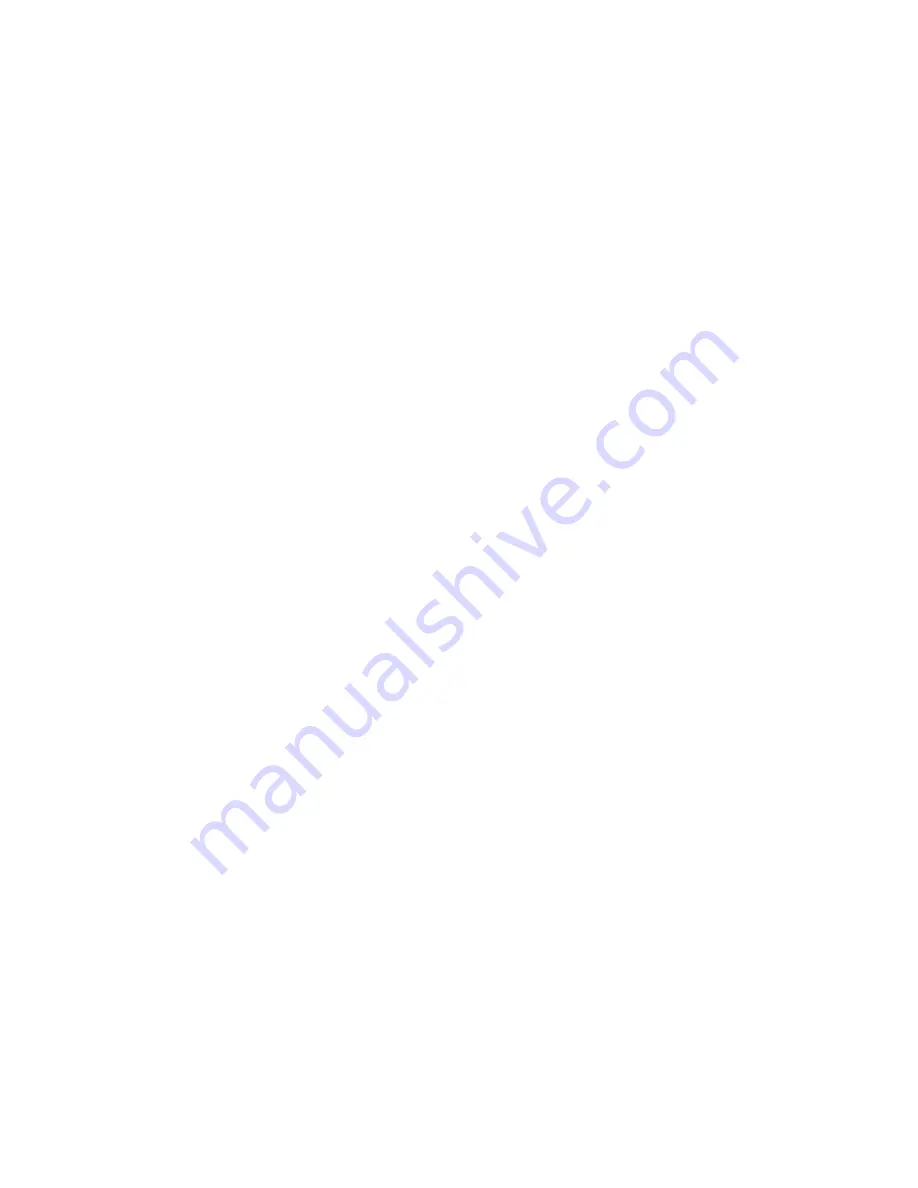
5
Regulatory Requirements
•
Passes FCC B and worldwide analogous emission limits
when assembled into a mouse with shielded cable
and following Avago Technologies recommendations.
•
Passes IEC-1000-4-3 radiated susceptibility level when
assembled into a mouse with shielded cable and
following Avago Technologies recommendations.
•
Passes EN61000-4-4/IEC801-4 EFT tests when assembled
into a mouse with shielded cable and following Avago
Technologies recommendations.
•
UL
fl ammability level UL94 V-0.
•
Provides suffi
cient ESD creepage/clearance distance
to avoid discharge up to 15kV when assembled into a
mouse according to usage instructions above.
Eye Safety
The ADNS-6010 and the associated components in the
schematic of Figure A1 are intended to comply with Class
1 Eye Safety Requirements of IEC 60825-1. Avago Tech-
nologies suggests that manufacturers perform testing to
verify eye safety on each mouse. It is also recommended
to review possible single fault mechanisms beyond those
described below in the section “Single Fault Detection”.
Under normal conditions, the ADNS-6010 generates the
drive current for the laser diode (ADNV-6340). In order to
stay below the Class 1 power requirements, resistor Rbin
must be set at least as high as the value in the bin table,
based on the bin number of the laser diode and LP_CFG0
and LP_CFG1 must be programmed to appropriate values.
Avago Technologies recommends using the exact Rbin
value specifi ed in the bin table to ensure suffi
cient laser
power for navigation. The system comprised of the ADNS-
6010 and ADNV-6340 is designed to maintain the output
beam power within Class 1 requirements over component
manufacturing tolerances and the recommended tem-
perature range when adjusted per the procedure below
and when implemented as shown in the recommended
application circuit of Figure A1. For more information,
please refer to Eye Safety Application Note 5088.
LASER Power Adjustment Procedure
1. The ambient temperature should be 25C +/- 5C.
2. Set VDD3 to its permanent value.
3. Ensure that the laser drive is at 100% duty cycle by
setting bit 6 of register 0x0A to 0.
4. Program the LP_CFG0 and LP_CFG1 registers to achieve
an output power as close to 506uW as possible without
exceeding it.
Good engineering practices should be used to guarantee
performance, reliability and safety for the product design.
LASER Output Power
The laser beam output power as measured at the naviga-
tion surface plane is specifi ed below. The following condi-
tions apply:
1. The system is adjusted according to the above
procedure.
2. The system is operated within the recommended
operating temperature range.
3. The VDD3 value is no greater than 50mV above its value
at the time of adjustment.
4. No allowance for optical power meter accuracy is
assumed.
Component Summary
Below is the summary of the components contained in
the ADNK-6013-SP01 Designer’s Kit.
Sensor
The sensor technical information is contained in the
ADNS-6010 Data Sheet.
Lens
The lens technical information is contained in the ADNS-
6120 Data Sheet. The fl ange on the standard ADNS-6120
lens is for ESD protection.
LASER Assembly Clip
The information on the assembly clip is contained in the
ADNS-6230-001 Data Sheet.
LASER
The LASER technical information is contained in the
ADNV-6340 Data Sheet and Application Note AN-5088.
Additional application notes regarding Eye Safety Re-
quirements are also available at Avago Technologies
website.
Base Plate Feature – IGES File
The IGES fi le on the CD-ROM provides recommended
base plate molding features to ensure optical alignment.
This includes PCB assembly diagrams like solder fi xture in
assembly and exploded view, as well as solder plate. See
Appendix D for details.
Reference Design Documentation – Gerber File
The Gerber File presents detailed schematics used in
ADNK-6013-SP01 in PCB layout form. See Appendix C for
more details.
Overall circuit
A schematic of the overall circuit is shown in Appendix A
of this document. Appendix B lists the bill of materials.