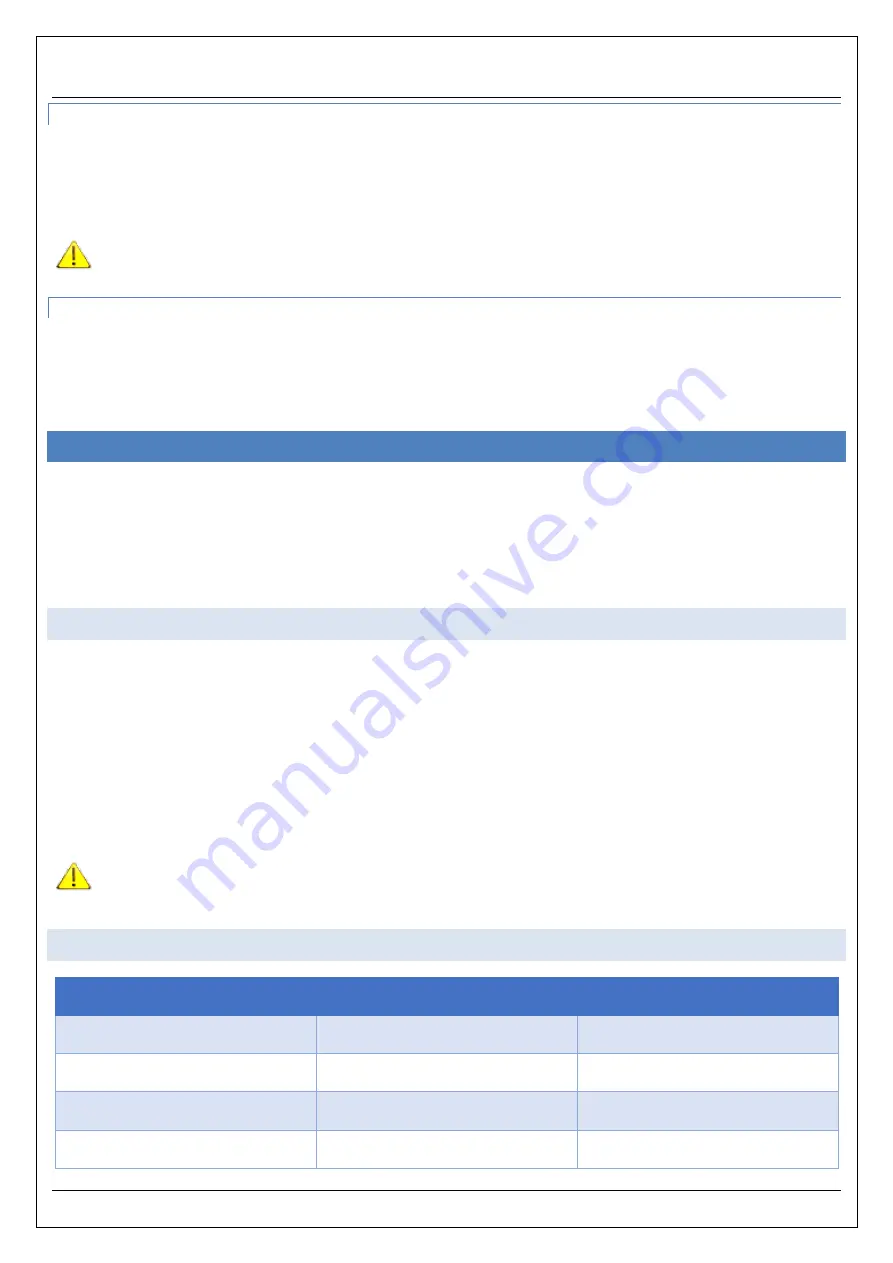
Operating manual
AQUA S.p.A.
ENGLISH
Page 18
PULSATI ON DAMPENER
The installation of a pulsation dampener improve the pump performance and also guarantees:
•
Protection against high pressure surges (fluid hammer), improving the machine long time duration;
•
Continuous flow rate with a regular flux;
•
Reduction of vibrations transmitted to discharge piping;
•
Pump noise reduction.
NOTE: If the process needs a continuous flow rate, it is mandatory to install the pulsation dampener.
MANOMETER
It allows to check the actual working pressure of the pump. It has to be installed on the discharge pipe, near the pump and before any eventual
pressure drops which could offset the right value. Periodical check of the value shown by the manometer allows to recognize further obstruction
events and prevent damages to the pumps and the plant itself. Installed manometer must be of the right scale, according to the pump in the plant
(e.g. for 8 bar working pressure pump, a 0-15 bar scale manometer is suggested), in order to have an easily readable value.
START
PRELIMINARY CHECKS
•
Be sure there are no product leakages from the pump connections or from the plant pipings;
•
Check the proper installation of all the accessories and their correct operation;
•
Check correct interception valves functionality (close/open according to their position);
•
Check there is no solidified/crystallized or frozen parts into dosed product and pipes
•
Be sure that the pump is adequately protected against external agents like sand, dust, corrosive substances, water, vibrations, tensions,
humidity or extreme thermic excursions
STARTING SEQUENCE
1.
Load the oil into the gearbox using the 250 cc container supplied with the machine, through the loading cap, like shown in the picture.
However the right level matches about with the middle of the oil level plug.
2.
Set the adjustment at 0% and start the motor, check the counter clockwise sense of its rotation as indicated by the arrow.
3.
Gradually increase the adjustment to 50% by keeping the discharge pressure at minimum, Keep this condition for at least 5 mins, and
then increase to reach the 100%.
4.
Adjust the counter pressure valve to the requested working pressure.
5.
Set the adjustment to process request, eventually compensate the pressure drop caused by the adjustment set at a value lower than
100%.
6.
During this first step, verify the actual pump working pressure by using a manometer. Maximum value cannot exceed the pressure
indicated on the pump sticker.
7.
Once the pressure has been set, verify that the current absorption coefficient complies to plate limits.
ATTENTION! Pump generate the maximum pressure with adjustment set to 100%. Absorption coefficient check must be executed
at maximum working pressure.
MAINTENANCE PROGRAM
AQUA suggests a maintenance program frequency according to the following table:
INTERVENTION
FREQUENCY
HOURS OF SERVICES
Periodical visual check
weekly
60
Liquid end parts washing
Before than any disassembling and in case of
crystallizing fluids at any machine stop.
variable
Valves group replacement
24 months
8000
Diaphragm replacement
24 months
8000