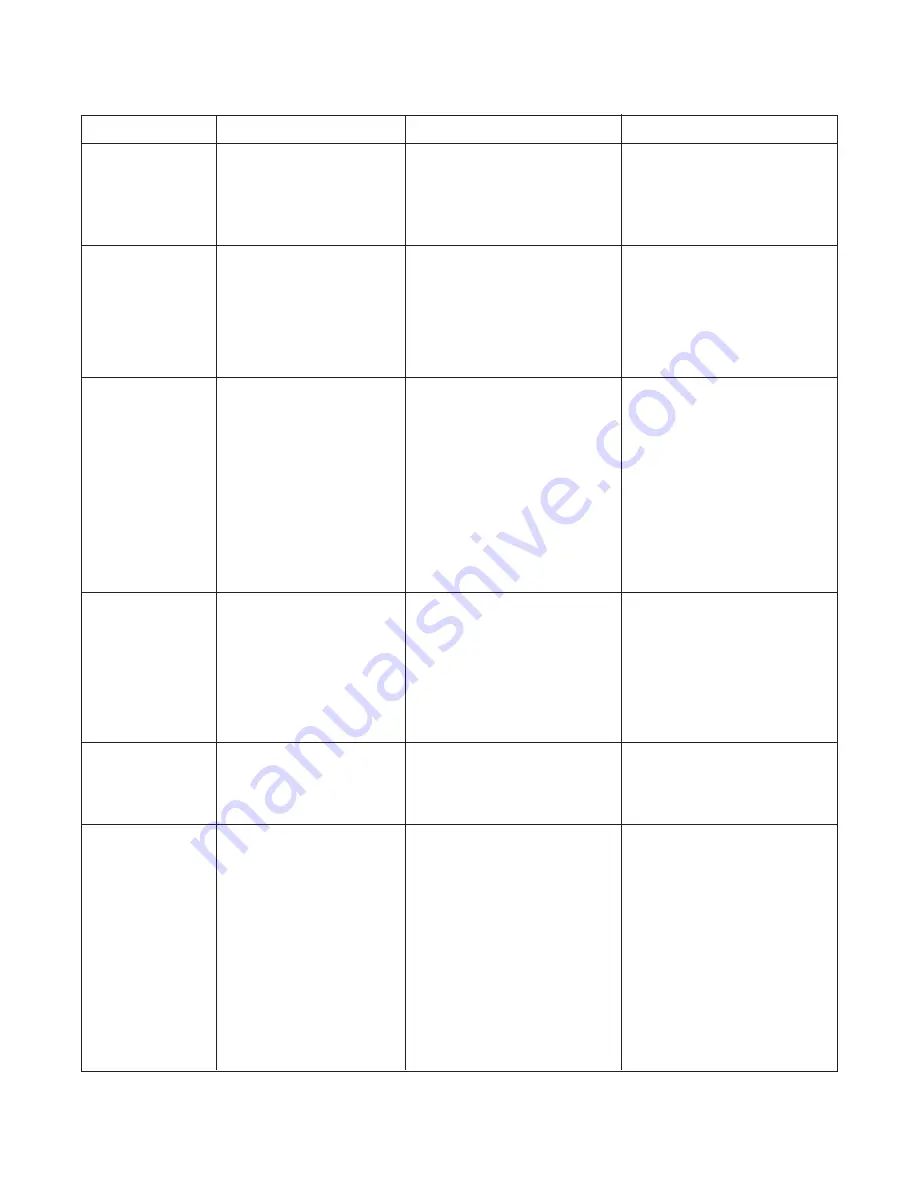
– 29 –
1. Clean, replace valve and/or
seat if necessary.
2. Clean, or if necessary,
replace plunger.
1. If readings are incorrect,
replace Outside Air
Temperature Sensor (TS-01)
or Discharge Air Temperature
Sensor (TS-03) or repair
wiring.
1. Increase inlet pressure
if possible or change to
larger valve. Consult factory
about possibility of using
special spring to reduce
pressure drop on selected
installations.
2. See Valve Adjustments
-Section X.
1. If readings are incorrect,
replace Discharge Air
Temperature Sensor
(TS-03) or repair wiring.
2. If desired temperature is
not reached, increase
Maximum Heating Discharge
Temperature Setpoint.
1. If proper resistances are not
observed, replace modulator
head or repair wiring.
1. If desired Space Temperature
is not reached, increase
Minimum Heating Discharge
Setpoint.
2a. Change to correct setpoint.
2b. Change to correct setpoint.
3. If desired Space Temper-
ature is not reached with
heater at high fi re, it may be
undersized. Consult Factory.
TROUBLESHOOTING GUIDE
TROUBLESHOOTING GUIDE
Modulating Room Temperature (MRT, MRT-PRO or MRT-EXPERT) Controls
continued
Portions reproduced with permission from Maxitrol
®
Company
Symptom
Possible Cause
Field Test
Remedy
1. Foreign material
holding valve open.
2. Plunger jammed.
1. Open circuit in Outside
Air Temperature Sensor
(TS-01) or Discharge
Air Temperature Sensor
(TS-03)
1. Inlet pressure too low.
2. Incorrect outlet
pressure adjustment.
1. Open circuit in
Discharge Air
Temperature Sensor
(TS-03).
2. Incorrect Maximum
Heating Discharge
Temperature Setpoint.
1. Short in modulator
coil circuit.
1. Incorrect Minimum
Heating Discharge
Temperature Setpoint.
2. Incorrect space setpoint.
3. Insuffi cient burner
capacity.
G. Continuous High
Fire (Electronics
Problem).
H. Continuous High
Fire (Electronics
OK).
I. Incorrect
High
Fire.
J. Continuous
Maximum
Discharge Air
Temperature.
K. Burned out
Transformer.
No Voltage to
Amplifi er.
L. Incorrect Space
Temperature.
Control circuits external to MRT Controls can cause burner malfunction.
Always check manual valve to be certain gas is on, and check limit controls for normal operation.
1. Remove bottom plate and
inspect valve and seat.
2. Inspect - plunger should be
smooth and clean and operate
freely in solenoid sleeve.
1. Measure resistance per
Thermistor Curve.
1. Read inlet pressure at
valve, using a manometer
with heater operating at full
fi re. Pressure should be at
least equal to the sum of:
outlet pressure setting and
pressure drop of the valve
plus 1.0" w.c.
2. Read outlet pressure using
manometer and compare
with the pressure stated on
the specifi cation plate.
1. Measure resistance per
Thermistor Curve.
2. Check to see if heater is
delivering at Maximum
Heating Temperature
Discharge Setpoint.
1. Measure resistance per
item B1.
1. Check to see if heater
is delivering at Minimum
Discharge Setpoint.
2a. Check Unit Enable
Potentiometer (MP-15)
Setpoint.
2b. Check Heating Occupied
and/or Unoccupied setpoint.
3. Check to see if heater is
operating at high fi re.
(Refer to Digital Control System User Manual for additional troubleshooting suggestions)
Содержание IOMDFCDFM-1
Страница 43: ... 43 ...
Страница 44: ...4830 Transport Drive Dallas TX 75247 Phone 214 638 6010 Fax 214 905 0806 www appliedair com ...