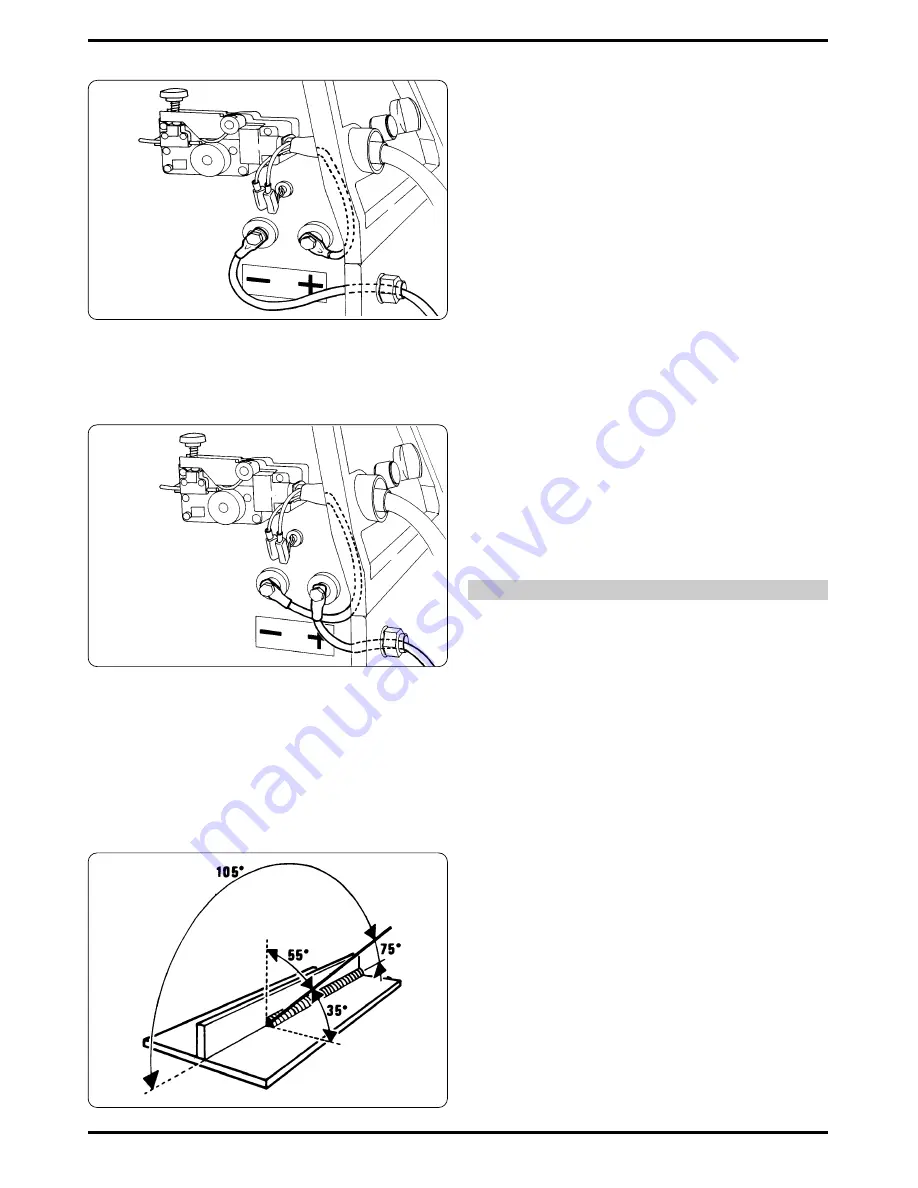
4
When you have finished welding, turn off the machine and
close the gas cylinder.
For the correct welding angle see figure 5.
5.1.2
Without gas protection.
Connect the cables as shown in the figure 4.
Use only diam. 0.9 flux cored wire that complies with the
standard AWS AS.20 E71 TII or E71 TGS, suitable for use
without gaseous protection.
Connect the earth cable clamp to the workpiece.
After connecting the cables, follow the instructions given in
paragraph 5.1.1.
NOTE: For compact, well-protected welds always work
from left to right and from top to bottom.
Remove all waste after each welding operation.
For the correct welding angle see figure 5.
5.2
WELDING ALUMINIUM
The welding machine must be prepared as for welding
mild steel with gas protection, but with the following differ-
ences:
- 100% ARGON as the protection gas for welding.
- A wire having a composition suited to the base material
to be welded.
For welding ALLUMAN: 3÷5% silicon wire
- For welding ANTICORODAL: 3÷5% silicon wire
- For welding PERALUMAN: 5% magnesium wire
- For welding ERGAL: 5% magnesium wire
Use grinding wheels and brushes specifically designed for
aluminium, and never use them on other materials.
REMEMBER that cleanliness is quality!
The wire reels must be stored in nylon bags with dehu-
midifying packets.
For the correct welding angle see figure 5.
5.3 WELDING STAINLESS STEEL
The welding machine must be prepared as for welding
mild steel with gas protection, but with the following differ-
ences:
- Reel of stainless steel wire compatible with the compo-
sition of the material to be welded.
- Cylinder containing 98% ARGON + 2% 02 (recommend-
ed composition)
The recommended torch angle and welding direction are
shown in figure 5.
6 MAINTENANCE AND CHECKS
6.1 GENERAL NOTES
l
Turn off the welding machine and unplug the power cord
from the socket before each checking and maintenance
operation.
l
Moving parts can cause serious lesions
l
Keep away from moving parts.
l
INCANDESCENT SURFACES can cause serious burns.
l
Let the unit cool before servicing.
l
Periodically remove any dust or foreign matter that may
have deposited on the transformer or diodes; to do so, use
a jet of clean, dry air.
l
When replacing the wire roller, make sure the groove is
aligned with the wire and corresponds to the diameter of
the wire used.
l
Always keep the interior of the gas nozzle clean to avoid
metal bridges created by welding dross between the gas
nozzle and the contact tip. Make sure the outlet hole of the
contact tip has not expanded excessively; if so, replace.
l
Strictly avoid striking the torch or allowing it to suffer vio-
lent impact.
6.2 REPAIRING THE WELDING MACHINE
Experience has shown that many accidents are caused by
repairs performed incorrectly. That is why it is just as
important to check a repaired welding machine carefully
and completely as it is for a new welding machine.
In addition, this protects the manufacturer from being held
liable for defects when the true fault lies elsewhere.
Fig. 5
Fig. 3
Fig. 4