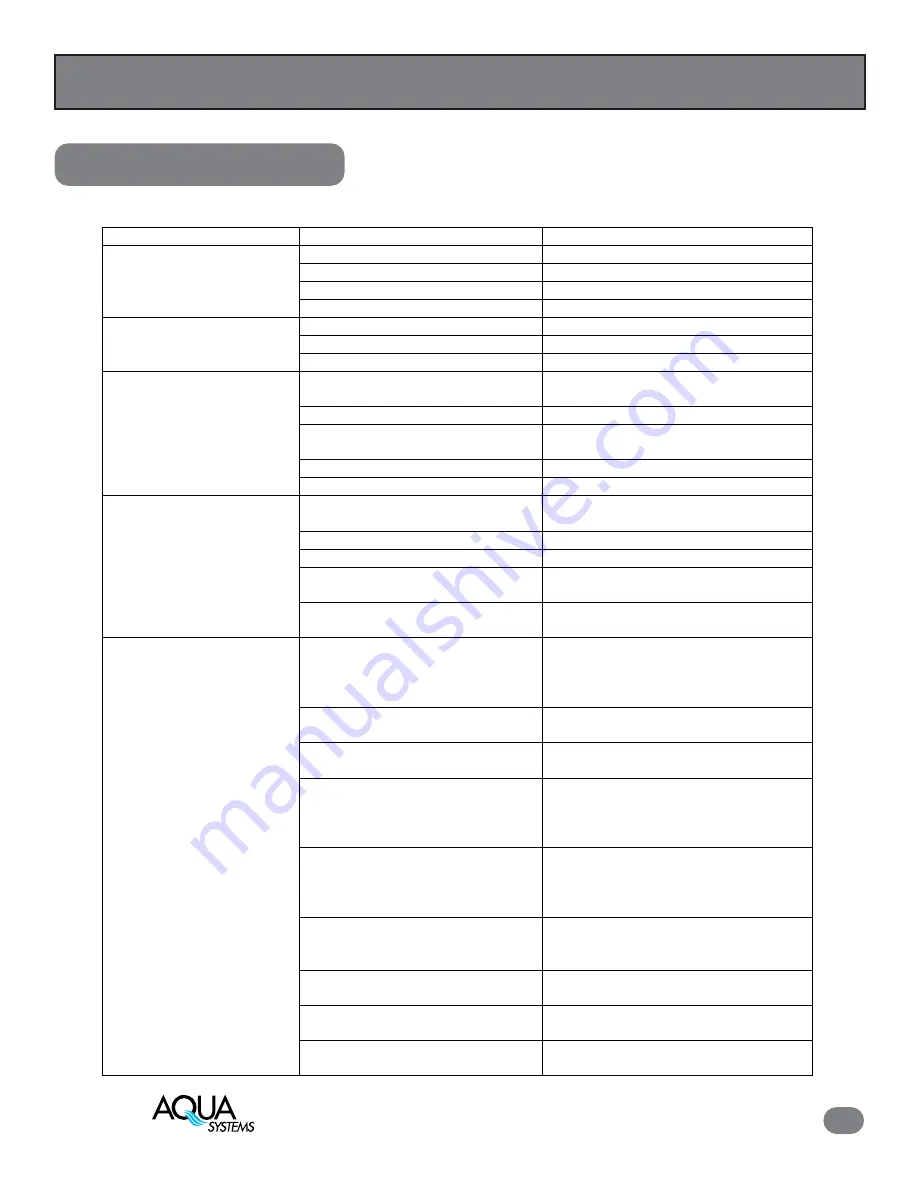
© 2002 New Aqua LLC dba Aqua Systems • 7785 East US Hwy 36 • Avon, IN 46123
37
Series SC
Installation, Operation,and
Maintenance Manual
Troubleshooting
Problem
Possible Cause
Solution
a. Transformer unplugged
a. Connect power
b. No electric power at outlet
b. Repair outlet or use working outlet
c. Defective transformer
c. Replace transformer
1. Timer does not display
time of day
d. Defective PC board
d. Replace PC board
a. Switched outlet
a. Use uninterrupted outlet
b. Power outage
b. Reset time of day
2. Timer does not display
correct time of day
c. Defective PC board
c. Replace PC board
a. Bypass valve in bypass
position
a. Put bypass valve in service
position
b. Meter connection disconnected
b. Connect meter to PC board
c. Restricted/stalled meter turbine
c. Remove meter and check for
rotation or foreign material
d. Defective meter
d. Replace meter
3. No softening/filtering
display when water is
flowing
e. Defective PC board
e. Replace PC board
a. Power outages
a. Reset control valve to correct time
of day
b. Time of day not set correctly
b. Reset to correct time of day
c. Time of regeneration incorrect
c. Reset regeneration time
d. Control valve set at “on 0”
(immediate regeneration)
d. Check control valve set-up
procedure regeneration time option
4. Control valve
regenerates at wrong
time of day
e. Control valve set at NORMAL
+ on 0
e. Check control valve set-up
procedure regeneration time option
a. Control valve has just been
serviced
a. Press NEXT and REGEN for 3
seconds or unplug power source
jack (black wire) and plug back in
to reset control valve
b. Foreign matter is lodged in
control valve
b. Check piston and spacer stack
assembly for foreign matter
c. High drive forces on piston
c. Replace piston(s) and spacer stack
assembly
d. Control valve piston not in
home position
d. Press NEXT and REGEN for 3
seconds or unplug power source
jack (black wire) and plug back in
to reset control valve
e. Motor not inserted fully to
engage pinion, motor wires
broken or disconnected, motor
failure
e. Check motor and wiring. Replace
motor if necessary
f. Drive gear label dirty or
damaged, missing or broken
gear
f. Replace or clean drive gear
g. Drive bracket incorrectly
aligned to back plate
g. Reseat drive bracket properly
h. PC board is damaged or
defective
h. Replace PC board
5. ERROR followed by
code number
Error Code 1001 -Unable
to recognize start of
regeneration
Error Code 1002 –
Unexpected stall
Error Code 1003 – Motor
ran to long, timed out
trying to reach next cycle
position
Error Code 1004 - Motor
ran to long, timed out
trying to reach home
position
If other Error Codes
display contact the factory.
i. PC board incorrectly aligned to
drive bracket
i. Ensure PC board is correctly
snapped on to drive bracket