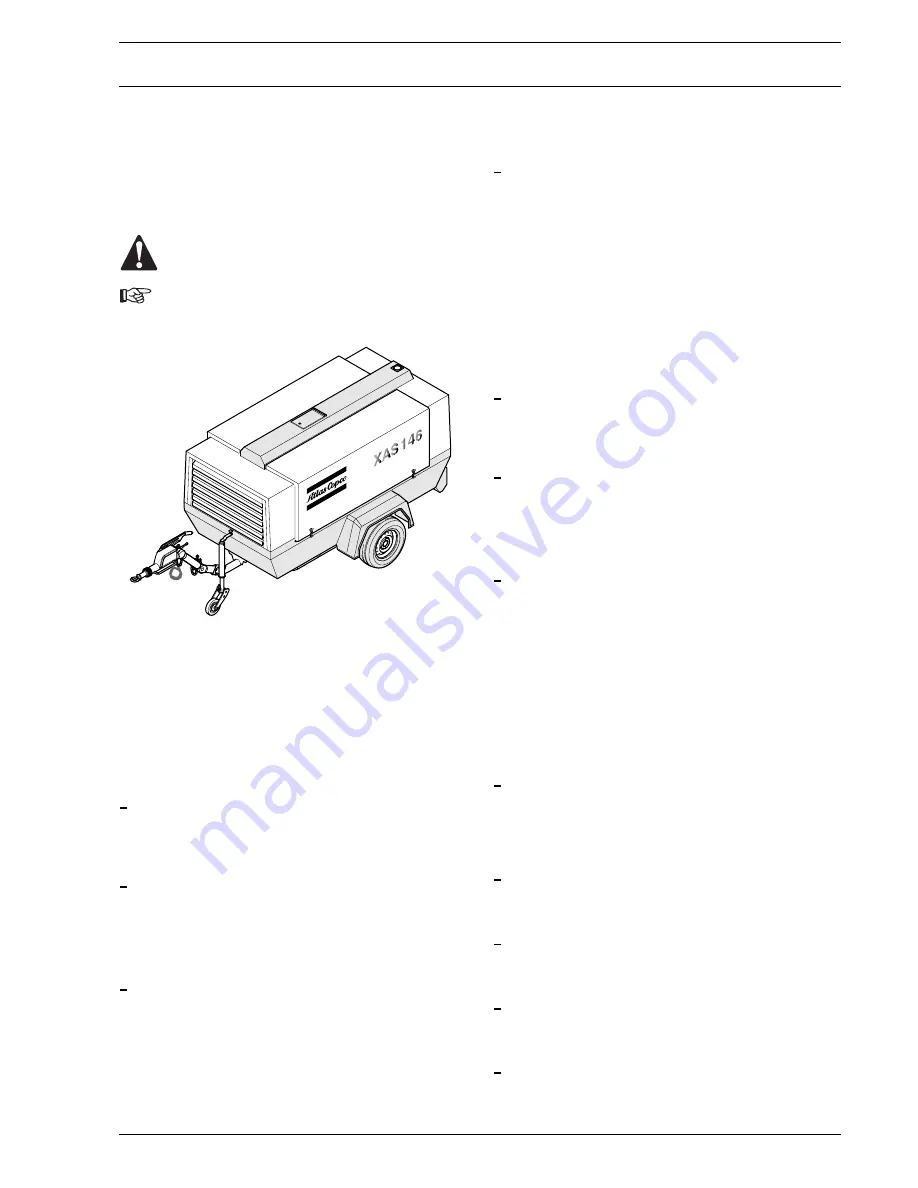
+
05647%6+10
/
#07#.
9
.'#&+0)2#46+%7.#45
&
'5%4+26+10
1(
5#('6;
2+%61)4#/5
75'&
+0
6*+5
/#07#.
Fig. 2.1
General view of XAS146
(adjustable towbar with brakes and jockey wheel are options)
)
'0'4#.
&'5%4+26+10
The XAS146 Dd is a silenced, single-stage, oil-injected screw
compressor, built for a nominal effective working pressure of 7 bar
(non-silenced version XA146 Dd).
The XAHS106 Dd is built for a nominal effective working pressure
of 12 bar.
'PIKPG
The compressor is driven by a water-cooled diesel engine.
The engine’s power is transmitted to the compressor through a heavy-
duty coupling.
%QORTGUUQT
The compressor casing houses two screw-type rotors, mounted on ball
and roller bearings. The male rotor, driven by the engine, drives the
female rotor. The element delivers pulsation-free air.
Injected oil is used for sealing, cooling and lubricating purposes.
%QORTGUUQTQKNU[UVGO
The oil is boosted by air pressure. The system has no oil pump.
The oil is removed from the air, in the air/oil vessel first by centrifugal
force, second through the oil separator element.
The vessel is provided with an oil level indicator.
4GIWNCVKQP
The compressor is provided with a continuous regulating system and
a blow-down valve which is integrated in the unloader assembly. The
valve is closed during operation by air receiver pressure and opens by
air receiver pressure via the compressor element when the compressor
is stopped.
When the air consumption increases, the air receiver pressure will
decrease and vice versa.
This receiver pressure variation is sensed by the regulating valve
which, by means of control air to the unloader and engine speed
regulator, matches the air output to the air consumption. The air
receiver pressure is maintained between the pre-selected working
pressure and the corresponding unloading pressure.
%QQNKPIU[UVGO
The engine is provided with a water cooler and the compressor is
provided with an oil cooler.
The cooling air is generated by a fan, driven by the engine.
5CHGV[FGXKEGU
A thermal shut-down switch protects the compressor against
overheating. The air receiver is provided with a safety valve.
The engine is equipped with low oil pressure and high coolant
temperature shut-down switches.
(TCOGCPFCZNG
The compressor/engine unit is supported by rubber buffers in the
frame.
The standard unit has a non-adjustable towbar with a towing eye.
As an option the unit can be equipped with an adjustable towbar, an
overrun and parking brake and towing eyes type AC, DIN, ball, ITA,
GB, NATO.
For available options see chapter
1
.
The new braking system consists of an integrated parking brake and
overrunbrake. When driving backwards the overrunbrake is not
engaged automatically.
$QF[YQTM
The bodywork has openings at the shaped front and rear end for the
intake and outlet of cooling air and hinged doors for maintenance and
service operations. The bodywork is internally lined with sound-
absorbing material.
.KHVKPIG[G
A lifting eye is accessible when a small door at the top of the unit is
unlocked.
%QPVTQNRCPGN
The control panel grouping the air pressure gauge, control switch etc.,
is placed at the right hand/ rear end corner.
&CVCRNCVG
The compressor is furnished with a data plate showing the product
code, the unit serial number and the working pressure (see chapter
1
).
5GTKCNPWODGT
The serial number is located on the right-hand side towards the front
on the upper edge of the frame.
7KLVV\PEROGUDZV\RXUDWWHQWLRQWRGDQJHURXV
VLWXDWLRQV7KHRSHUDWLRQFRQFHUQHGPD\HQGDQJHU
SHUVRQVDQGFDXVHLQMXULHV
7KLVV\PEROLVIROORZHGE\VXSSOHPHQWDU\LQIRUPDWLRQ
Содержание XA146 Dd
Страница 2: ... 5 5 2 ...