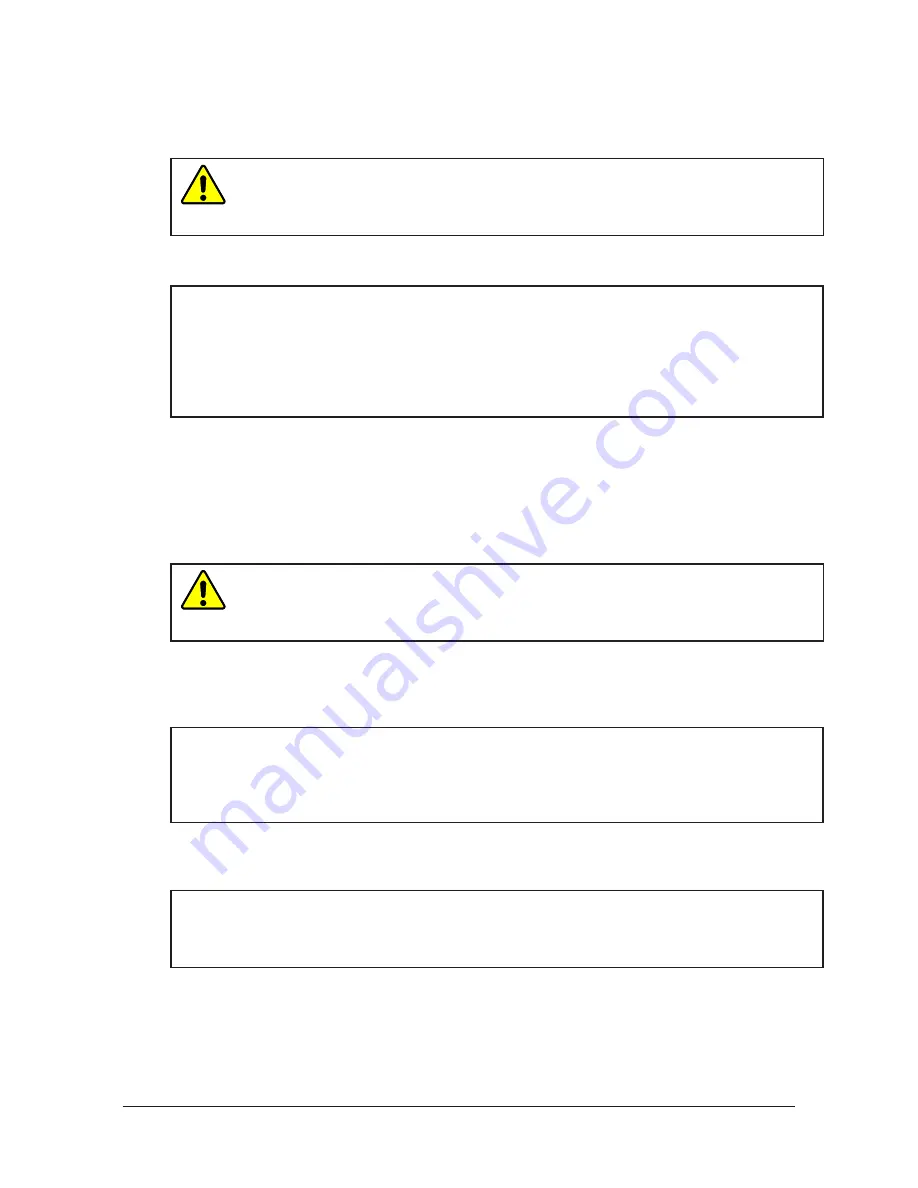
Manual, Tool Changer, QC‑113
Document #9620‑20‑B‑113 Base Tool Changer‑05
Pinnacle Park • 1031 Goodworth Drive • Apex, NC 27539 • Tel: 919.772.0115 • Fax: 919.772.8259 •
www.ati‑ia.com
B-15
3.1 Conditions for Coupling
The following conditions should be considered when operating the Tool Changer. For more details about
programming the robot, refer to the Operation section of the Control/Signal Module Manual.
CAUTION:
Do not attempt to couple the Tool Changer when in locked position. The
locking mechanism must be in the unlock position when attempting to couple the Tool
Changer. Failure to adhere to this condition may result in damage to the unit and/or the
robot. Always unlock the Master prior to coupling to a Tool.
1. Unlock the Tool Changer by removing air pressure from the lock port and supplying air pressure to the
unlock port (if equipped, the unlock sensor indicates the Tool Changer is unlocked).
NOTICE:
For Tool Changers with a control/signal module and air/valve adapters with a double
solenoid valve, turn the Unlatch output ON and turn the Latch output OFF. For Tool Changers
with a control/signal module and air/valve adapters with a single solenoid valve, turn the Unlatch
output ON. Some control/signal modules prevent the Tool Changer from being unlocked unless
the Master and Tool are coupled and nested properly in the tool stand, a manual override
procedure is required to unlock the Tool Changer. Refer to your Control/Signal Module Manual
for instructions.
2. Position the Master above the Tool and move the Master into ready to lock position. The mating surfaces
of the Master and Tool should be parallel and not touching. Make sure that the tapered alignment
pins from the Master enter the alignment holes on the Tool. The alignment pins should be relatively
concentric with the alignment bushings with no contact between the two.
3.
It is recommended that the mating faces of the Master and Tool not be touching but be within the No-
Touch distance of each other when coupling to minimize stress and wear on the locking mechanism. The
locking mechanism allows the Master to “pull up” the Tool with gaps between the two sides.
CAUTION:
Direct contact of the Master and Tool mating surfaces is not suggested
or required just prior to coupling. Contact may result in damage to the unit and/or the
robot. No-Touch locking technology allows the unit to couple with a separation distance
between the Master and Tool.
4. The RTL (Ready-To-Lock) sensor and target that are built into the Tool Changer must be positioned
within approximately 0.05” (1.5 mm) of each other for the sensors to detect Tool presence. RTL signals
are not required to couple the Tool Changer but are recommended as a confirmation of coupling prior to
removing the Tool from the tool stand.
NOTICE:
At this point, communication is initiated with the ATI Tool and downstream nodes.
If equipped, Tool-ID and communications become available. Depending on the type of
control/signal module, additional notifications such as RTLV, TSRV, TSIV, Tool Present,
Unlatch Enabled, and other notifications can provide verification of properly functioning
system components.
5. Couple the Tool Changer by releasing the air pressure from the unlock port and supplying air pressure
to the lock port. Air must be maintained on the lock port during operation to assure rigid coupling (if
equipped, the lock sensor indicates the Tool Changer is in the locked position).
NOTICE:
For Tool Changers with a control/signal module and air/valve adapters with a double
solenoid valve, turn the Unlatch output OFF and turn the Latch output ON. For Tool Changers
with a control/signal module and air/valve adapters with a single solenoid valve, turn the
Unlatch output OFF.