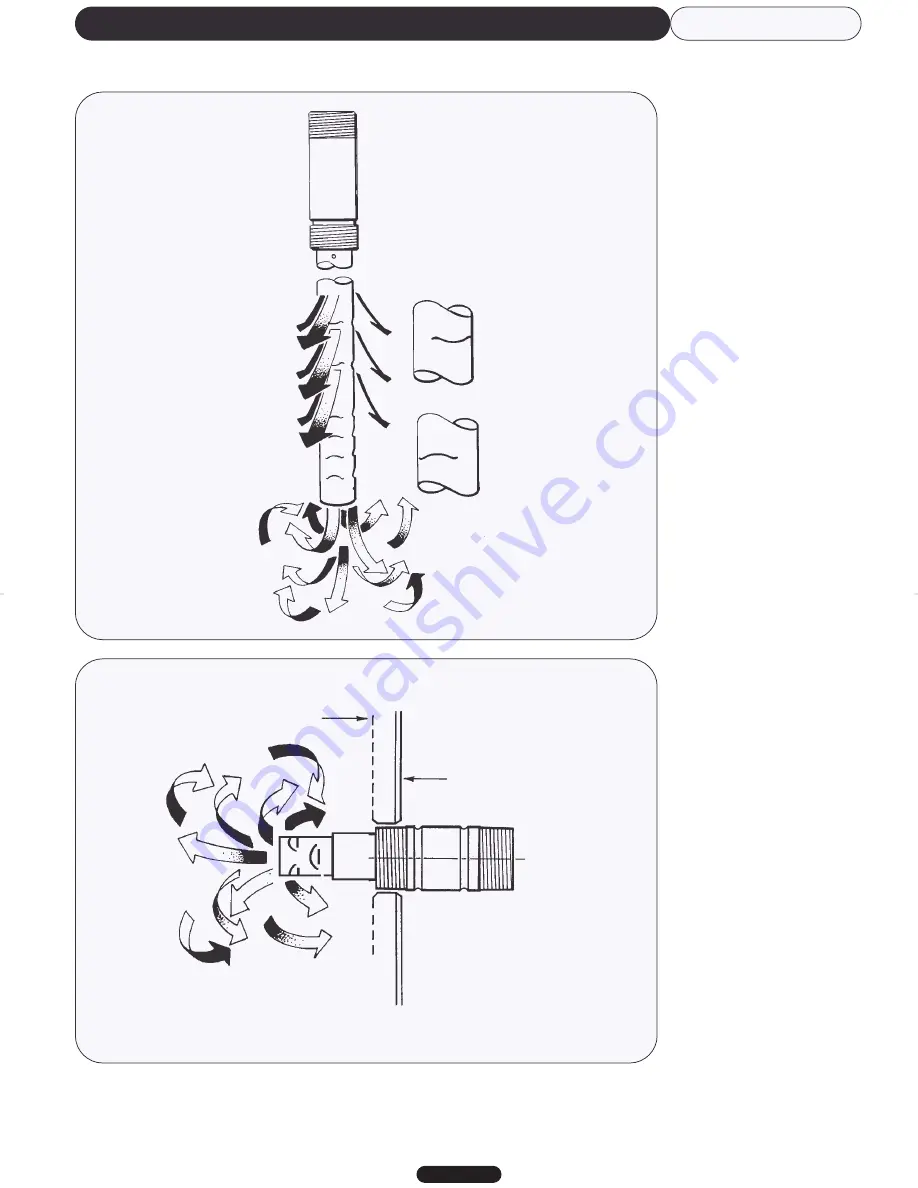
17
INSTALLATION
SECTION 3
WATER
CONNECTIONS
Hydrojet System
The upper “jet
ports” direct the
flow outward to
begin the dynamic
mixing action.
The lower “jet
ports” direct the
flow inward to
increase the
turbulence.
The heater is fitted with the Hydrojet Total Performance System incorporated in the cold
inlet dip tube. The tube is designed to increase turbulence and reduce sediment build up,
reduce thermal stacking and increase delivery.
Mini
Hydrojet Inlet Nipple
(Side Cold Inlet
Connection)
All models now incorporate the
new Mini Hydrojet system on
cold inlet side connections.
This system ensures water is
directed onto the tank base
which minimises sediment build
up from day one of installation.
Heater Casing
Tank
Содержание 24/39
Страница 11: ...11 INSTALLATION SECTION 3 Standard Range Hi FloRange Fig3a Fig3b ...
Страница 19: ...19 INSTALLATION SECTION 3 Fig 6A Fig 7 ...
Страница 23: ...23 INSTALLATION SECTION 3 WATER CONNECTIONS Fig 9 Fig 10 ...
Страница 26: ...26 INSTALLATION SECTION 3 WATER CONNECTIONS Fig 13 Fig 14 ...
Страница 29: ...29 INSTALLATION SECTION 3 WATER CONNECTIONS Fig 17 Fig 18 ...
Страница 50: ...46 Hi Flo Model 32 143 Hi Flo Models 65 173 and 81 264 50 PARTS LIST AND ILLUSTRATIONS SECTION 9 ...
Страница 52: ...52 PARTS LIST AND ILLUSTRATIONS SECTION 9 Hi Flo Models 62 341 and 54 418 440 ...
Страница 56: ...56 PARTS LIST AND ILLUSTRATIONS SECTION 9 24 Volt Auto System Kit B258 24 Volt Auto System Kit B217 ...
Страница 93: ...93 Notes ...
Страница 94: ...94 Notes ...
Страница 95: ...95 Notes ...