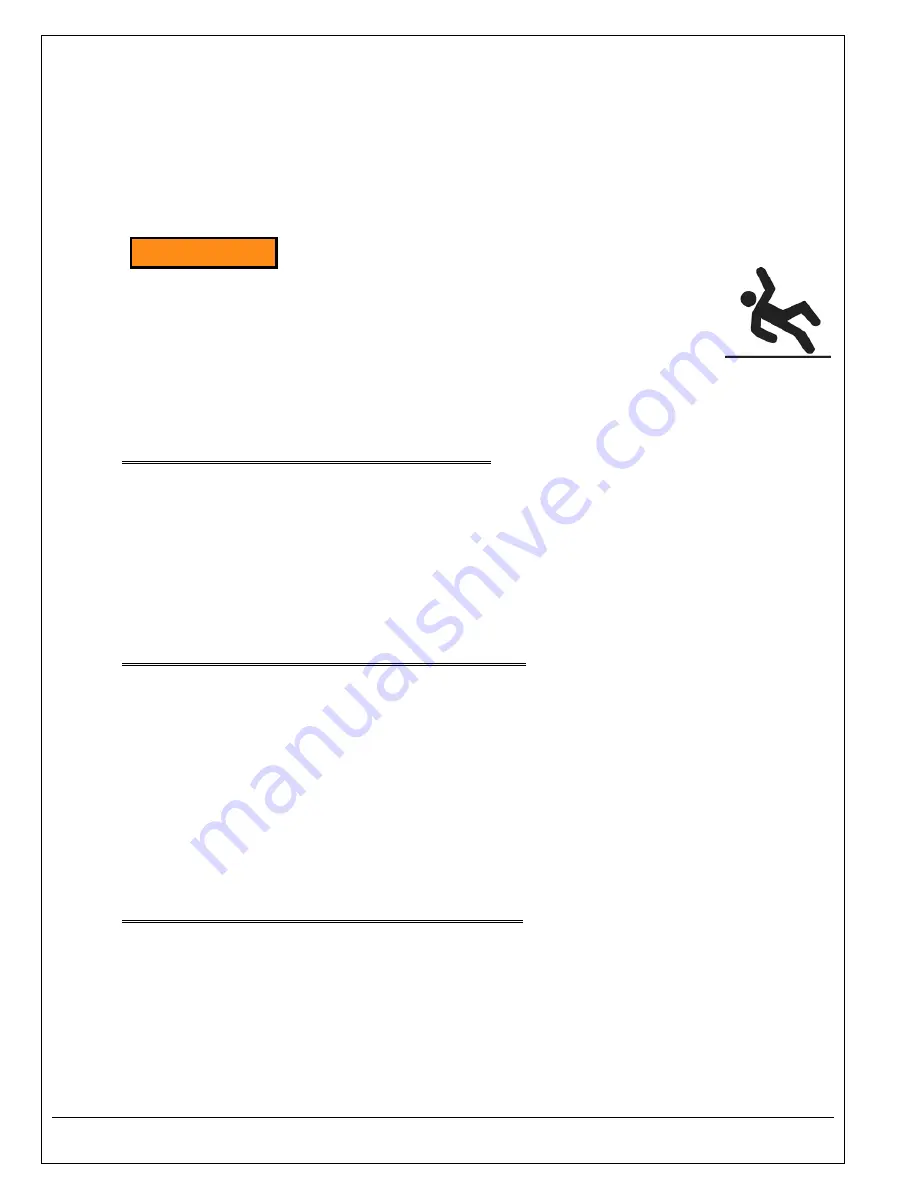
32
Hydraulic hoses can fail from age, damage and exposure.
Do not search for hydraulic leaks without body and face protection. A tiny,
almost invisible leak can penetrate the skin, requiring immediate medical
attention.
Use wood or cardboard to detect hydraulic leaks, never your hands.
Spilled hydraulic fluid is slippery and may also present a fire
hazard.
Clean up spilled hydraulic fluid.
