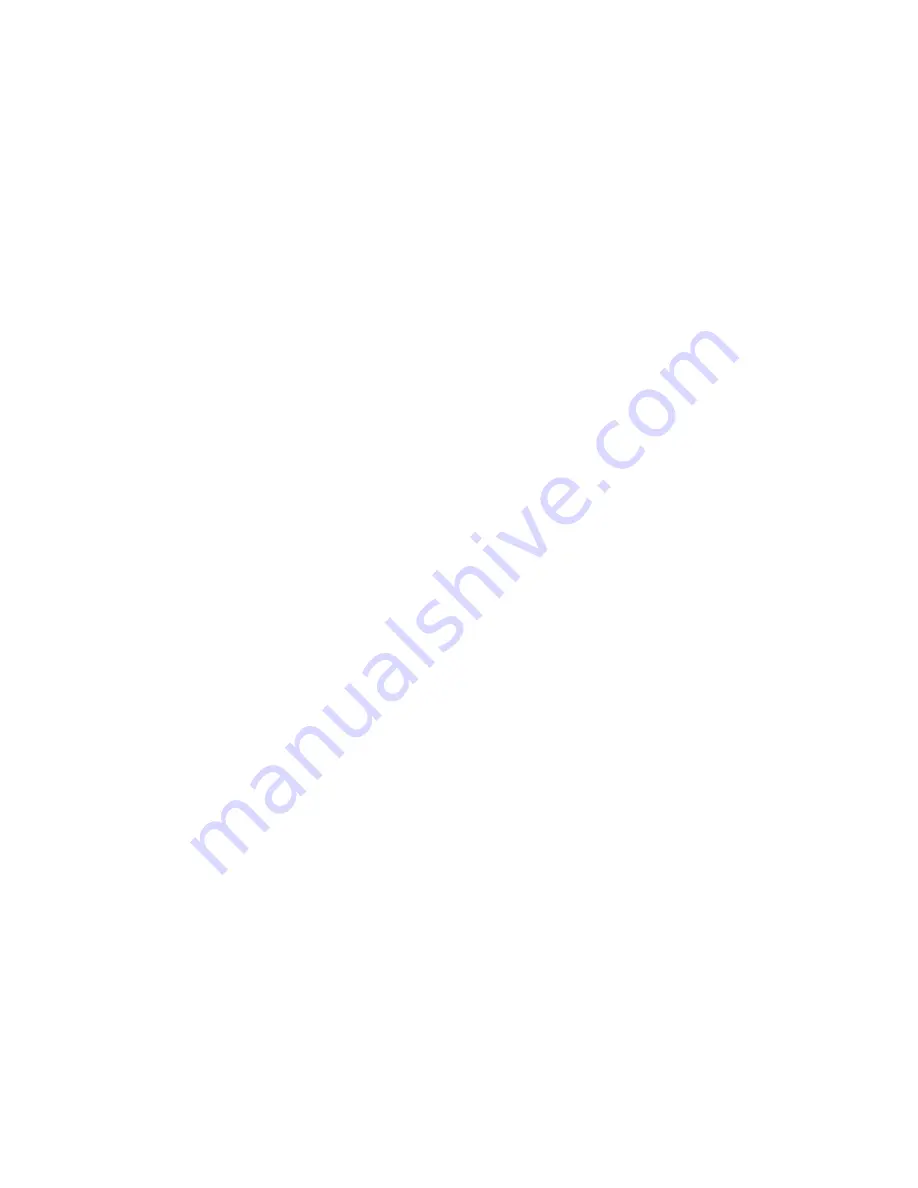
F
OR
M
ODELS
: JGI, JGM, JGN, JGP
AND
JGQ
S
ECTION
2 - I
NSTALLATION
PAGE 2-6
4.
Loosen the bolting while checking with a dial indicator to be sure that the clear-
ance is completely filled and there is no deflection.
5.
Using the information from the current
Ariel Performance Program
, determine
the estimated crosshead guide foot deflection for JGH:E:K:T:C:D:Z:U:KBB:V
frames. This calculated value is required to compensate for the deflection or
droop of the cantilevered weight of the guide and cylinder. For the
JG:A:M:N:P:Q:R:W:J frames, the guide and cylinder weights are not sufficient to
deflect the guide.
6.
Lift or jack cylinder, just slightly to allow insertion of additional shims based on
the calculated value.
7.
Re-tighten the crosshead guide hold down bolting to full fastener torque.
8.
Repeat for each crosshead guide support.
9.
Shims may need to be adjusted so that the crosshead to guide top and bottom
clearances, and piston rod run-out measurements are within the tolerance
requirements. Reference Section 5 for checking crosshead clearances and pis-
ton rod run-out, and Section 1 for tolerance limits.
10. For some applications, head-end cylinder supports may be desirable for larger
classes of cylinders (bosses and tapped holes are provided on all
K:T:C:D:Z:U:B:V class cylinders). See Ariel cylinder outline drawings for dimen-
sional details. These supports must be adjusted and set when the components
are at operating temperature.
Setting - Miscellaneous
1.
Reference Technical Manual Section 4 for protection of electronic equipment
when arc welding.
2.
Comply with the Ariel Start Up Check List, see Technical Manual Section 3.
Alignment - to Driver
Proper alignment to the driver is necessary for satisfactory performance. A flexible coupling
will not make up for poor alignment. Misalignment can result in:
•
High bending moment on the crankshaft.
•
Large axial forces.
•
Excessive bearing wear.
•
And if severe, probable damage to various components.
Procedural Requirements for Aligning a unit:
•
Check the compressor frame, crosshead guide and driver hold-down bolting fastener
torques.
•
Check and correct the alignment of the compressor main bearing bores by the top-
cover mounting surface flatness and/or soft foot, as applicable. The compressor and
driver are to be laying flat. Check the driver’s technical information for detailed
instructions and determine that driver is laying flat.
•
Correct the cold alignment readings with the predicted thermal growth values for both
the compressor and the driver.
•
Pre-lube the compressor frame using the compressor pre-lube pump prior to turning