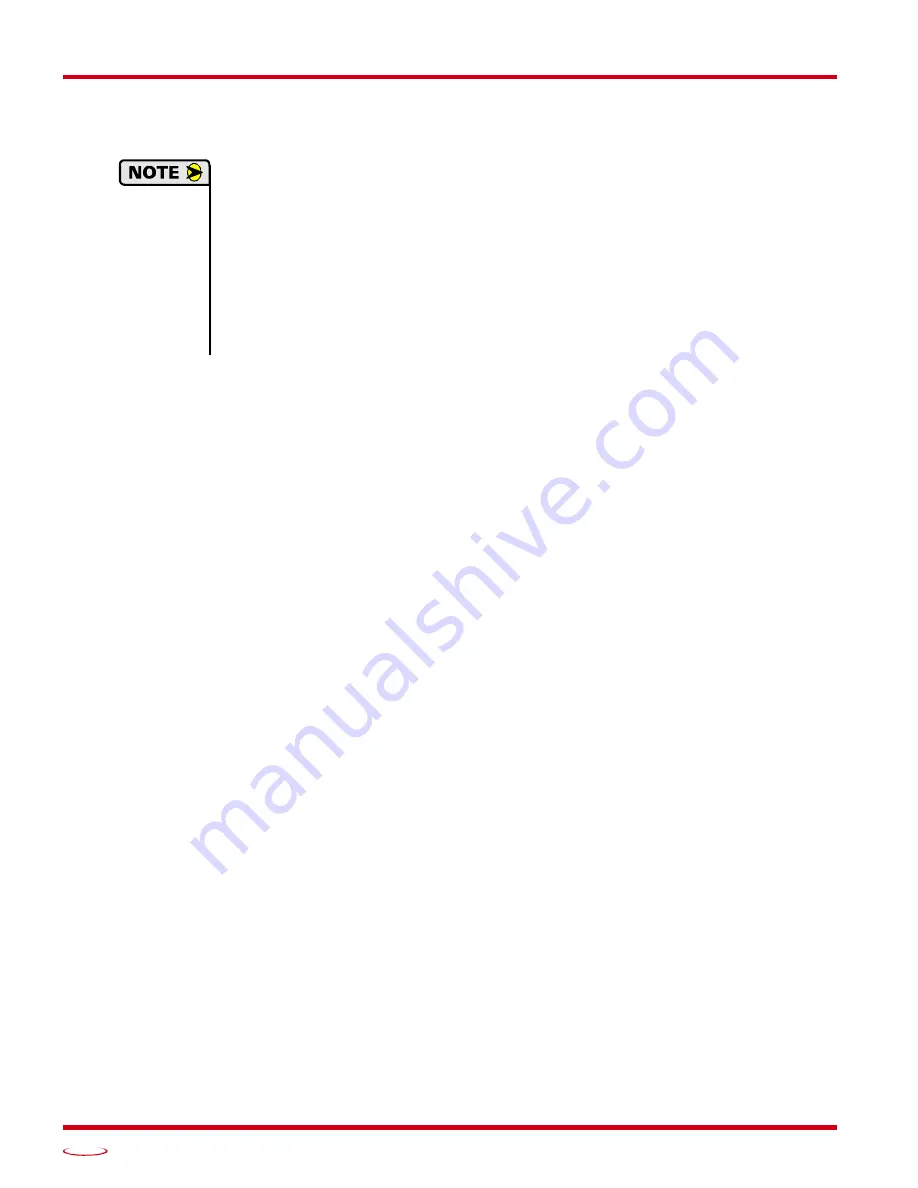
M
OTION
C
ONTROL
SMD23E2 and SMD24E2 User Manual
ADVANCED MICRO CONTROLS INC.
38
Assembled Moves (continued)
Blend Move (continued)
1) You do not have to preset the position or home the machine before you can use a Blend Move.
Because the Blend Move is based on Relative Moves, it can be run from any location.
2) The Blend Move is stored in the internal memory of the SMD23E2 or SMD24E2 and can be
run multiple times once it is written to the unit. The Blend Move data stays in memory until
power is removed, the unit is sent new Configuration Data, or a new Blend or Dwell Move is
written to the unit. As described in
Saving an Assembled Move in Flash
on page 40, it is
also possible to save a Blend Move to flash memory. This move is restored on power up and
can be run as soon as you configure the SMD23E2 or SMD24E2 and enter Command Mode.
3) There are two control bits used to specify which direction the Blend Move is run in. This
gives you the ability to run the Blend Move in either direction.
Controlled Stop Conditions
The move completes without error.
You toggle the Hold_Move control bit in the Network Output Data. When this occurs, the SMD23E2 or
SMD24E2 decelerates the move at the deceleration rate of the present segment to the Starting Speed
and ends the move. Note that your final position will most likely not be the one you commanded. A
Blend Move that is brought to a controlled stop with the Hold_Move bit cannot be restarted. The use of
the Hold_Move bit is explained in the
section starting on page 43.
Immediate Stop Conditions
The Immediate_Stop bit makes a 0
1 transition in the Network Input Data.
A positive transition on an input configured as an E-Stop Input.
A CW or CWW Limit Switch is reached. If the limit that is reached is the same as the direction of
travel, for example, hitting the CW limit while running a CW move, a
Reset Errors
command must be
issued before moves are allowed in that direction again. If the limit that is reached is opposite the direc-
tion of travel, a
Reset Errors
command does not have to be issued.
Dwell Move
A Dwell Move gives you the ability to string multiple relative moves together and run all of them sequentially
with a single start condition. Like a Blend Move, a Dwell Move is programmed into an SMD23E2 or SMD24E2
as a series of relative moves before the move is started.
Unlike a Blend Move, the motor is stopped between each segment of the Dwell Move for a programed
Dwell
Time
. The Dwell Time is programmed as part of the command that starts the move. The Dwell Time is the same
for all segments. Because the motor is stopped between segments, the motor direction can be reversed during
the move. The sign of the target position for the segment determines the direction of motion for that segment.
Positive segments will result in clockwise shaft rotation while a negative segment will result in a counter-clock-
wise shaft rotation.
Содержание SMD23E2 Series
Страница 10: ...ABOUT THIS MANUAL SMD23E2 and SMD24E2 User Manual ADVANCED MICRO CONTROLS INC 10 Notes...
Страница 44: ...MOTION CONTROL SMD23E2 and SMD24E2 User Manual ADVANCED MICRO CONTROLS INC 44 Notes...
Страница 54: ...CALCULATING MOVE PROFILES SMD23E2 and SMD24E2 User Manual ADVANCED MICRO CONTROLS INC 54 Notes...
Страница 68: ...CONFIGURATION MODE DATA FORMAT SMD23E2 and SMD24E2 User Manual ADVANCED MICRO CONTROLS INC 68 Notes...
Страница 88: ...COMMAND MODE DATA FORMAT SMD23E2 and SMD24E2 User Manual ADVANCED MICRO CONTROLS INC 88 Notes...
Страница 124: ...ETHERNET IP EXPLICIT MESSAGING SMD23E2 and SMD24E2 User Manual ADVANCED MICRO CONTROLS INC 124 Notes...
Страница 128: ...MODBUS TCP CONFIGURATION SMD23E2 and SMD24E2 User Manual ADVANCED MICRO CONTROLS INC 128 Notes...
Страница 134: ...LEADERS IN ADVANCED CONTROL PRODUCTS ADVANCED MICRO CONTROLS INC...