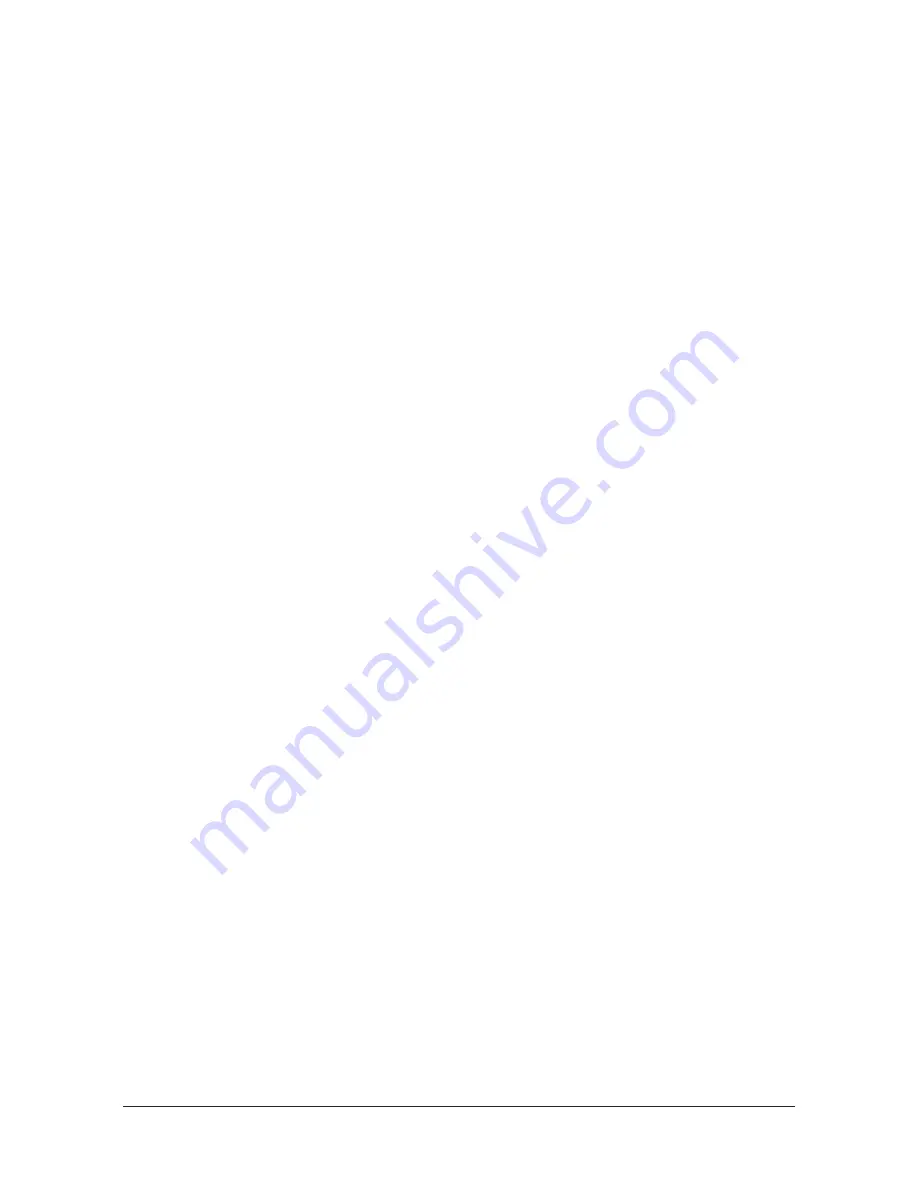
Manual, Control Module, PROFINET, DL12
Document #9620-20-C-DL12-06
Pinnacle Park • 1031 Goodworth Drive • Apex, NC 27539 • Tel: 919.772.0115 • Fax: 919.772.8259 •
C-25
4.2 Inputs
The following describes the most critical inputs from the ATI Master module.
4.2.1 EVERYTHING IS OK
This is an overall status bit that indicates if there is an error condition that will block an unlatch
request. This bit is high as long as there are no errors.
4.2.2 Locked
An input indicating that the coupling mechanism is in the Lock position. The “LOCKED” bit in the
PROFINET bitmap will only be set high if the following conditions are on:
•
LOCKED sensor input is high
•
UNLOCKED sensor input is low
• TOOL PRESENT input is high
4.2.3 Latch Enabled
The Latch Enabled bit indicates when the preconditions for latching the Tool Changer have been
met. The preconditions include:
• No Errors
• Input and Output Power within operating range (20.4‑28.8 V).
• Air pressure within operating range (60‑100 psi).
• UNLATCH bit is off
• LATCH bit is off
4.2.4 RTL1 and RTL2
Proximity sensor inputs that indicate the Tool Changer Master is close to the Tool. It is
recommended that these inputs be used to indicate when it is okay to couple the Tool Changer.
These proximity sensors are installed in the Master body and sense targets in the Tool body that
indicate the Master is adjacent to the Tool (within ~ 0.06” or 1.5 mm).
4.2.5 SSO 1 and SSO 2
Discrete inputs from the safety switch, which are high when the Tool Changer is in the stand.
4.2.6 SS Pulse Missing
A bit indicating the TSI Safety Switch is bypassed or SSO_1 is shorted to 24 volts. This bit will
clear when the bypass is removed or the SSO_1 short is fixed. This bit does not prevent latching or
unlatching.
4.2.7 Tool Power Is On
The Tool Power Is On bit indicates that the Arc Prevention circuit has turned power on to the Tool
side.
4.2.8 Tool Present
An input indicating the Master module is electrically connected to the Tool.