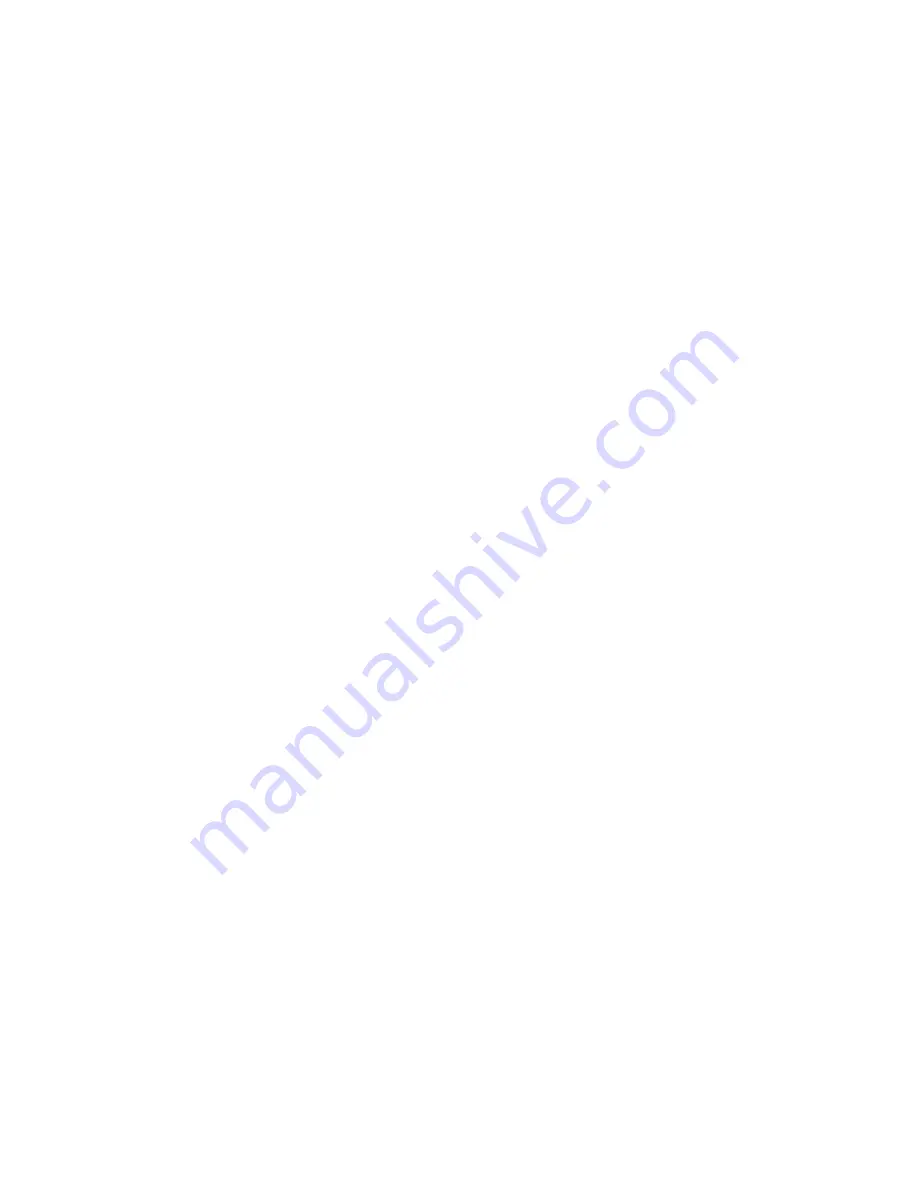
– 37 –
24. Place a drop of “BLUE” Loctite on the blower
setscrews and tighten all of the setscrews.
25. Align the blower and motor sheaves using a laser
or straight edge and tighten the blower sheave to
the shaft.
26. Replace the belts and tighten the motor base
adjustment for the proper belt tension. Over
tightening the belt tension will severely reduce
belt and bearing life. Belt defl ection should be
approximately 1/64 inch for every inch of span
length.
