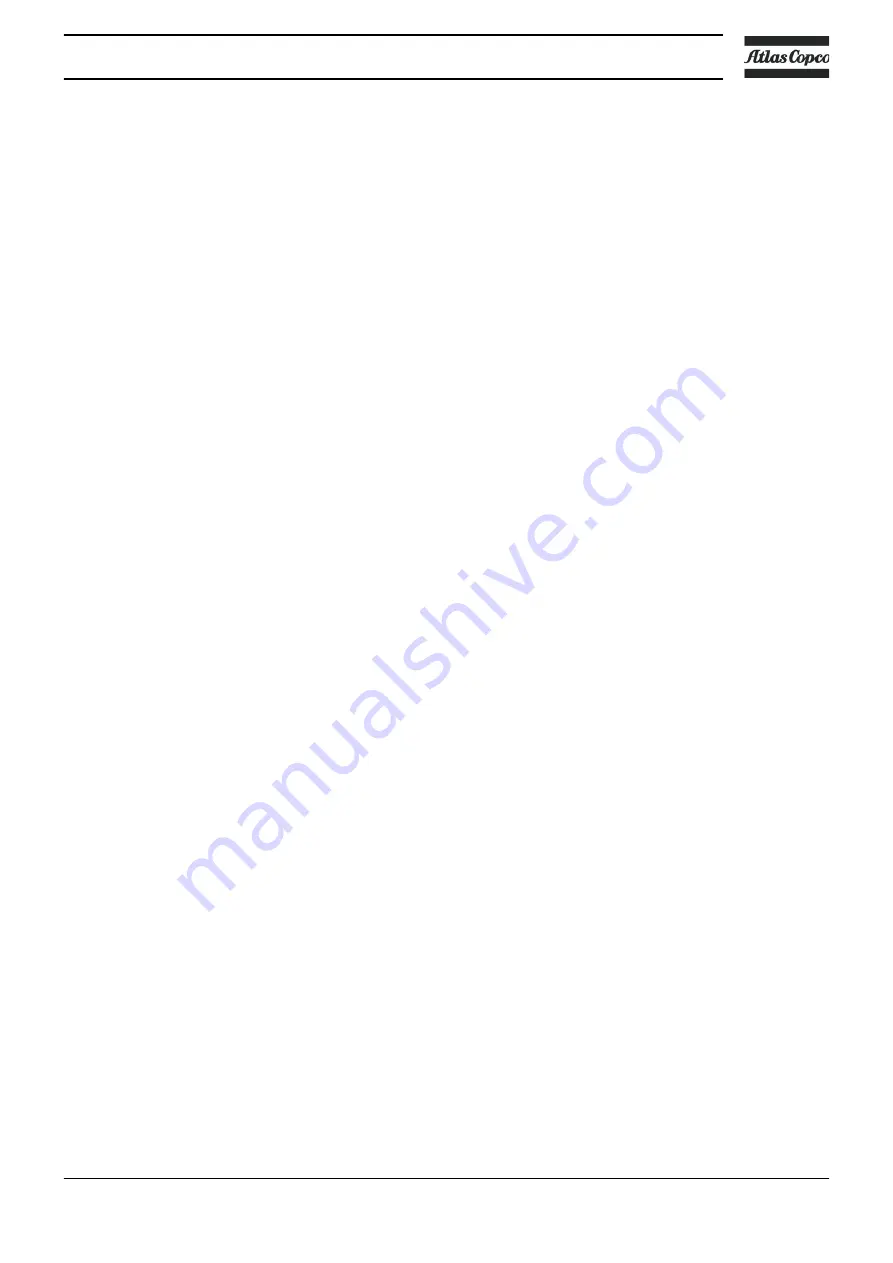
.................................................................................................35
.........................................................................................42
....................................................................... 43
............................................................................................ 43
Instruction book
2920 7110 11
3
Содержание SF 1
Страница 1: ...Atlas Copco Oil free scroll compressors SF 1 SF 2 SF 4 SF 6 Instruction book ...
Страница 2: ......
Страница 53: ......