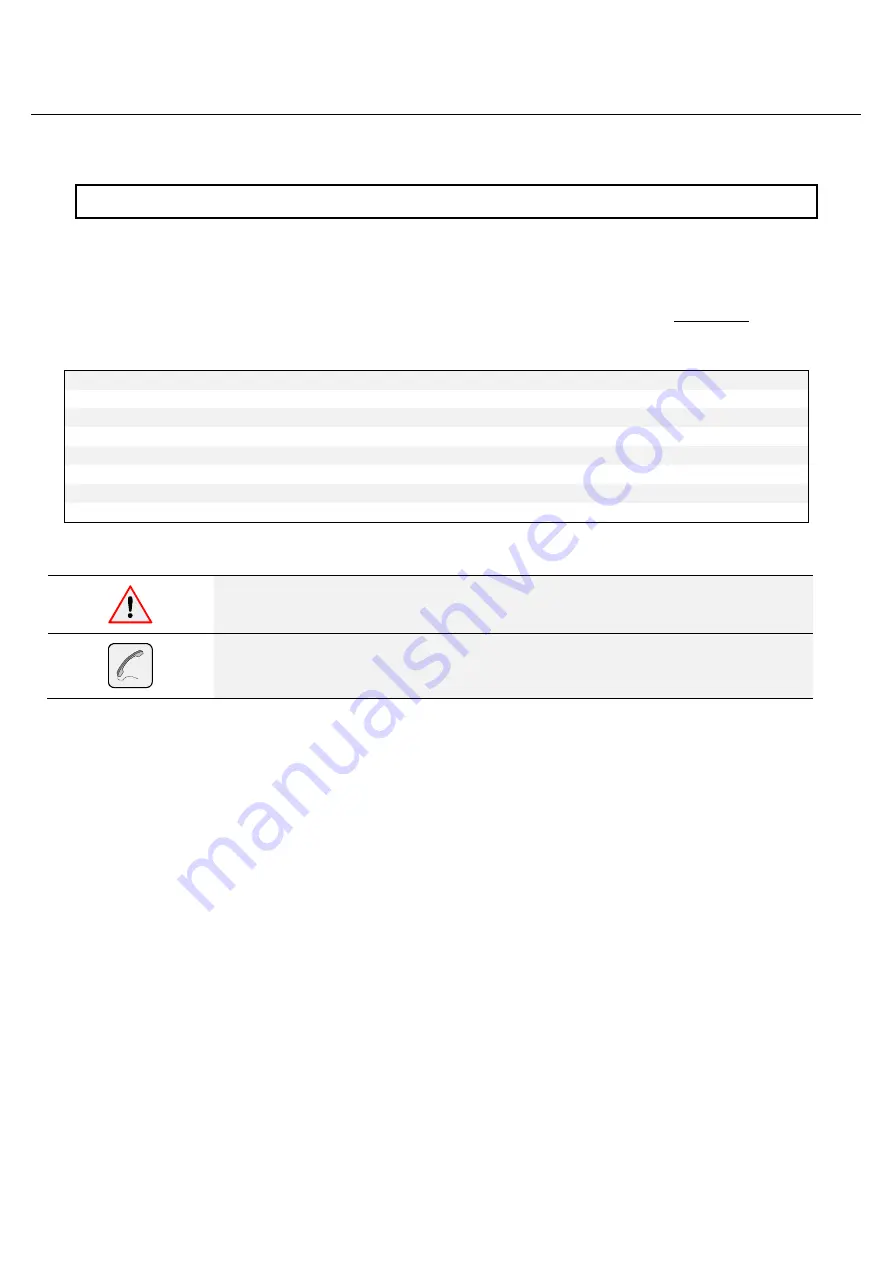
AT-OS S.r.l.
Viale del Lavoro, 19 37030 Colognola ai Colli (Verona) Italy
Tel. ++39 045 6159411- Fax ++39 045 6159422 - e-mail: [email protected] – www.at-os.com
52
PART 3
7
SCHEDULED MAINTENANCE PROCEDURES
The display shows the message requesting performance of routine maintenance every 2000 wash cycles
performed by the machine (if this value is preset). Maintenance procedures to perform are established based
on the number of cycles performed (see table below).
If the machine is used fewer than 15 times a day (average value) then periodic inspection can be performed
according to the time periods (rather than the work cycles) indicated in the table (at least once a year).
The following table lists the procedures necessary for performing adequate scheduled routine maintenance in
function of the number of cycles and/or work intervals performed by the machine:
INTERVALS
No. CYCLES
PREVENTIVE MAINTENANCE PROCEDURES
-
500*
T
A
K
B
R
6 months
2000
T
A
K
B
R
1 year
4000
N
T
G
C
D
1 year and 6 months
6000
T
E
U
F
V
W
2 years
8000
H
I
N
J
2 years and 6 months
10000
C
L
T
U
G
K
M
L
U
S
5 years
20000
O
P
Q
(*: procedures necessary only if machine operation during testing was not OK).
NOTE: maintenance procedures are performed either based on the number of wash cycles or based on operating time.
Proper routine maintenance must be performed on the machine to ensure correct
operation.
If the machine does not work even after maintenance then turn to the AT-OS S.r.l.
Service Department specifying the type of defect and the machine model and serial
number.
A.
Check the rotary jets: impurities (cleaning) and rotation
See the instructions in paragraphs 6.7.1, 6.7.2 and 6.7.3.
B.
Check for basin seal leaks
Check if there are no holes in the basin seal. Otherwise proceed with the instructions given in
paragraphs 6.12 and 6.13.
C.
Check power connections on the electric board
Check if all connectors are properly inserted
D.
Check the cleanliness of the hot and cold water refill solenoid valves
See the instructions in paragraph 6.2.1
E.
Check if drain trap welds do not leak
Perform a wash cycle with the reduced program. Then cut off electrical power to the machine using the
main switch upstream from the appliance and also the service switch. Access the lower compartment
and check if there are no droplets along the trap tubing. If the trap leaks water through its joints then
replace it with a new one.
F.
Cleaning the solenoid valve that fills the steam generator
See the instructions in paragraph 6.2.2.
Содержание AF2 C Series
Страница 67: ......