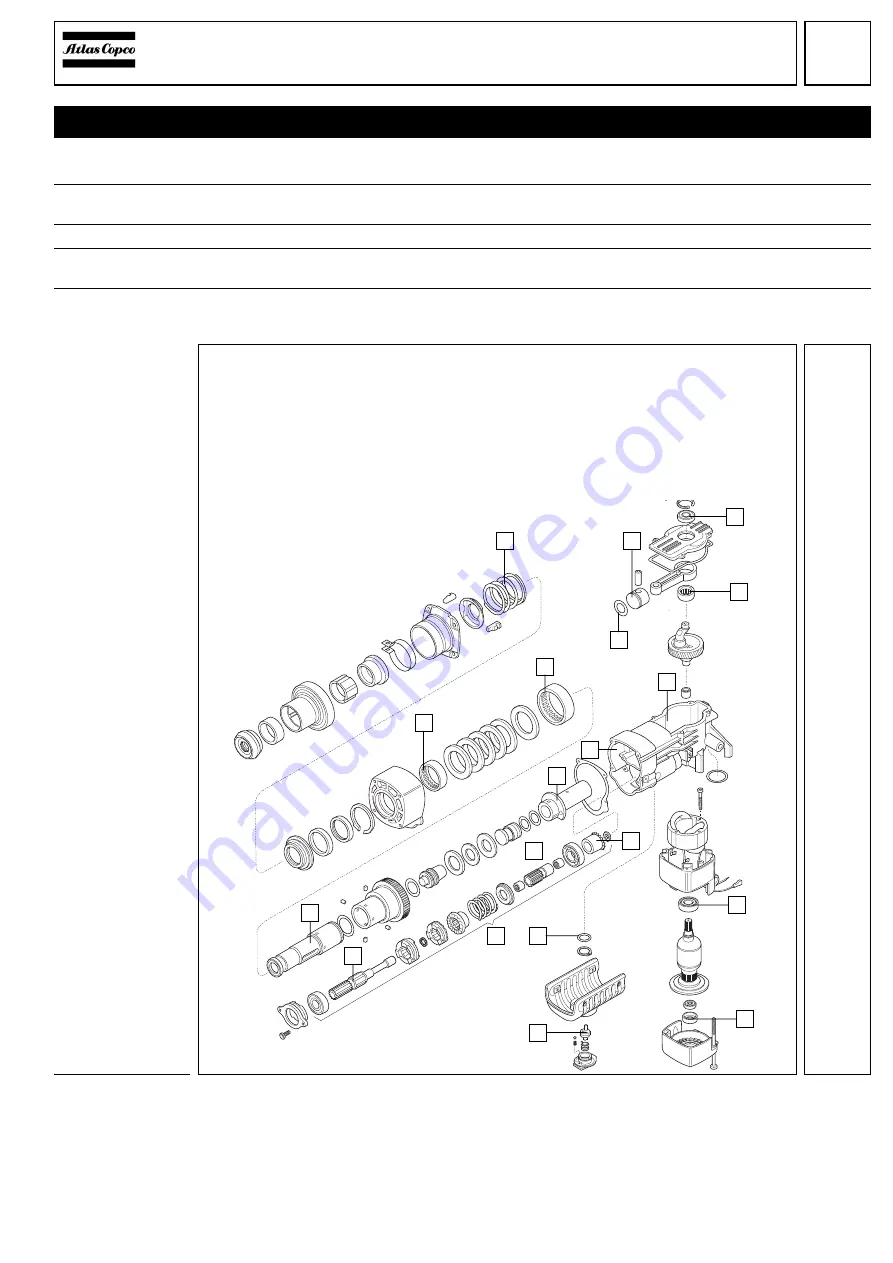
6
PAGE
Repair Instructions No.189.03/01
PHE 45 S
Maintenance
General
It is recommended that maintenance be performed on the machine at regular intervals or when the
carbon brushes switch off at the latest.
Cleaning
Clean all parts – with the exception of the electrical parts – with cold cleaning agent. Caution! No
cleaning agent should penetrate into the bearing. Clean the electrical parts with a dry brush.
Check for wear
Check the disassembled parts for wear (visual inspection) and replace worn parts.
Electrical tests
Before reassembling, perform an electrical test on all relevant parts (see chapter Electrical and
Mechanical Test Instructions).
Lubrication
Each time maintenance is performed, the machine is to be lubricates as stated in the lubrication plan.
After the machine is fully disassembled, completely remove the old grease and replace with new
grease. The grease must be applied to the machine as indicated in the lubrication plan.
Legend
Distribute the grease type N (125 g) from the maintenance set as follows:
A
Thinly daub
B
Generously cover
C
Fill with 43 g grease
D
Fill with 28 g grease
Torques
Screws in plastic
1.8 Nm
Screws in metal
4.0 Nm
Gear box screws
15.0 Nm
■
Use locking agent for all metal housing screws!
B
B
B
B
C
B
A
A
B
B
A
B
D
C
C
A
B
C
D
Содержание PHE 45 S
Страница 1: ......