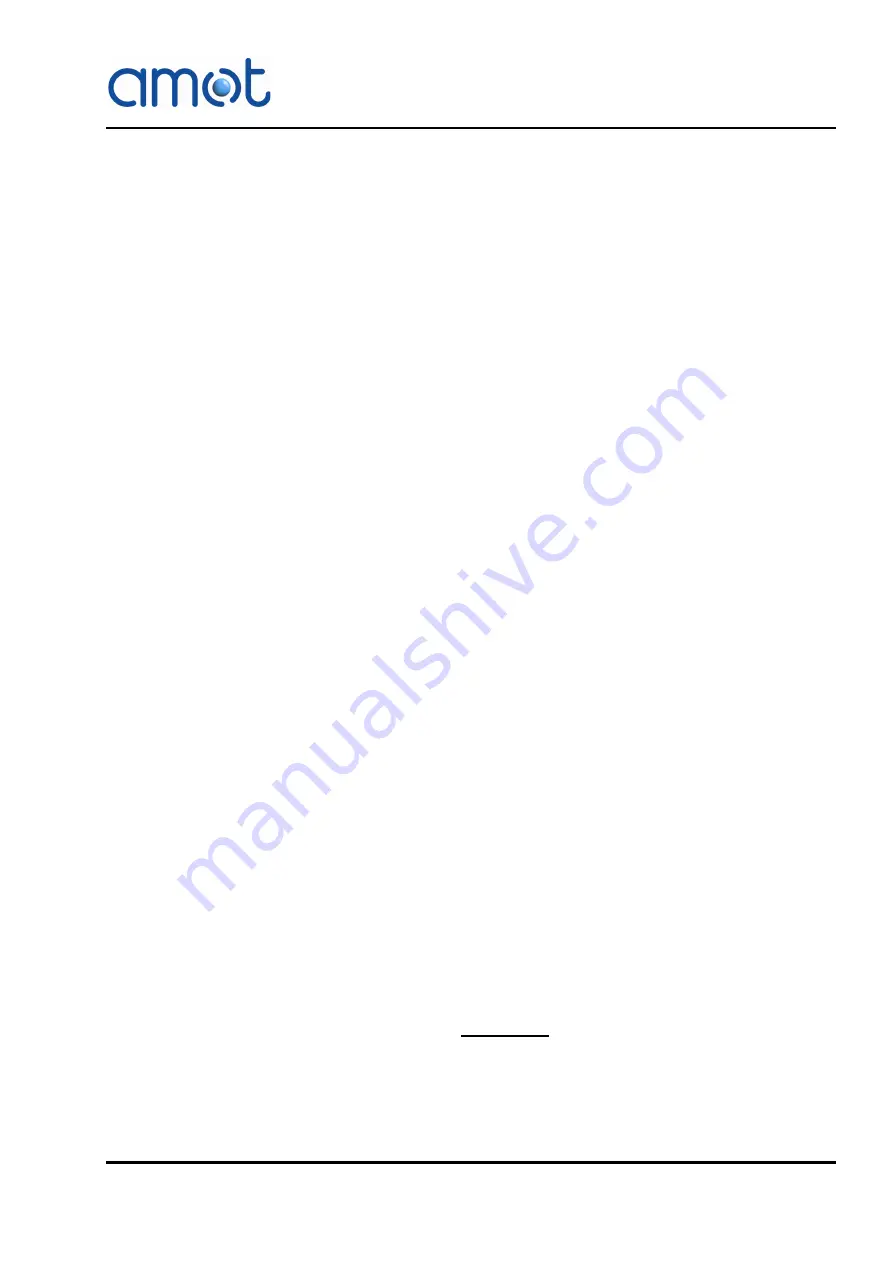
41
Electric Actuator
OMMG00012
Rev 12 – NOV 2019
14
Connect the replacement limit switch pair wires to the terminal strip.
15
Slide the cams and cam spacer (12) onto the position indicator shaft.
Whilst viewing the actuator as illustrated, ensure the cam grubscrews are
facing you when the flats face the switches.
16
Position the upper limit switch bracket (9) and slide down the shaft with
the cams.
17
Secure the limit switch assembly with the two screws (22).
18
Slide the large spur gear (7) onto the shaft. Do not tighten the grubscrew
at this point.
19
Slide the potentiometer bracket (3) onto the shaft and secure with screw
(30) and washer (29).
20
Refit the motor strap (16) through the slot in the terminal strip bracket
and around the motor and capacitor. Ensure the capacitor sits snugly
against the motor on the anti-vibration block (14).
21
Refit the position indicator to the top of shaft. Manually wind the actuator
to each end of travel and ensure the indicator aligns with the scale on the
cover.
22
Use new cable ties to secure the potentiometer wires to the
potentiometer bracket and potentiometer bracket mounting pillar.
23
Carry out limit switch adjustment in accordance with Sect 4.8.4
24
Carry out potentiometer adjustment in accordance with Sect 4.8.7.
4.8.4
Limit Switch Adjustment – Rotor Not Visible
The limit switches and mechanical end stops are set by the manufacturer and
should not need adjustment unless the cams or switches are replaced or
disturbed. During manufacture, the limit switches are set up relative to the
valve fully open and closed positions. The mechanical end stops are then set in
position, a further two complete turns of the manual operating handle.
This procedure assumes that observation of the valve rotor is not possible
(installed in pipework) and sets the limit switches relative to the factory set
mechanical end stop positions.
CAUTION
During adjustment of the limit switches, the actuator must be
manually positioned. If the actuator is mounted on a valve which is
installed in the pipework, it will affect the process flow of the system.
Adjust the limit switches as follows (refer to Fig 13, page 40):
WARNING
Lethal voltages are exposed when the actuator cover is removed,
presenting an electric shock hazard to personnel. Electrical power
supplies must be isolated from the actuator before the cover is
removed.
Содержание 10GEF
Страница 1: ...Doc No OMMG00012 Revision 12 NOV 2019 G Valve electric actuator Operation and Maintenance Manual...
Страница 2: ......
Страница 14: ...14 System Overview Rev 12 NOV 2019 OMMG00012...
Страница 26: ...26 Electric Actuator Rev 12 NOV 2019 OMMG00012 Fig 7 EA Actuator Internal Wiring Without Positioner...
Страница 28: ...28 Electric Actuator Rev 12 NOV 2019 OMMG00012 Fig 9 EA Actuator Internal Wiring With Positioner...
Страница 52: ...52 Electric Actuator Rev 12 NOV 2019 OMMG00012...
Страница 54: ...54 PID Controller Rev 12 NOV 2019 OMMG00012...
Страница 64: ...64 System Integration Rev 12 NOV 2019 OMMG00012 Fig 22 System Wiring Diagram 8072D Controller...
Страница 67: ...67 System Integration OMMG00012 Rev 12 NOV 2019...
Страница 68: ...68 System Integration Rev 12 NOV 2019 OMMG00012...
Страница 74: ...74 Technical Data Rev 12 NOV 2019 OMMG00012 9 1 1 Valve Bore Fig 25 Valve Selection Curve...