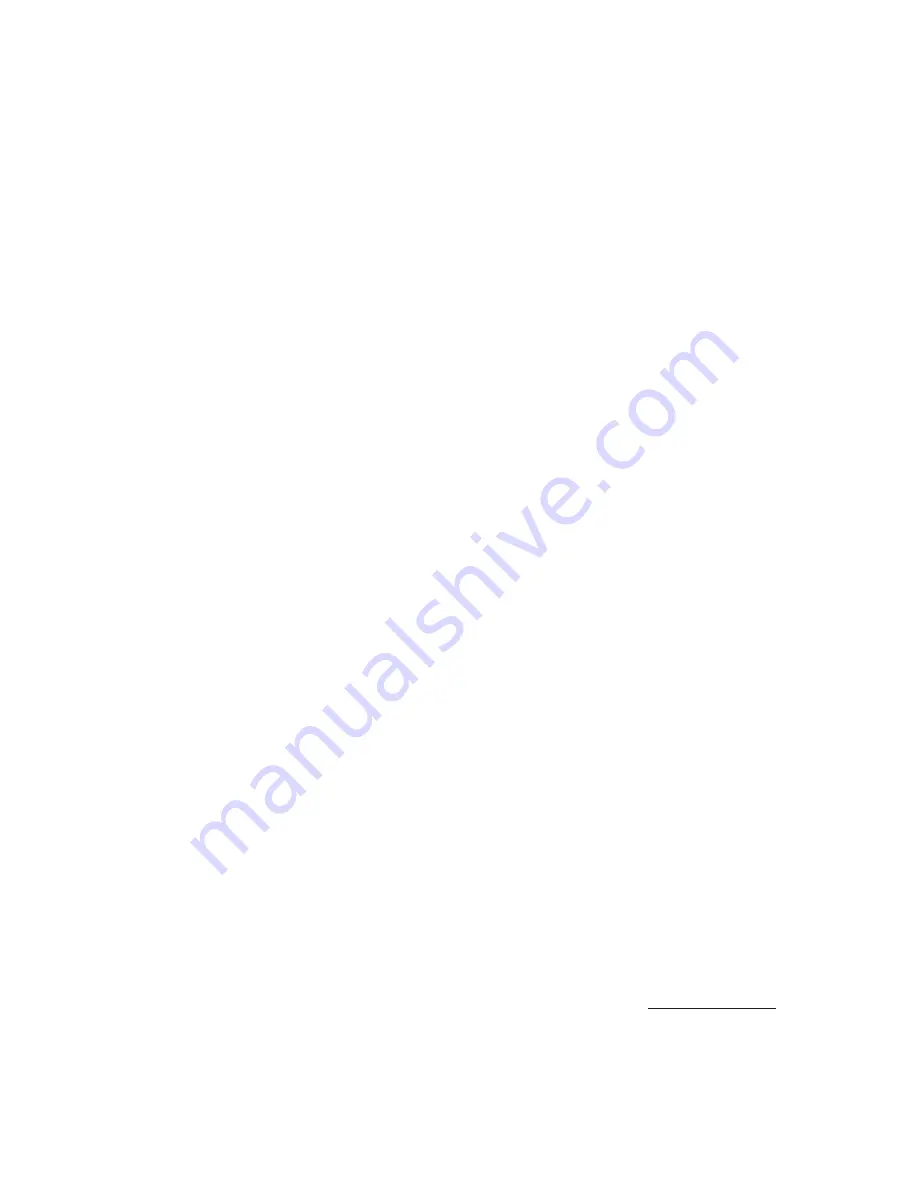
– 10 –
SECTION IV - PRE START-UP
Do not attempt start-up without completely reading
and understanding this manual, along with the
Digital Control Sysem user manual.
Pre Start-Up
The owners representative or equipment operator
should be present during start-up to receive instructions
on care and adjustments of the equipment.
