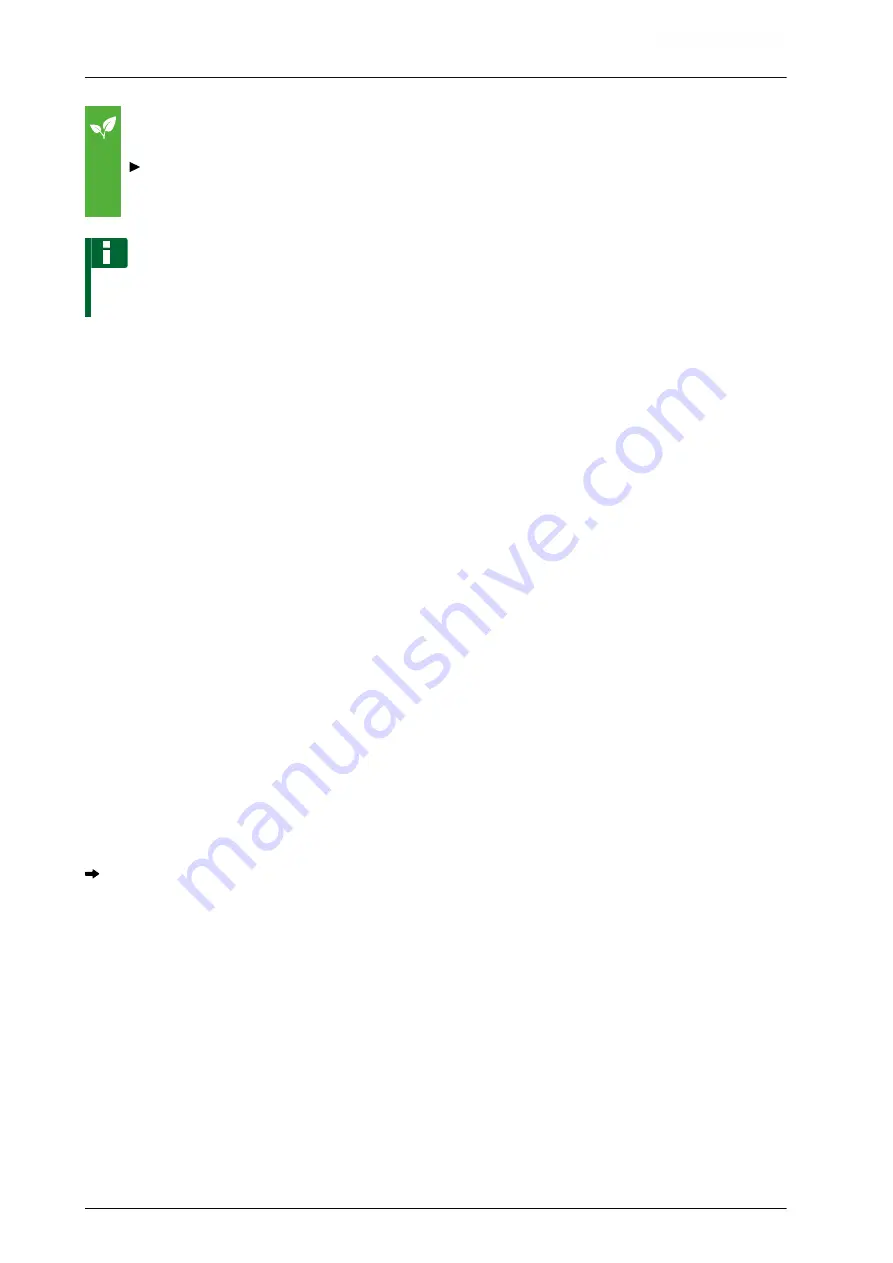
ENVIRONMENTAL INFORMATION
Indicates a risk for environmental
damage.
NOTE
Indicates application tips and instructions for
optimal use.
1.1.3 Instructions
XXXX Numbered instructions
Actions that have to be performed in a specific
sequence are represented as numbered instructions.
The specified sequence of the actions must be
observed.
Example:
1.
Instruction 1
2.
Instruction 2
1.1.3.1 Instructions and responses
Reactions to instructions are marked with an arrow.
Example:
1.
Instruction 1
Reaction to instruction 1
2.
Instruction 2
1.1.3.2 Alternative instructions
Alternative instructions are introduced with the word
"or".
CMS-T-00000473-B.1
CMS-T-005217-B.1
CMS-T-005678-B.1
CMS-T-00000110-B.1
1 | About this operating manual
Diagrams
MG6212-EN-II | C.1 | 12.04.2021
2