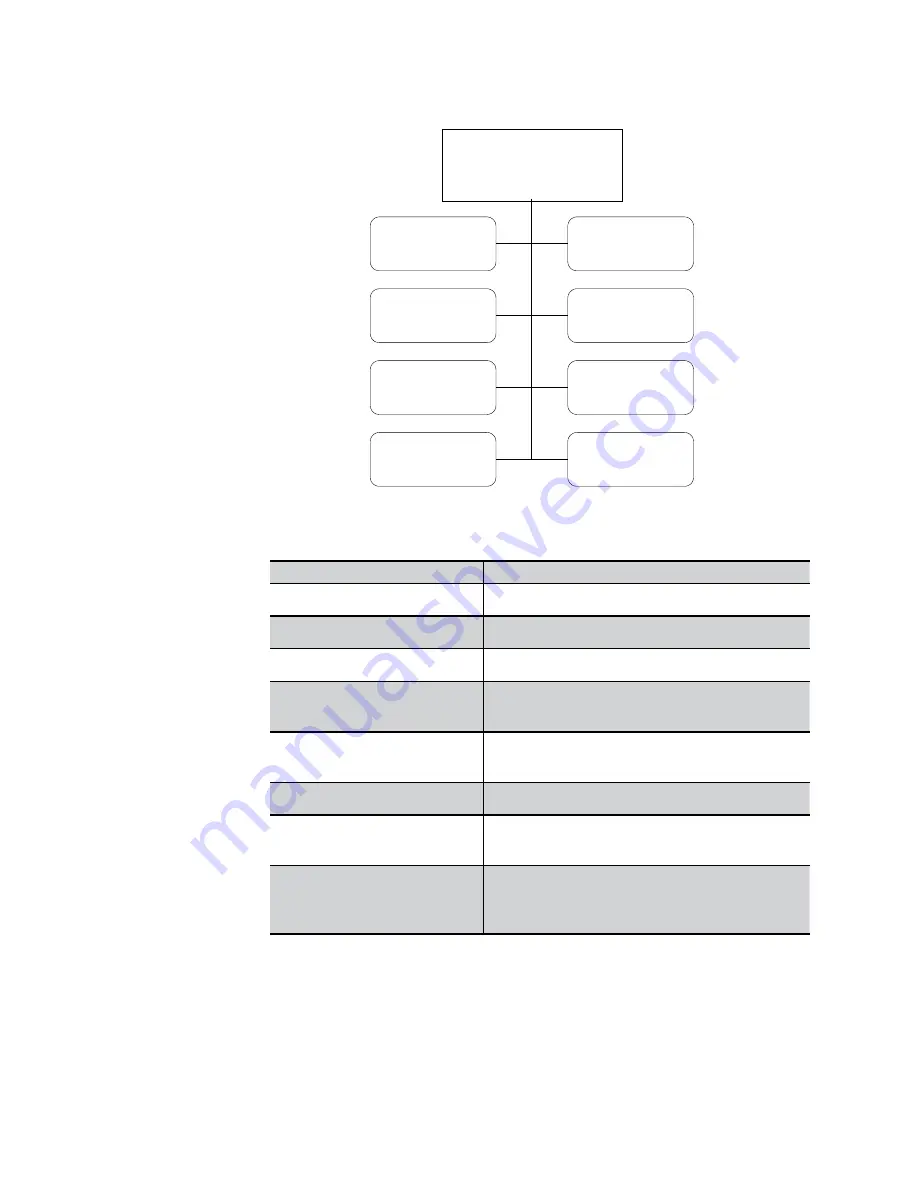
Controller / User Interface
|
4-5
Setup Key
Display
System Tests
Primary Calib
Pump
Passwords
System Serial #
Communications
Carrier Gas
SETUP KEY
Figure 4-1. Setup Key menu options.
Setup Key Menu
Function/Options
Display
Select info for Display Lines 1, 2 and 3
Passwords
Create a system password
System Tests
Perform internal diagnostics
System Serial #
View Serial Number and manufacturing num-
ber
Primary Calibration
Perform an automatic, remote, or manual pri-
mary calibration
Communications
Define communication parameters
Pump
Turn thepump on or off. Applies only ifyou have
the optional pump installed.
Carrier Gas
Define the carrier gas to deliver the calibration
gases. This menu option also allows you to
calibrate your flow sensor.