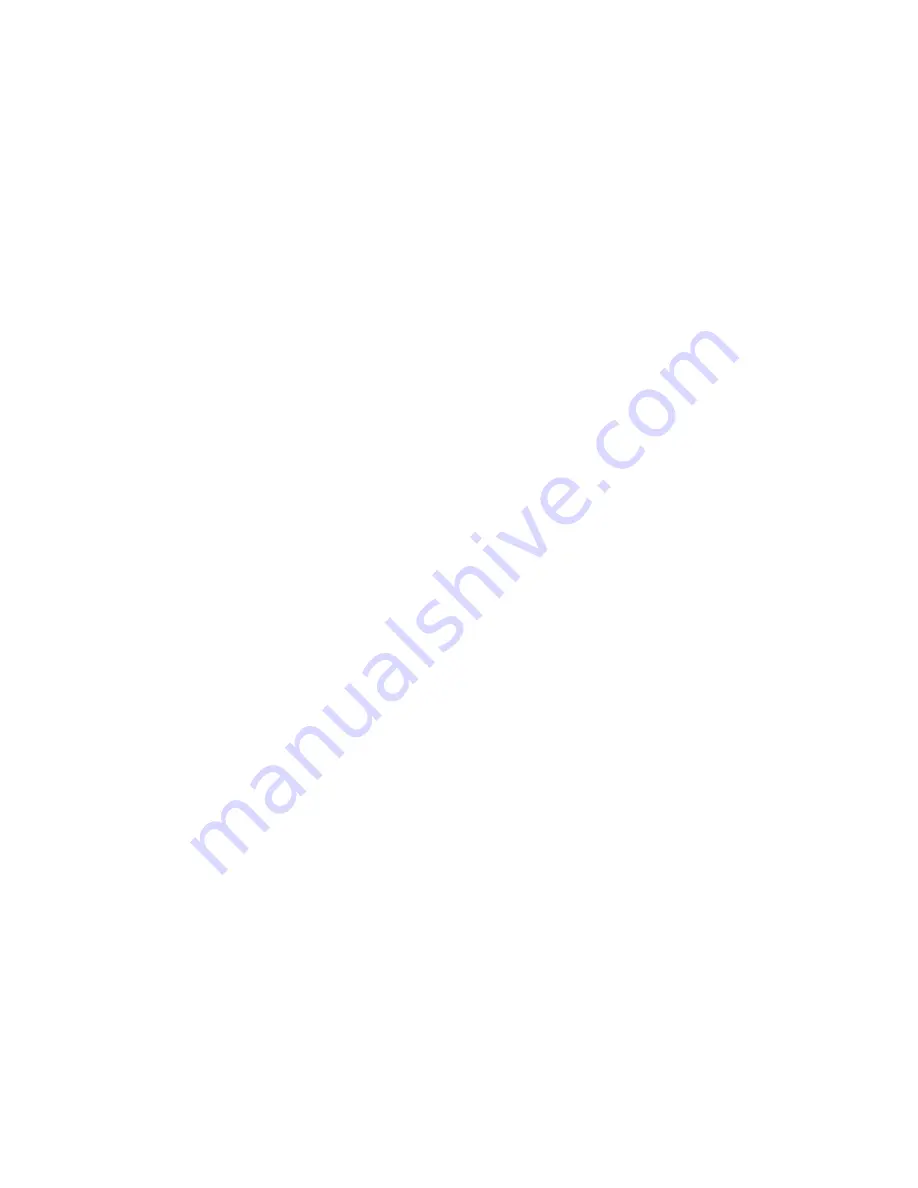
F
OR
M
ODELS
: JGI, JGM, JGN, JGP
AND
JGQ
S
ECTION
5 - M
AINTENANCE
PAGE 5-13
Crosshead - Installation
NOTE: BE SURE CROSSHEADS ARE RETURNED TO THEIR ORIGINAL THROW
LOCATION.
1.
With the throw positioned near to its inner dead center position, turn the cross-
head on its side and slip it into the crosshead guide. Rotate the crosshead 90°
into place. Make sure it does not become cocked. Should the crosshead
become wedged, do not force it. Ease it off and start again. Be careful not to
damage the crosshead shoe surface during installation.
2.
Lift the crosshead end of the connecting rod and turn the crankshaft to near the
outer dead center position to locate the connecting rod in the crosshead. Align
connecting rod bushing with the crosshead bushings and insert the crosshead
pin.
3.
Install the end plates, through bolt and locknut. Tighten the locknut to the torque
value listed in Table 1-12 on page 1-16.
4.
Be sure that the crosshead-balance nut seating surfaces are flat and free of
burrs. Dress with a flat stone as required. The piston rod threads are to be lubri-
cated with a thin coat of Never Seez, regular grade, and the crosshead-balance
nut seating surfaces with new oil (same grade as used in the frame).
5.
Re-install the crosshead-balance nut on the piston rod. Be sure to have set-
screw cup points on the crosshead side of the nut. Install the piston and rod
assembly in the cylinder. See “Piston and Rod - Installation” on page 5-30.
NOTE: PISTON END CLEARANCE MUST NOW BE SET OR SERIOUS DAMAGE
COULD OCCUR. SEE THE REQUIRED PISTON CRANK END CLEARANCE AS
SHOWN ON THE CYLINDER IDENTIFICATION PLATE, REFER TO TABLE 1-3
ON PAGE 1-10.
6.
Position the crankshaft to the exact inner dead center position of the throw.
NOTE: UTILIZE A DIAL INDICATOR WITH A MAGNETIC BASE TO INDICATE THE
LOCATION OF THE CROSSHEAD WHEN FINDING EXACT INNER DEAD CEN-
TER POSITION.
7.
Determine the required piston crank end clearance from the cylinder identifica-
tion plate, refer to Table 1-3 on page 1-10. Insert a feeler gage, equal to the
required crank end clearance, through an open valve pocket. For 13 in. (330
mm) and larger cylinders, insert the feeler gage through a bottom valve pocket.
For 2-3/4M, 3M, 2-3/4P-CE and 3-1/4P-CE class cylinders, use the Ariel fur-
nished clearance setting tool A-13801 as a feeler gage, see Figure 7-1 on page
7-2 (this tool must be inserted horizontally with end notch side toward the crank
end and rotated 90° to position the end notch up, prior to performing step 6.
above). 2-1/4P-CE class cylinders use clearance setting tool A-11344. Screw
the piston rod into the crosshead until piston is tight against the feeler gage, so
that the feeler gage can not be removed by hand.
8.
Use the Ariel furnished special slugging peg or open end wrench shown in Fig-
ure 7-1 on page 7-2 and a dead blow semi-soft faced hammer to tighten the
crosshead-balance nut by the tried and true slugging method. Strike the wrench
with the hammer until an audible difference can be heard, and/or on seeing the
wrench “bounce” indicating that the nut is tight. Some mechanics can obtain the
desired tightness in 3 to 4 strikes, while others may require more hammer blows.
9.
When the nut is tight, the feeler gage can be removed by hand.