during handling.
To regain optical performance of the device, the surface
must be cleaned.
While manually handling the devices, ESD protection
must be in place. To ensure solderability of the device, the
operator must wear finger cots.
Agents for cleaning or degreasing of the device are best
applied with a cotton bud on the optical surfaces. While
holding the device under a stereomicroscope, gently wipe
the dust or grease off. Dry compressed air is then used to
remove any residual.
Recommended chemicals:
x
Alcohols like methyl, isopropyl, isobutyl
x
Aliphatics like hexane or heptane
x
Soap
solutions
x
Naphtha
x
De-ionized
water
Do not use chemicals like:
x
(Partially) halogenated hydrocarbons
x
Ketones (eg. MEK)
x
Acetone
x
Chloroform
x
Ethyl
acetate
x
Phenol
x
Methylene
chloride
x
Methylene
dichloride
x
N-methylpyrrolidone
In general it is sufficient to use simple cleaning agents like
alcohols or soap solutions. More aggressive chemicals like
halogenated hydrocarbons are needlessly demanding
on the environment and are hazardous to human health.
Therefore, these should be avoided if possible.
Guidelines for optimum heat transfer to PCB
The PCB should be designed for optimum heat transfer
from the device's interior via the leads to the PCB (especial-
ly important for the GND and RES leads of the AFBR-1012
transmitter and the GND lead of the AFBR-2012 receiver as
these leads lead to active subcomponents). The distance
of the device body to the solder joint on the PCB shall also
be minimized and the dimensions of the conductors on
the PCB shall be maximized. Convection airflow around
the devices shall not be obstructed. Other heat generat-
ing devices shall not be placed near the devices.