All equipment has been factory tested, adjusted, metered
and inspected to meet conditions set at the time the
order was placed. Only minimal adjustments should be
required. All information in this service manual is typical.
All products are semi-custom and changes may occur.
CAUTION: Line side of disconnect may be energized.
Follow proper “lockout/tagout” procedures.
NOTE: All servicing and adjustments of the Direct
Gas-Fired unit should be performed by a qualifi ed
service engineer.
Perform a visual inspection, internally and externally,
to make sure no damage has occurred and that every-
thing is secure. This inspection is very important and
should be completed with greatest care given to detail.
A good pre-start inspection will insure against possible
unit damage on start-up and will save valuable analy-
sis time.
1. Check that the physical condition of the unit
exterior is acceptable.
2. Check that the insulation inside of unit is properly
secured.
3. Remove all shipping blocks, brackets and bolts
from supply fan base with optional isolation base.
4. Check all terminals for loose connections and
inspect all wiring terminations to insure that all
crimped connections are tight.
5. Inspect all fan and motor bearings and lubricate if
necessary.
CAUTION: DO NOT RUPTURE GREASE SEALS.
6. Inspect pulleys and belts for tightness, tension and
alignment.
Do not overtighten belts.
7. Check set screws on all bearings, pulleys, fans and
couplings for tightness.
8. Check voltage supplied to disconnect switch; the
maximum voltage variation should not exceed ± 10%.
Phase voltage unbalance must not exceed 2%.
9. Check that all relays are securely plugged into the
electronic relay board.
10. Check thermostat(s) for normal operation.
11. Check to ensure all manual reset safety devices
have been reset and limits are in the normal
operating position.
12. Check that system duct work is installed and free
from obstructions.
13. Check that fans turn free in housing.
14. Check that the area around the unit is clear of
fl ammable vapors or containers of fl ammable liquids.
15. Check that all piping connections, particularly
unions, are tight. Check all gas piping for leaks
using a soap bubble solution. The most common
types of problems found relative to the gas train
itself is foreign material within the gas piping. This
will interfere with the proper operation of the gas
train components and burner. Purge all air from gas
lines per gas codes.
16. Check that all accessories requiring fi eld wiring
have been properly installed.
17. Check burner for proper location and alignment.
18. Check that fi lters, fi lter stops, accessories and ship
loose items are installed correctly.
19. Check that vent lines (if applicable) are run to
atmosphere on gas regulators and pressure
switches for indoor units. Vent lines should
terminate outside the building, with a turndown
elbow and bug screen. Note that some units will use
vent limiters and vent lines are not required. If vent
lines are even partially plugged, this will interfere
with proper venting of pressure control devices.
20. Check that all manual gas shut-off valves are closed.
21. Check that inlet gas pressure is the same as shown
on the rating plate.
22. When failure or malfunction of this heater creates a
hazard to other fuel burning equipment, (e.g. when
the heater provides make-up air to a boiler room),
the heater is to be interlocked to open inlet air
dampers or other such devices.
23. Motor overload relay setting should match the mo-
tor’s nameplate full load amperage.
24. Check that dampers and linkages are free to move,
and that linkages are tight.
25. The unit may require that a Return Airfl ow Station
be fi eld installed. Be sure all tubing connections
are in the correct location as shown in drawing
#C000643.
26. If inlet duct is attached to the heater, a purge
timer must be provided and set to purge 4
times the inlet duct volume.
Purge time in seconds = 4 x L x W x H x 60
SCFM
L = duct length in feet, W = duct width in feet,
H = duct height in feet, SCFM = rating plate air
throughput.
Refer to the electrical schematic for the proper
circuit placement. Purge timer P/N 65.0711.00.
Содержание IOMDFCDFM-1
Страница 43: ... 43 ...
Страница 44: ...4830 Transport Drive Dallas TX 75247 Phone 214 638 6010 Fax 214 905 0806 www appliedair com ...