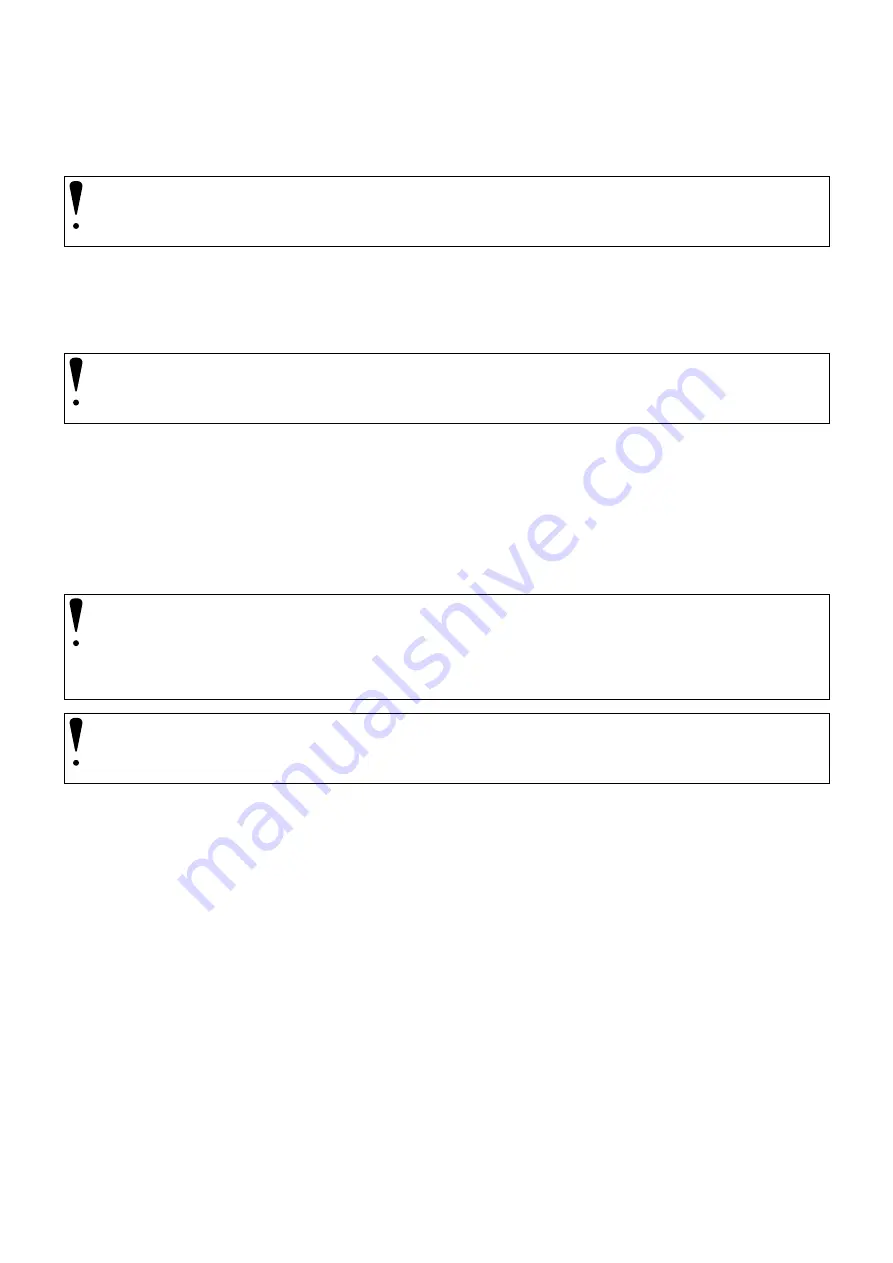
Check the oil separator insert. Check all hoses and tubes, replace them if necessary.
Assembly
Clean the jet/draw off tube and the insert gasket surface. Attach the new separator insert.
Warning
Do not remove a clamp from the antistatic gasket. It serves to ground any possible static electric charge. Do not
use sealing materials which could influence electric conductivity.
Fit the flange, mind the gasket and tighten the screws crosswise to recommended torque (see Tightening torques table).
Fit the flange with the draw off tube including the filter, reconnect the hoses and tubes to the flange.
Change compressor oil (see the following paragraph 15.25).
Warning
Start the machine (see paragraphs Before starting and Starting the machine at page 15) and check for leakage
before putting the machine back to operation.
OIL AND WATER COOLER
If grease, oil and impurities cumulate on the outer oil and water cooler surface, their efficiency is reduced. It is recommended
to clean the oil and water cooler with the compressed air stream from the outer side of the cooler once a month (it is possible
to use incombustible detergent). This should remove the cumulated grease, oil and impurities from the cooler, which would
therefore efficiently conduct the heat from oil and water away.
Warning
Hot coolant could cause serious injury. When adding coolant or antifreeze, stop the engine for at least one
minute before opening the cooler cap. Use gloves to protect your hands. Slowly loosen the tank cap and wipe
any released fluid with cloth. Do not open the tank cap until the excessive fluid does not flow away and the
cooling system is not fully unpressurised.
Warning
Follow the instructions of the antifreeze manufacturer for refilling or releasing the antifreeze. It is recommended
to use personal protective equipment and avoid skin and eye contact with the antifreeze.
COMPRESSOR DRIVE
Twisting moment transmission from the engine to the air end is provided by a toothed belt.
Maximum belt bending (Gates Power Grip GT2 / 600-8MGT-30) in the middle of its traction strand should be 7,5 mm under
pressure of 49, 2
÷
56, 3 N (79, 5
÷
84, 9 Hz).
Maximum belt bending (Contitech Synchroforce CXP III HDT 1280-8M-30) should be 80, 7
÷
89, 3 Hz.
Check the belt bending according to the maintenance intervals (see Maintenance schedule on page 41 ).
Use a tightening screw to tighten the belt.
ALTERNATOR BELT
Use a tightening screw to tighten the alternator belt.
Use a tightening screw to set the belt bending to approx. 5 mm when the belt is pushed down by a thumb. Secure the
alternator.
At 2020/N
X.11.2016
34