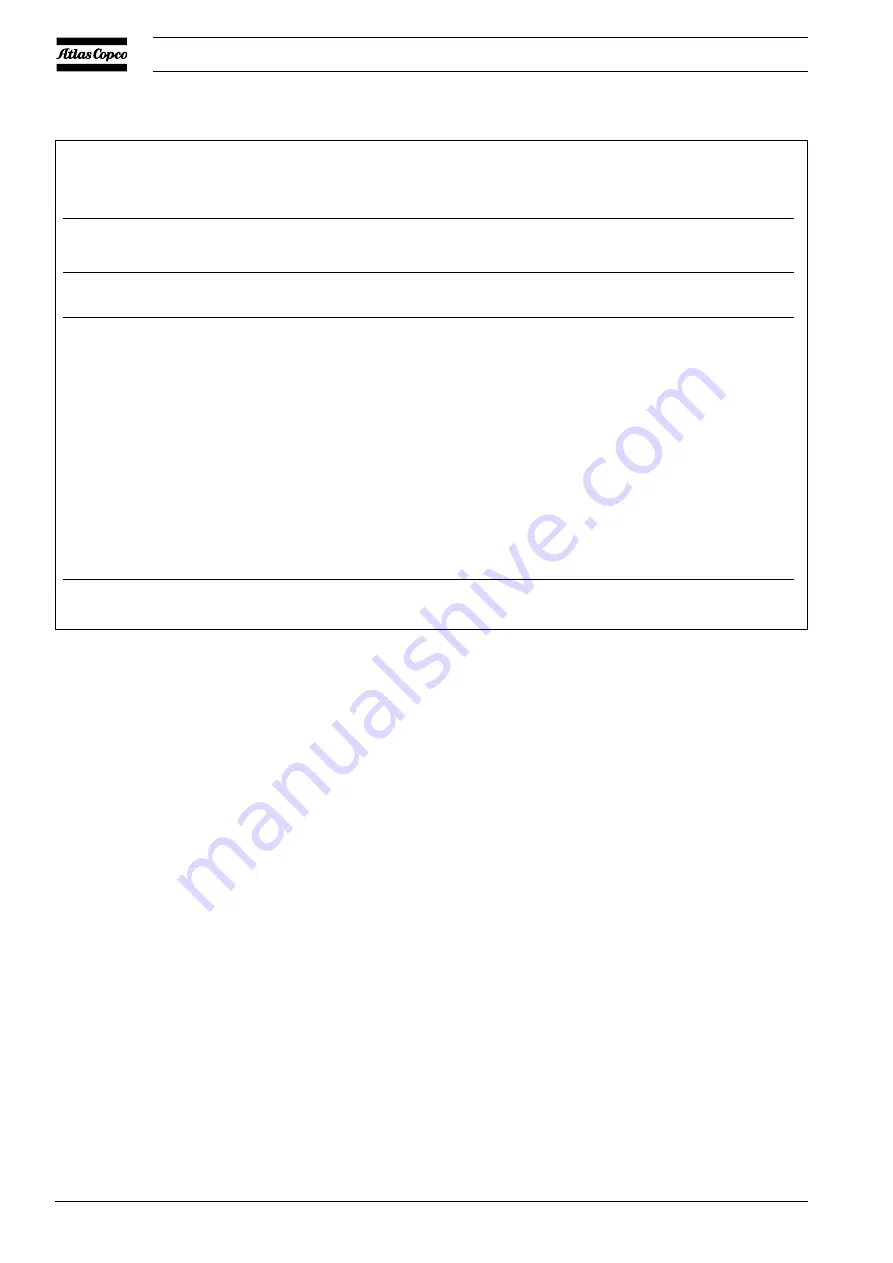
2920 1454 00
22
Instruction book
Notes
1. More frequently when operating in a dusty atmosphere. Replace damaged or heavily contaminated elements.
2. Use genuine Atlas Copco filters.
3.
The interval for Service plan A is to be reduced to the mentioned interval in case mineral oil is used instead of Roto-
injectfluid. Consult the "User manual for Elektronikon regulator", section "Modify settings".
4. Recommended oil: Atlas Copco Roto-injectfluid. For the change interval in extreme conditions of temperature, humidity
or cooling air, consult Atlas Copco.
5. Or when the pressure drop over the separator exceeds 1 bar. See "User manual for Elektronikon regulator", section
"Measured data menu" to call up this value. Check the pressure drop when the compressor is running loaded and preferably
with a stable working pressure.
6. Any leakage should be attended to immediately. Damaged flexibles or flexible joints must be replaced.
7. See "User manual for Elektronikon regulator", section "Test menu".
8. See "User manual for Elektronikon regulator", section "Modify settings menu".
Decrease the shut-down warning level and shut-down level for the compressor element outlet temperature to the minimum
settings. Run the compressor: when reaching the setting, the unit must shut down. Afterwards, reset the warning and shut-
down levels to their original values.
4.2 Compressor motor (1-Fig. 3.2)
The correct type of grease can be ordered from Atlas Copco
(see section 4.8).
The bearings must be regreased with KLÜBERQUIET BQH
72 - 102.
Quantity: 24 g per bearing
Running
See
See notes
Service
Operation
hours
section
below
plan
table
4000
4
2/4
A
If Atlas Copco Roto-injectfluid is used, change oil and oil filter
1000
4
2/4/3
A
If oil as specified in section 4.4.2 is used, change oil and oil filter
4000
--
-
B
Check pressure and temperature readings
"
--
7
B
Carry out a LED/display test
"
--
6
B
Check for possible air or oil leakage
"
4 and 5
2
B
Replace air filter element
"
--
-
B
Remove, dismantle and clean float valve of condensate trap
"
4
-
B
Re-grease bearings of drive motor as specified
"
--
-
B
Check blow-off solenoid valve (Y1) after stopping and pressing the
emergency stop button
"
--
8
B
Test temperature shut-down function
"
5
-
B
Have the safety valve tested
"
--
-
B
Clean cooling fins of electric motors
"
--
-
B
Inspect restrictor in scavenging line for cleanness
"
5
-
B
Clean air and oil coolers
8000
--
5
C
Have oil separator replaced
Service plans
To regrease the motor
(Fig. 3.3) loosen palm grip (3), lift
nozzle (2) and turn it 90 degrees clockwise (automatic
operation pictograph covered and grease pump pictograph
visible); tighten the palm grip. Run the Regreasing program
from the Test submenu on the regulator. When the regreasing
program has finished, loosen the palm grip, lift the nozzle and
turn it back into its original position (grease pump pictograph
covered and automatic operation pictograph visible), tighten
the palm grip.