Normally, scissor lifts will require very little maintenance. However, a routine maintenance program could
prevent costly replacement of parts and/or downtime.
6.2.1
Every Day Or 10 H
ours
Of O
peration
Check reservoir fluid level.
Check for fluid leaks.
Check all hoses and electrical cords for cracks, abrasions, twisting, etc. Small leaks at connections
can be remedied by tightening connections or replacing faulty component.
Check that oil pressure does not exceed 3,000 psi.
Check all pivot joints & roller bearings for noise and wear.
Check overall condition of unit (i.e. bends, breaks, loose or missing screws, etc.).
6.2.2
Every Month Or
100
Hours O
f
O
peration
Check quality of oil. Replace if discolored (oxidized), cloudy, or otherwise contaminated. Do not
overfill reservoir. Always use clean fluid.
Inspect lift cylinder rods for scoring and leaking, wipe away any foreign material.
Inspect all structural and mechanical components for cracked or broken welds and any distortion
caused by collision, overloading, or other misuse.
Inspect snap rings/bolts at rollers & pivot points for proper retention & tightness.
Inspect cylinder trunion pin for proper retention.
When all checks have been completed, start unit and operate through all functions. Inspect all
components for signs of noise, vibration, erratic movement, and any other abnormal behavior.
6.2.3
Every Year Or
1000
H
ours
Of O
peration
Change oil and clean reservoir. Always use clean fluid. Never return fluid from drip pans, pit, etc.
back to reservoir. Dispose of and handle used fluid as a hazardous material.
If noise or vibration has been noticed, remove lift cylinder pins, pivot pins, and roller bearings.
Inspect for wear and replace as necessary.
Inspect all hydraulic hoses. Replace any that show signs of wear or leaking.
Replace all filters.
Check for permanent mechanical deformation.
i
WARNING
Содержание PLTC-58120
Страница 13: ...13 1 DECAL_CAPACITY 2 36430050 3 36401487 4 36401560 5 06100010...
Страница 14: ...14 6 36403225 7 36400265 8 36400257 9 36403720 10 36433670...
Страница 17: ...17 PLT Pit Detail See Pit Installation Notes...
Страница 19: ...19 Lifting and Installation...
Страница 22: ...22 4 6 Bridge Lifting Chain Installation Steel Bridge...
Страница 23: ...23 4 7 Bridge Lifting Chain Installation Aluminum Bridge...
Страница 24: ...24 4 8 Bridge Winch Installation Steel Bridge...
Страница 25: ...25 4 9 Bridge Winch Installation Aluminum Bridge...
Страница 26: ...26 4 10 Pit Modification Installation for Mechanical Wheel Chock...
Страница 30: ...30 Figure 6 1...
Страница 35: ...35 Figure 6 3 Cylinder Seals...
Страница 38: ...38 6 3 5 Schematics and Field Wiring Details Electric Schematic 5HP 3Ph Contractor or Vertical Power Unit...
Страница 39: ...39 Electric Schematic 5HP 3Ph Continuous Running Vertical Power Unit...
Страница 40: ...40 Electric Schematic 5HP 1Ph 230V Vertical Power Unit...
Страница 41: ...41 Electric Schematic 3HP 1Ph 115V Vertical Power Unit...
Страница 42: ...42 Hydraulic Schematic Contractor Power Unit...
Страница 43: ...43 Hydraulic Schematic Vertical Power Unit...
Страница 44: ...44 Hydraulic Schematic Continuous Running Vertical Power Unit...
Страница 45: ...45 Push Button Wiring Diagram...
Страница 46: ...46 Guarded Foot Switch Wiring Diagram...
Страница 47: ...47 Guarded Foot Switch Assembly...
Страница 48: ...48 Optional Limit Switch Mounting Diagram PLTC 6050 to 6060...
Страница 49: ...49 Optional Limit Switch Mounting Diagram PLTC 6070 to 58150...
Страница 54: ...54 7 PARTS LISTS Contractor Power Unit...
Страница 55: ...55 Vertical Power Unit...
Страница 56: ...56 Continuous Running Vertical Power Unit...