27. Monitor for excessive heat or vibration during
operation.
28. All bearings are pre-lubricated and should not
initially require greasing. See previous section for
bearing maintenance instructions.
Note: Drive side Sleevlock bearing installation
(USRB5000A 115C)
WARNING: Do not apply grease, oil, or anti-seize
compound to the tapered surface, bore, or
shafting. If any of these substances are applied,
equipment failure and personal injury may
result.
1. Mount all the bearings and leave all of the bolts
and setscrews loose.
2. Tighten setscrews on the bearing to the
tightening pattern as described in the
installation sheet that comes with the bearing
to a fi nal 30 inch lbs torque while rotating the
shaft. Check to make sure the insert of the
bearing is centered in the bearing housing and
then bolt bearing down.
3. Tighten down the bolts and setscrews on
the remaining bearings per installation sheet
starting from the non-drive end bearing back
towards the Sleevlock while rotating the shaft.
3. Dampers – Dampers should be inspected monthly
(daily in icy or snowy weather)
for securely fastened
linkages, and smooth operation. If dampers are binding
or excessively noisy, then lubrication may be required.
Place one drop of #20 wt. machine oil on each blade
bearing, and linkage ball joint. Do not over lubricate,
and wipe any excess from the area. Be sure to note
that dampers over 49 inches long have intermediate
bearings which require lubrication. On outdoor models
with factory supplied discharge dampers, you will need
to remove to top cover to access the damper bushings.
Replace cover and caulk as necessary.
C. Air Filters
All fi lter banks should be equipped with a manometer
or differential pressure switch to indicate when the
fi lters are dirty. Filters should be replaced when
the differential pressure across them reaches the
manufacturer’s recommended fi nal value. Dirty fi lter
elements should be replaced with a clean element of
the same type and size. In addition, the factory not
only suggests, but insists, that air fi lters be
checked
every 30 days (daily in icy or snowy weather)
and
replaced with new fi lters (throw-away type) or cleaned
(washable type) as required. Cleanable fi lters should
be given new application of fi lter coating after washing
to maintain optimum fi lter performance.
The frequency of cleaning and replacing air fi lters
applies twelve months of the year,
where blowers
are used for ventilation and heating.
D. Belt Tensions and Adjustments
Belt tension is adjusted during the initial run-in and test
periods at the factory. However, the belts are run as
slack as possible to prevent excessive damage to the
bearings, yet tight enough to prevent slippage.
It is necessary, therefore, to tighten all belts during the
fi rst few months of operation, and to
check for proper
tension weekly during
the
fi rst 60 days,
after which
30-day check intervals are suffi cient.
NOTE: Turn off all power to the equipment before
checking belt tensions.
CAUTION: Do not attempt to tighten any belt or belts
by changing the pitch of an adjustable pulley, as this
will change the speed of a driven pulley, causing the
unit to be rendered OUT OF AIR BALANCE. Do not
overtighten belts.
Suggested Belt Tension Method is with the use of a
Belt Tension Checker
1. Check tension frequently during the fi rst 24-48
hours of run-in operation. Ideal tension is the
lowest tension at which the belt will not slip under
peak load conditions. Over tensioning shortens belt
and bearing life.
Alternate Belt Tension Method
2. To properly tension a conventional V-belt drive use
the following procedure:
a. Measure the span length.
b. At the center of the span, apply a force perpen-
dicular to the span to defl ect the belt 1/64 inch
for every inch of span length. For example, for a
40 inch span, apply a force that will defl ect the
belt 40/64 or 5/8 of an inch.
c. Compare the force you have applied with the
values given in the table below. If the force is
between the values for normal tension and 1-1/2
times normal tension, the belt tension should be
satisfactory. If the belt tension is not within this
range, it can be adjusted by loosening the motor
mounting bolts, and adjusting the position of the
motor along its base.
Содержание IOMDFCDFM-1
Страница 43: ... 43 ...
Страница 44: ...4830 Transport Drive Dallas TX 75247 Phone 214 638 6010 Fax 214 905 0806 www appliedair com ...