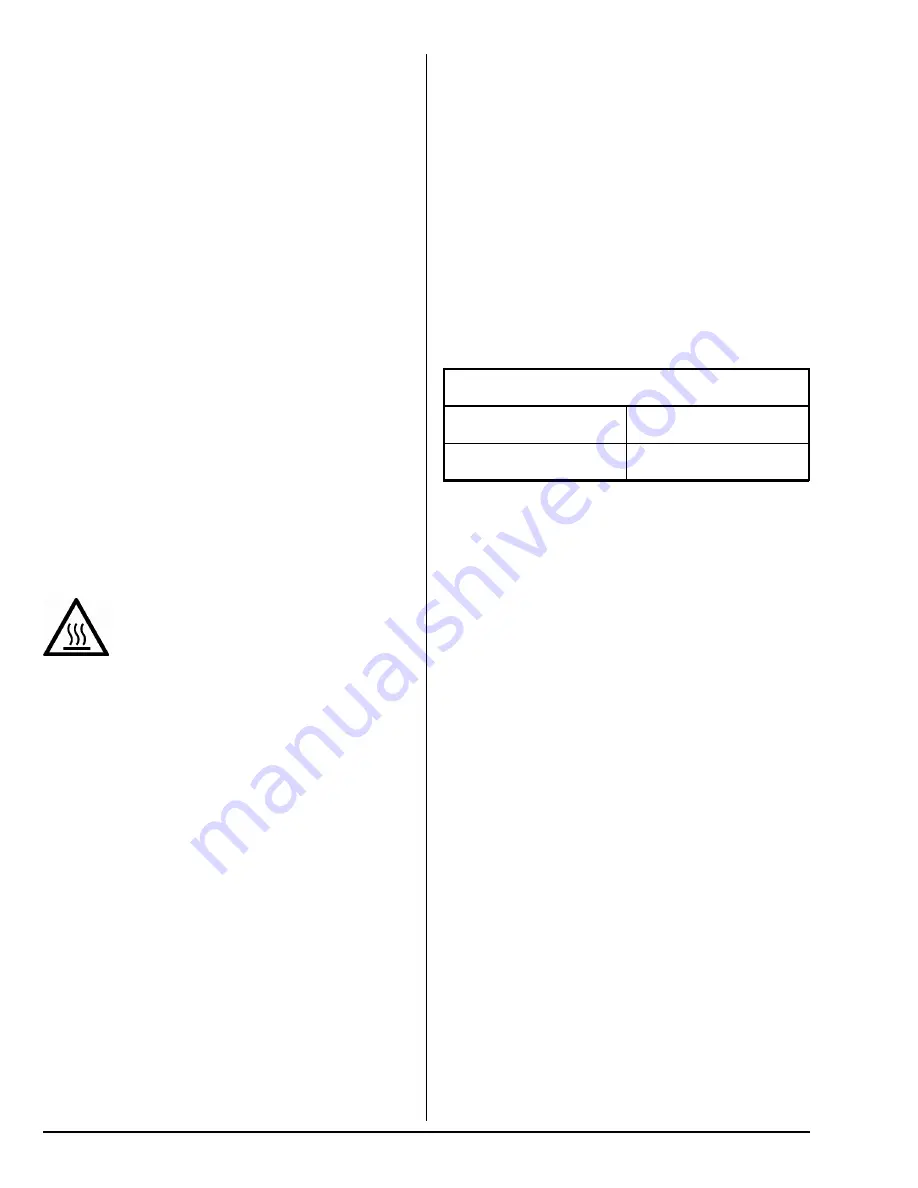
12
American Dryer Corp.
113576 - 1
3. Back out the miniature screw inside the outlet pressure
tap (“out P”) (G).
4. Attach a manometer to pressure tap (G).
5. Turn the gas valve’s switch (H) to the “ON” position.
6. Continue electrical power to the dryer.
7. Run a “heat” cycle and wait for burner ignition.
8. Gas manifold pressure can now be measured.
9. If the gas pressure does not need adjustment then
disconnect electric power and go to Step 10, otherwise:
9.1. Disconnect electrical power to the dryer.
9.2. Regulator screw is under the regulator cap (F)
9.3. Remove the regulator cap (F) and turn the plastic
adjustment screw to alter the pressure (clockwise to
increase, or counterclockwise to decrease).
9.4. Continue electrical power to the dryer.
9.5. Run a “heat” cycle and wait for burner ignition.
9.6. Gas manifold pressure can now be measured.
9.7. If the manifold pressure needs further adjustment then
return to “Step 9.1.”
9.8. Disconnect electrical power to the dryer.
9.9. Replace the regulator cap (F).
10. Turn the gas valve’s switch (H) to “OFF” position
11. Remove manometer and tighten pressure tap screw (G).
12. Turn the gas valve’s switch (H) to “ON” position
13. Continue electrical power to the dryer.
Steam Information ______________
Steam installation should be performed by
qualified personnel in accordance with national
and local safety regulations.
Care must be taken when leveling a steam dryer to promote
good steam coil drainage. Return lines should be level or
pitched down slightly for good drainage.
The steam supply to the coil must be from the top of a well-
dripped steam main. If the supply run-out to the dryer exceeds
6 meters then it should be dripped just before the control valve
with a proper trap and dirt pocket.
The normal pH level for copper-type steam coils must be
maintained between 8.5 and 9.5. For steel-type steam coils
the pH level must be between 9.5 to 10.5. These limits are
required to limit the acid attack of the steam coils.
Properly sized steam supply, and return, lines are required to
avoid poor performance.
Clean, dry steam must be provided to the dryer.
The steam supply connection into the main supply line must
be made with a minimum 25 cm riser. This will prevent any
condensate from draining towards the dryer.
The steam supply line to the dryer must include a 30 cm riser
along with a drip trap and check valve. This will prevent any
condensate from entering the steam coil.
Flexible hoses or couplings must be used. The dryer vibrates
slightly when operating which could cause steam connections
to crack if they are hard piped.
Horizontal sections of steam supply piping should be pitched
back towards the steam supply header (minimum slope of 1
cm for every meter) to allow any condensation to flow back
into the header. Install a bypass trap in any low point to eliminate
wet steam.
Failure to comply with the above requirements can result in
water hammer, premature component failure, and will void the
warranty.
Steam Supply Requirements
Maximum Pressure
1.0 MPa
Minimum Pressure
0.7 MPa
Shutoff valves for each dryer should be installed in the supply
line, return line, and drip trap return line. This will allow the
dryer to be isolated from the steam supply if the dryer will be
serviced.
The supply and return lines should be insulated to save energy
and provide safety to maintenance personnel.
Install a 3/4-inch vacuum breaker at the steam coil (as shown)
to prevent coil damage from acids formed in a vacuum.
Mount steam solenoid valve in orientation show (coil up).
A standard steam dryer comes with a 24VAC solenoid valve
that is shipped in the dryer’s lint compartment. Electric
connections are in the rear of the dryer (top right).
AD-50i
Install an inverted bucket steam trap and check valve at least
30 cm below the steam coil return connection, and as close to
the coil as possible. A trap, with a minimum capacity of 95.2 kg
of condensate per hour (at 1.0 MPa), is needed for each unit
(based on twice the steam consumption per hour). Refer to the
schematic later in this section.
AD-80i
Install an inverted bucket steam trap and check valve at least
30 cm below each steam coil return connection, and as close
to the coil as possible. Two traps, with a minimum capacity of
63.5 kg of condensate per hour (at 1.0 MPa), are needed for
each unit (based on twice the steam consumption per hour).
Refer to the schematic later in this section.