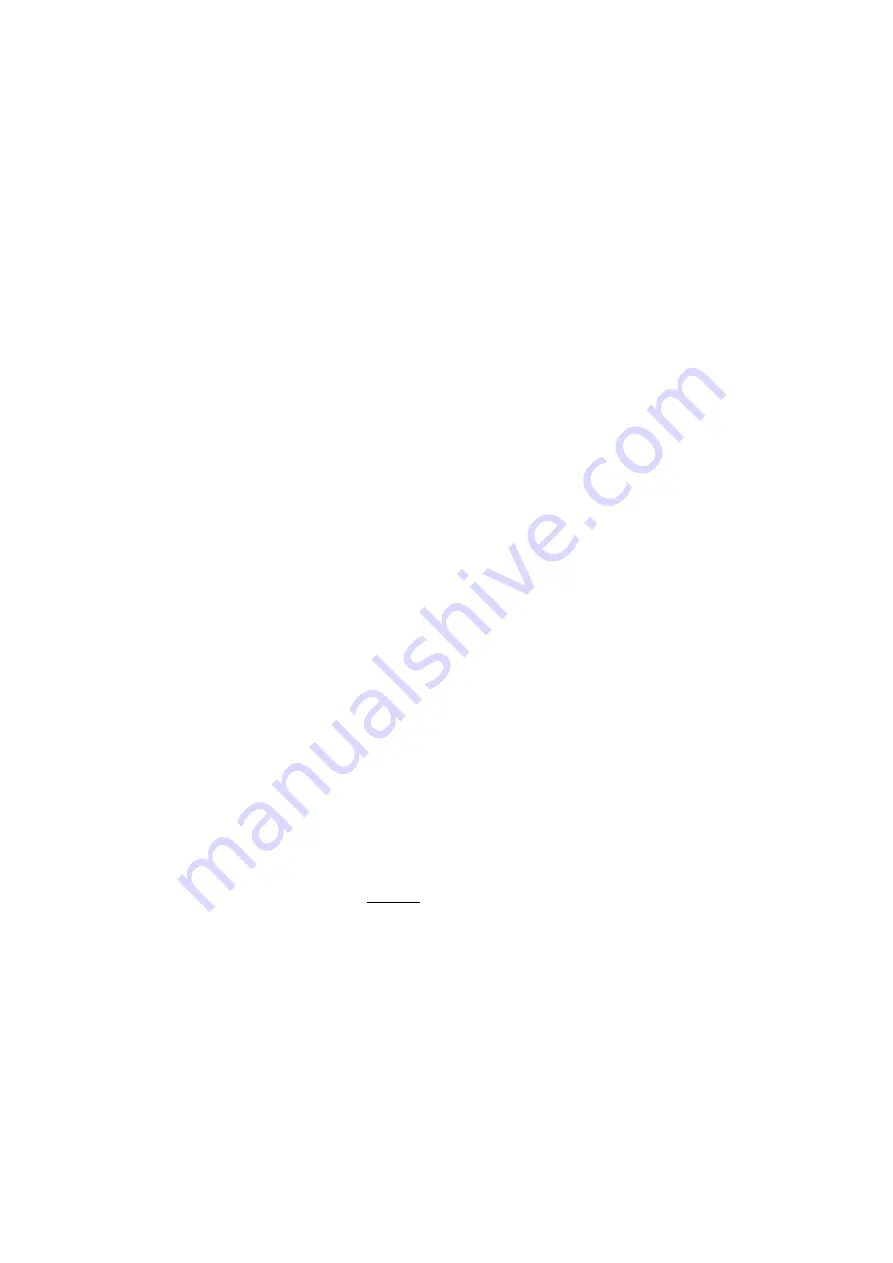
Ambic Equipment Ltd - AutoFoamer Operating Notes
-7 -
AF7500 (01.01.15)
Initial Setting Up
Leave the Foam Applicator at the far end of the distribution line disconnected and, in its place, fit a short length
of tube resting in a suitable container in order to collect any chemical discharged.
Switch on the power at the electric socket and on the front of the pumping unit. Power Unit (
A1
) will be
activated and liquid will start to be drawn up through the pump(s). Allow unit to run until liquid has passed
through the pump(s) and is flowing out in a continuous stream from the end of the distribution pipe (this may
take a few minutes on a system with a long distribution line). At this point, turn Off the unit and fit the final
applicator. Briefly remove the plug from the T-piece below the small enclosure (
A2
) replacing it as soon as liquid
runs out, to ensure liquid has reached the pressure switch.
Switch the pump unit back On and, when the Pressure Reservoir Bottle (
W
) has been filled to a level of about
30mm, and a liquid pressure of ~3psi (0.2 Bar) is reached, the pressure switch will automatically switch off the
peristaltic pump(s), which will not operate until a gun is used and pressure drops. If pumps fail to stop within
1 minute (or run continuously) then check the distribution line system for leaks.
Switch on the air supply, adjust the pressure regulator initially to 3 – 4 psi and check the quality of foam by
depressing the trigger on each applicator in turn. Initially the foam may not be produced until a continuous
stream of liquid has reached the base of the foaming cup; priming each applicator should take no more than a
few seconds and is accomplished by holding the trigger fully depressed until foam fills the applicator cup.
Foam Quality/Wetness may be adjusted by regulating the relative liquid to air pressure ratio. The unit will have
been preset in the factory to a near optimum liquid pressure and it is therefore preferable to adjust the air
pressure to arrive at the desired foam quality. Increasing Air pressure will make the foam more “dry” (very
frothy and tending towards larger air bubbles), whilst decreasing air pressure will both reduce the rate of
production of foam and make the foam “wetter” ultimately to the extent where foam collapses very quickly to
leave fluid in applicator cup. The difference in air pressure between these extremes typically covers the pressure
range of 2 – 6 psi (with liquid pressure set at 3 psi). Generally the Air pressure should be within ±2 psi of Liquid
pressure.
OPERATION
When ready to dip, depress the trigger until foam is level or just above the rim of Applicator (F) and raise fully
onto teat. Typically a full cup will dip two teats.
WARNING – Refill chemical container(s) BEFORE EMPTY and SWITCH OFF PUMP UNIT whilst refilling. In the
event that chemical supply is exhausted, it will be necessary to re-prime system as described in the section
“Initial Setting Up” above.
WHEN MILKING IS COMPLETED SWITCH OFF ELECTRIC POWER SUPPLY and rinse out cups with warm
water.
WARNING – AFTER MILKING IS COMPLETE ALWAYS ISOLATE MAINS POWER FROM PUMPS (this action is
essential to avoid possible loss of chemical through leakage and damage to pump motors).
SPECIFICATIONS
Power Source – Liquid
– Electric Pumping unit
•
220-240Vac 50Hz 120/240W
– Fuses
• Single Pump T0.4A
• Twin Pump T1.0A
Power Source – Air
– Compressed Air
•
5 -10L/min at 3 - 7psi (0.2 - 0.5 Bar)
Maximum No. of Applicators per Pumping Unit
•
10
Maximum No. of Applicators operating simultaneously
•
2
Maximum Length of Distribution Tubing (Black or Grey/ Blue) •
45 Metres (150 ft)
Typical Chemical Consumption per Applicator
•
1.5 – 2.5 mL/second
Operating Temperature
•
5 – 40
°
C