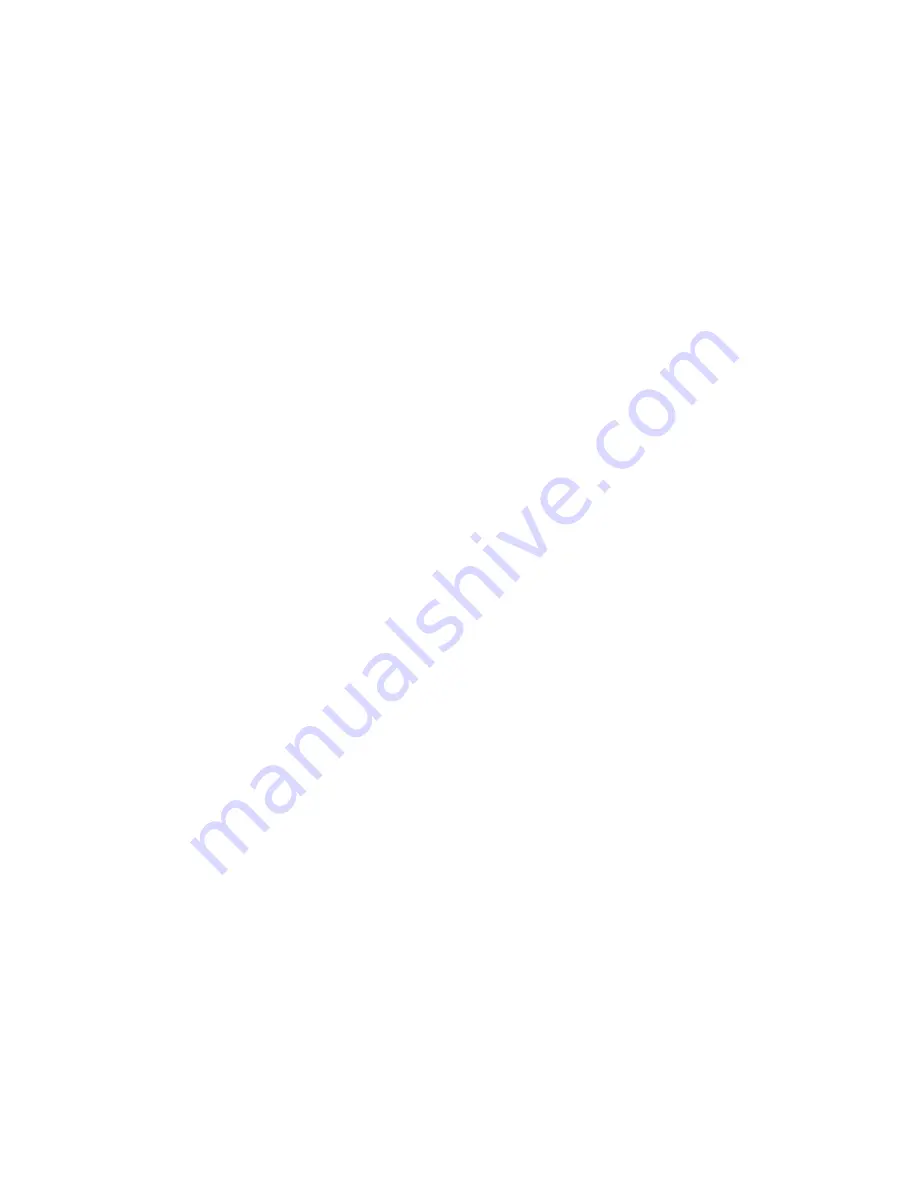
Vertical stabilizer:
This a simple part. Construct the frame with ¼ x 3/8 and install the ¼ square cross piece.
Sheet this part with 3/32” balsa and you are done.
Rudder:
Begin by stripping 6 pieces of 1/16” x 3/8” x 36” balsa to form the laminated outline.
These strips should be soaked in a tub of water for about two hours. During this time you
can begin pinning the inner outline of the rudder. The pins should be placed every ¼” on
the straights with 1/8” spacing on the tight radiuses. Once you have removed the strips
from the water, coat them with carpenter’s glue to create a 3/8” thick 6 layer deep
laminate. Again, begin at one end and begin working the laminate around the outline.
When you come to the tight radii, maintain a tight pressure in holding the laminate
together, this will minimize the breakage within the individual pieces (Some fractures are
acceptable and unavoidable). Once the outline is completed, again let it dry for a
minimum of 24 hours. The completion of the rudder is now a straight foreword affair.
Fuselage:
Begin the fuselage by constructing the forward box from parts FP1, FP2, the two ¼”
sides, and temporary formers Fxx. Take care to ensure that the temp formers Fxx are
located on the center line as indicated on the plans. Install the balsa formers to their
appropriate plywood formers. The balsa formers are ¼ semi-circles with two upper and
lower parts per hoop. The formers are all designed to slide snuggly onto a piece of ¾”
I.D. copper tubing. Mark the former locations onto the piece of tubing and slide the
formers into their correct locations. Install the eight ¼” square stringers in their slots
alternating from side to side, all the while checking to maintain a 90 degree angle
between the former and the jig tube. Trim them to an angled joint at the tail as shown on
the plans. Reinforce the area where the horizontal stabilizer spar will pass through using
¼” balsa and then trim the hole for the spar through the stringer. Next sheet the wing
saddle using 1/8” sheet balsa. The saddle will use FP2 to maintain its correct angle. Now
complete boxing in the saddle by using scrap 1/8” balsa to tie the saddle into FP9 and
FP10. Repeat this procedure on both sides. Our next step is to cap the 3/8” x ¾”x 12”,
3/16” grooved blocks with 1/8” plywood. Once this is done lay the blocks in their correct
locations against FP1 and FP2. Mark the angle of the formers on the blocks and trim
them. Epoxy them in place reinforcing them on the outside of the box with ½” triangle
stock. Retain the trimmed ends, as we will now use them for the front landing gear leg
mounts. Mark the location of the front landing gear mount onto the outside of the box and
a 90-degree line on former FP1. Hold the blocks in place and draw a line using FP1 as a
template. Now epoxy both blocks to the box and FP1 using 30-minute epoxy. Once this
has set, epoxy in the two per side ¼” plywood reinforcements FPxx as shown on the
plans. Now we are ready to start sheeting the fuselage. The first step is to sheet the sides
and top from the front of the cockpit to the tail, leaving the bottom open for now. If you
are building this plane for contest work, you will want to panel it according to your three
views or pictures, otherwise panel it as is convenient. A little water and ammonia sprayed
through a Windex bottle really helps curl the sheeting to fit the formers. If you will be
staining the wood, take great care to minimize the glue, which gets onto the outside
surface of the wood as it can create light spots. At this time you may remove the fuselage
from its jig tube. Finally it’s beginning to look like something. While the fuselage is in
this state, reopen the tail