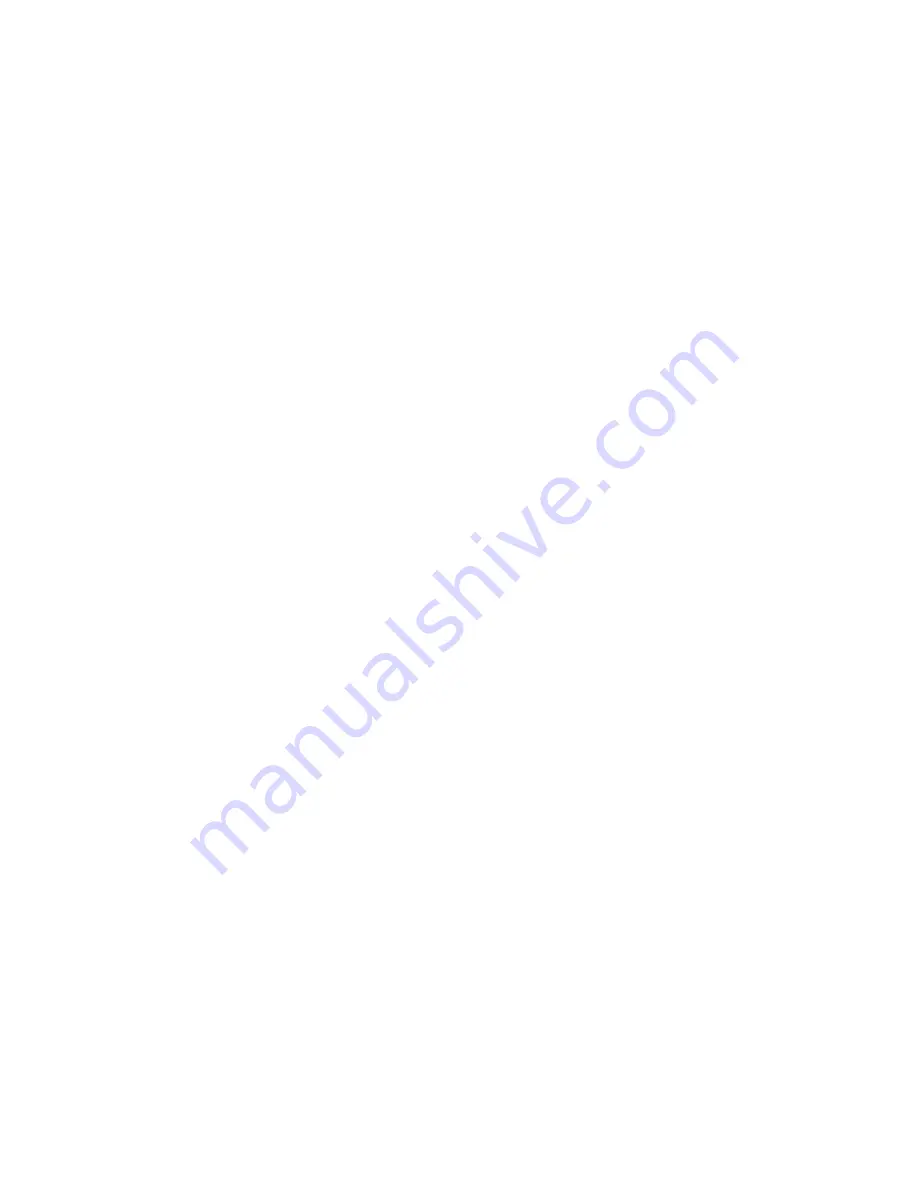
24
#L010120
November 2001
Direct mode is used to directly control motion for real time movements through serial communication.
The PCL501(PC) has 20 commands which are easy to remember for direct movement of a step motor.
COM Port Settings
Baud Rate:
Select one from the Baud Rate Selection chart in section 1.
Data Bits:
8
Parity:
None
Stop Bits:
1
Flow Control:
Xon/Xoff
Unit Selection
In order to select a unit the @ command followed by the address of the unit must be sent.
NOTE: There should be no spaces between the @ and address select.
How to select a unit:
@0
(Unit 0 is selected)
@1
(Unit 1 is selected)
@29 (Unit 29 is selected)
How to get a response from a unit:
@0$ (Carriage Return)
After the $ command, the PCL501(PC) will return a SMC50 + the current version number.
Note: In direct talk mode each command is followed by a carriage return.
The unit communicates in half duplex mode, therefore proper setup of hyper terminal is necessary to view
characters, if characters are to be echoed back to the screen.
Section 4: Direct Talk Mode
Instructions
All instructions require that no spaces be sent between the command and the parameter followed by a
carriage return.
(@0 not @ 0)
Command Summary:
A
- Acceleration/Deceleration
B
- Base Speed
G
- Go Number of Steps
H
- Home
I
- Read Inputs
J
- Jog Speed
L0
- Get Limit Status
LS
- Soft Limit Input Bit
M
- Max Speed
N
- Number of Steps
O
- Set Outputs
P
- Absolute Position
S
- Go Slew
V
- Verify
Z
- Position
.
- Stop Motion
+
- Clockwise Direction
-
- Counterclockwise Direction
$
- Version Number Register
!
- Error Codes Register
July 2018
L010121