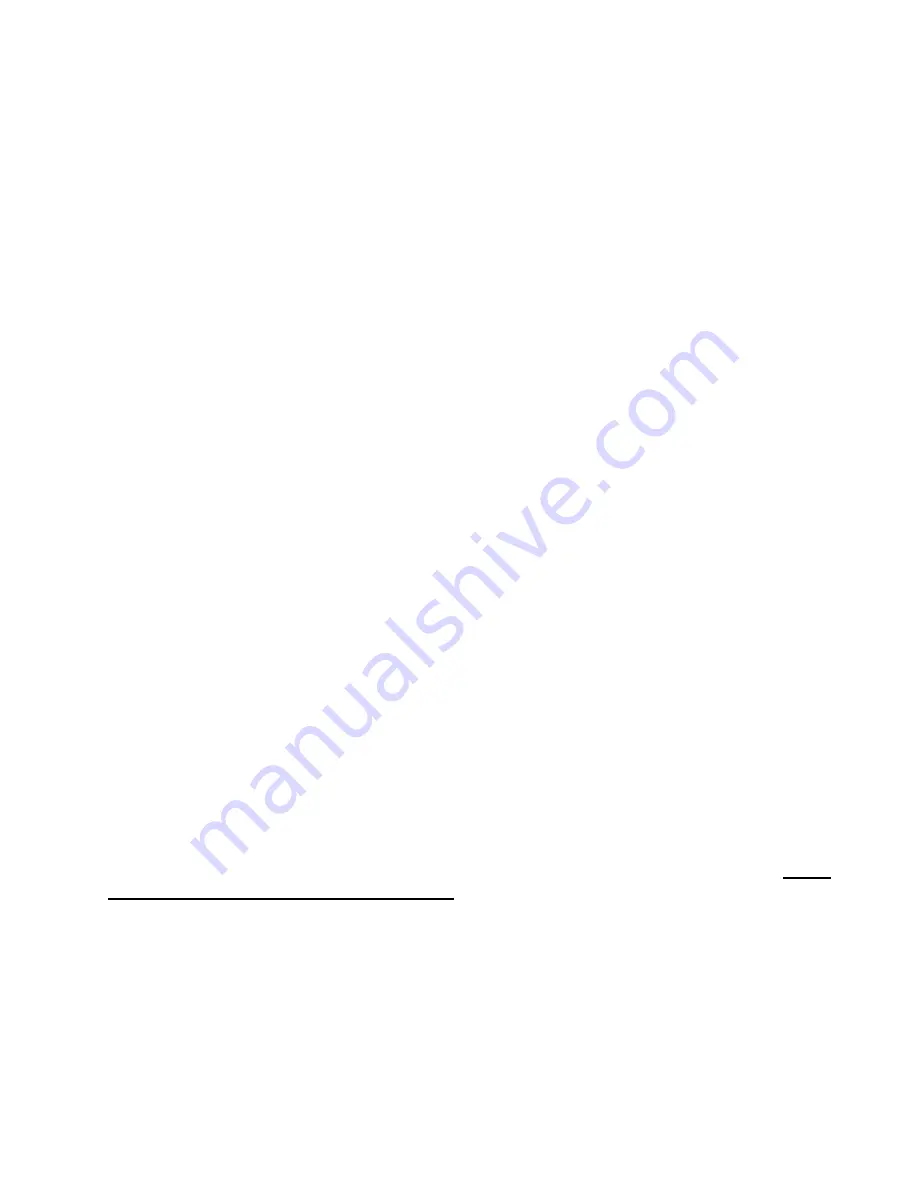
F
OR
M
ODELS
: JGI, JGM, JGN, JGP
AND
JGQ
S
ECTION
4 L
UBRICATION
PAGE 4-53
USE ANY OTHER FLUIDS FOR PURGING!
Start up the compressor and bring up to normal operating pressure. After the operating pres-
sures have stabilized, adjust the cap on the top of the balance valve if necessary. Loosen
the locking nut on the top of the balance valve directly under the cap. Turn the cap clockwise
to increase the pressure and counter clockwise to decrease the pressure. Retighten the
locking nut against the cap.
Set the balance valves and maintain at approximately same pressure on each pressure
gauge in the injection lines of the pump system affected. A system should be set and main-
tained within 500 psi (3400 kPa) total or less. The closer the individual line pressures are
maintained, the more reliable the system will become.
Once the balance valves have been set, they should be checked 4 to 6 hours later to ensure
the pressures have not changed and caused another imbalance. If readjustment is neces-
sary the gauges should be checked again in 4 to 6 hours. If a pressure gauge in a line with a
balance valve is reading more than 500 psi (3400 kPa) higher than the others, try to reduce
the pressure on that particular injection line. If reducing the balancing pressure on the bal-
ance valve does not drop the pressure, then the other balance valves will need to be
adjusted to match the highest pressure.
To set balance valves equipped with a distribution block inlet gauge only:
1.
Start up the compressor and bring up to normal operating pressure. After the
operating pressures have stabilized, with all balance valves backed off (zero
spring load), note the highest gauge pressure reached in a complete block
cycle.
2.
Slowly increase the spring load on one balance valve, being careful to not
exceed rupture disk rated pressure. Watch the gauge and if the maximum pres-
sure increases, reduce the spring load until the highest pressure falls to the
pressure noted in step 1, above. Tighten the lock nut against the cap, hand
wrench tight.
3.
Repeat step 2, for the remaining valve(s).
Maintain the system by recording the pressures and cycle times of the lubrication system at
least once a day.
Checking/Adjusting Balance Valves on Subsequent Start-up
Be sure that all fittings are tight and any known leaks have been fixed. Purge the force feed
system with a purge gun (hand pump kit, available from Ariel purchased separately), using
the same injection oil that is used in service.
Start the compressor and bring up to normal operating pressure. After the operating pres-
sures have stabilized, check the pressure gauges to ensure the system is still balanced. If
one or more line pressures are out of balance, wait for 2 to 3 hours to see if they become
balanced. DO NOT adjust the balancing valves immediately. It is possible that some lube
points will increase in injection pressure after a short period of run time and the system will
become balanced if it is not balanced on start up.
If a balance valve(s) was installed, but is not required, leave (or set) the spring adjustment at
zero. If back-pressure on an unused balance valve is high enough, it may eventually begin