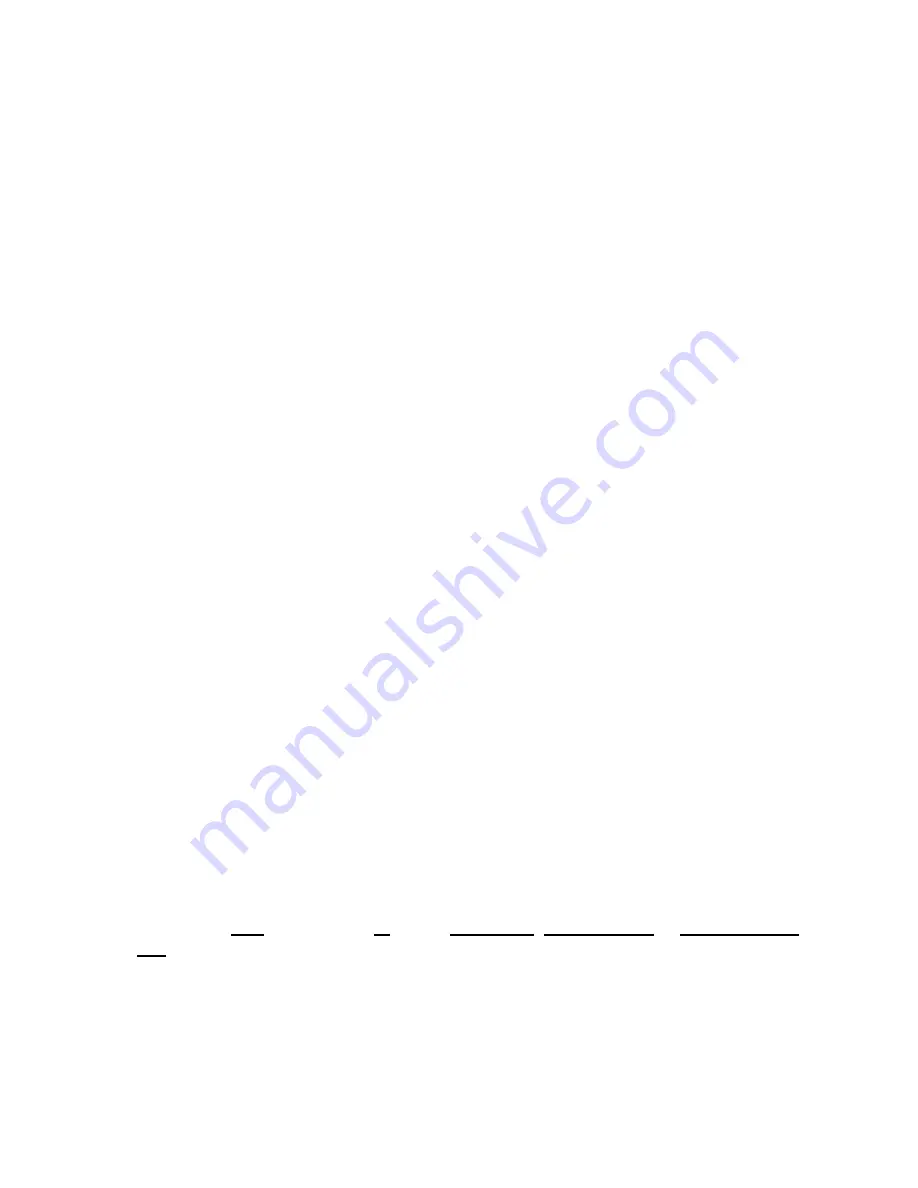
F
OR
M
ODELS
: JGI, JGM, JGN, JGP
AND
JGQ
PAGE 6-1
S
ECTION
6 - T
ECHNICAL
A
SSISTANCE
Recommended Maintenance Intervals
Like all equipment, Ariel compressors do require maintenance. The frequency of mainte-
nance is dictated by the environment in which the compressor is placed, the loads the user
imposes on the compressor and the cleanliness of the gas.
First and foremost on the preventative maintenance list is the completion and compliance
with the Ariel Corporation Packagers Standard and Compressor Start Up Check List. All
items must be adhered to, both before and after start up.
The following is a guide only and, as stated above, may vary due to operating conditions.
The time intervals start from the start up date of the unit. If your oil supplier's recommended
oil service changes are more frequent than the Ariel recommendations, the supplier’s inter-
vals should be followed. Regular oil analysis is recommended. If problems develop the oil
should be changed immediately and the cause of the problem determined and corrected.
A log book should be kept with each unit. Every maintenance item can be entered with
exacting detail in order that records will be available for tracking maintenance costs per unit
and for trouble-shooting.
Operator logs should be reviewed by qualified personnel to determine trends in compressor
performance and/or maintenance.
CAUTION! BE SURE THAT THE COMPRESSOR IS COMPLETELY VENTED TO
RELIEVE ALL GAS PRESSURE, AND THE DRIVER WILL NOT EXERT
TORQUE ON THE COMPRESSOR CRANKSHAFT THAT COULD RESULT IN
INJURY, PRIOR TO TAKING COUPLING READINGS, RE-CHECKING
BOLTING TORQUES ON PRESSURE CONTAINING COMPONENTS OR
REMOVING ACCESS COVERS FOR PERFORMING INTERNAL
INSPECTION OR MAINTENANCE ON THE COMPRESSOR. IN THE CASE
OF A DIRECT DRIVE MOTOR, THE BREAKER IS LOCKED OUT. FAILURE
TO FOLLOW THESE STEPS CAN RESULT IN SERIOUS PERSONAL
INJURY OR DEATH.
Daily
After running a new compressor (or after a re-location, re-configuring or major overhaul) for
the first 24 hours, shutdown, vent gas system and perform a hot alignment check at coupling
within 30 minutes, while barring driver shaft to packager’s recommendations. Realign if nec-
essary to hold coupling hub face and rim hot alignment within 0.005 inch (0.13 mm) TIR,
except for hub O.D. >17 in. (>43 cm) angular hub-face limit is increased to 0°1’ (0.0167°).
Also check fastener torque on gas nozzle flange, valve cap, cylinder head, compressor rod