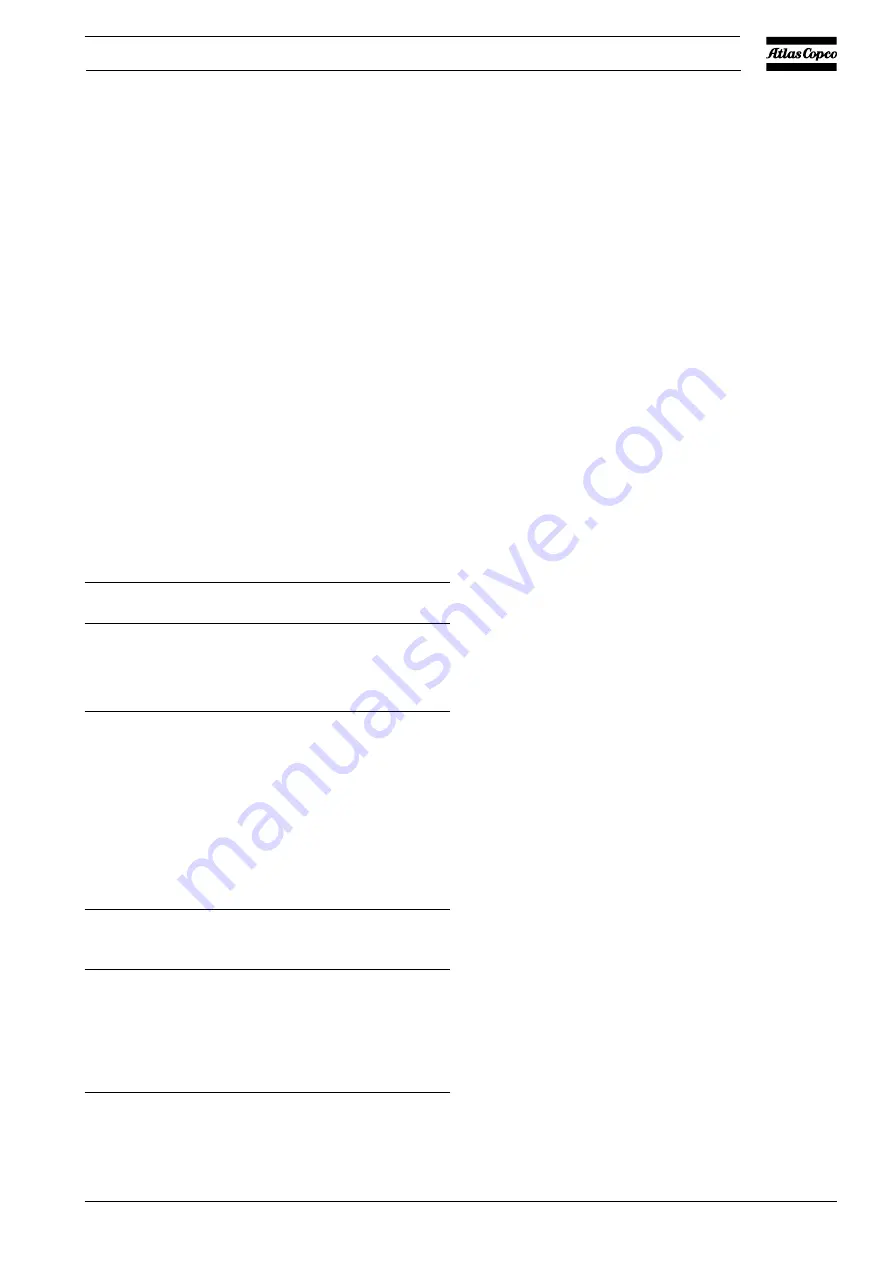
2920 1454 00
23
Instruction book
During the Regreasing program, the compressor will run for
30 minutes at minimum speed. The compressed air is blown
off via the solenoid valve.
The compressor can be put into operation again by pressing
the start button. Reset the regulator as described in the "User
manual for Elektronikon regulator", section "Service reset".
4.3 Oil and oil filter change interval
Consult section 4.1 for the change intervals and section 4.4
for the oil specifications.
4.4 Oil specifications
4.4.1 Atlas Copco Roto-injectfluid
It is strongly recommended to use Atlas Copco Roto-
injectfluid. This is special oil for screw compressors which
keeps the compressor in excellent condition.
Atlas Copco Roto-injectfluid can be ordered in following
quantities:
Quantity
Ordering number
5-litre can . . . . . . . . . . . 2901 0245 01
20-litre can . . . . . . . . . . 2901 0522 00
209-litre drum . . . . . . . . 2901 0045 01
4.4.2 Mineral oil
Although Roto-injectfluid is recommended, a high-quality
mineral oil with oxidation inhibitors and anti-foam and anti-
wear properties can also be used after taking some precautions.
The oil system should first be drained and flushed. The
viscosity grade must correspond to the ambient temperature
and ISO 3448, as follows:
Ambient
Viscosity
Viscosity
temperature
grade
index
Consistently above 25 degrees
Celsius
ISO VG 68 Minimum 95
Between 25 and 0 degrees
Celsius
ISO VG 32 Minimum 95
or 46
Attention
Never mix oils of different brands or types. Use only non-
toxic oils.
4.5 Oil change (Fig. 3.1)
1. Run the compressor until warm.
Stop the compressor,
press the emergency stop button (S3-Fig. 1.1), close
the air outlet valve, open manual drain valves (1 and
4-Fig. 1.5) and wait until the compressor has
depressurized.
Unscrew oil filler plug (3) only one turn
to permit any pressure in the system to escape.
2. Remove vent plug (5-Fig. 1.4). Drain the oil by removing
drain plugs (4-Fig. 3.1 and 2-Fig. 3.4). Collect the oil in a
collector and deliver it to the oil collection service. Fit
and tighten the drain plugs after draining.
3. Fill air receiver (6) with oil until the level reaches the filler
neck. Take care that no dirt drops into the system. Reinstall
and tighten filler plug (3) and vent plug (5-Fig. 1.4).
4. Run the compressor for a few minutes.
Stop the
compressor and press the emergency stop button to
depressurize the compressor.
Wait a few minutes to allow
the oil to settle. Unscrew oil filler plug (3) only one turn
to permit any pressure in the system to escape. Fill the air
receiver with oil until the level reaches the filler neck. Fit
and tighten filler plug (3).
5. Reset the oil service warning
2)
.
4.6 Oil filter change (Fig. 3.1)
1. Close the air outlet valve and let the compressor run at
minimum speed for 3 minutes.
Stop the compressor, press
the emergency stop button (S3-Fig. 1.1) and open
manual drain valves (1 and 4-Fig. 1.5). Wait until the
compressor has depressurized. Unscrew oil filler plug
(3) only one turn to permit any pressure in the system
to escape.
2. Remove vent plug (5-Fig. 1.4), wait 5 minutes, remove
drain plug (2-Fig. 3.4) of the check valve/oil stop valve.
Catch the oil in a receptacle.
3. Remove oil filter (1-Fig. 3.1).
4. Clean the filter seat on the manifold. Oil the gasket of the
new element. Screw the element into place and tighten it
firmly by hand.
5. Tighten the plug in the check valve/oil stop valve.
6. Fill the receiver (6) with oil until the level reaches the filler
neck. Fit and tighten plug (3) and vent plug (5-Fig. 1.4).
7. Reset the oil filter service warning.
2)
4.7 Storage after installation
Run the compressor twice a week until warm.
If the compressor is stored without running from time to time,
protective measures must be taken. Consult Atlas Copco.