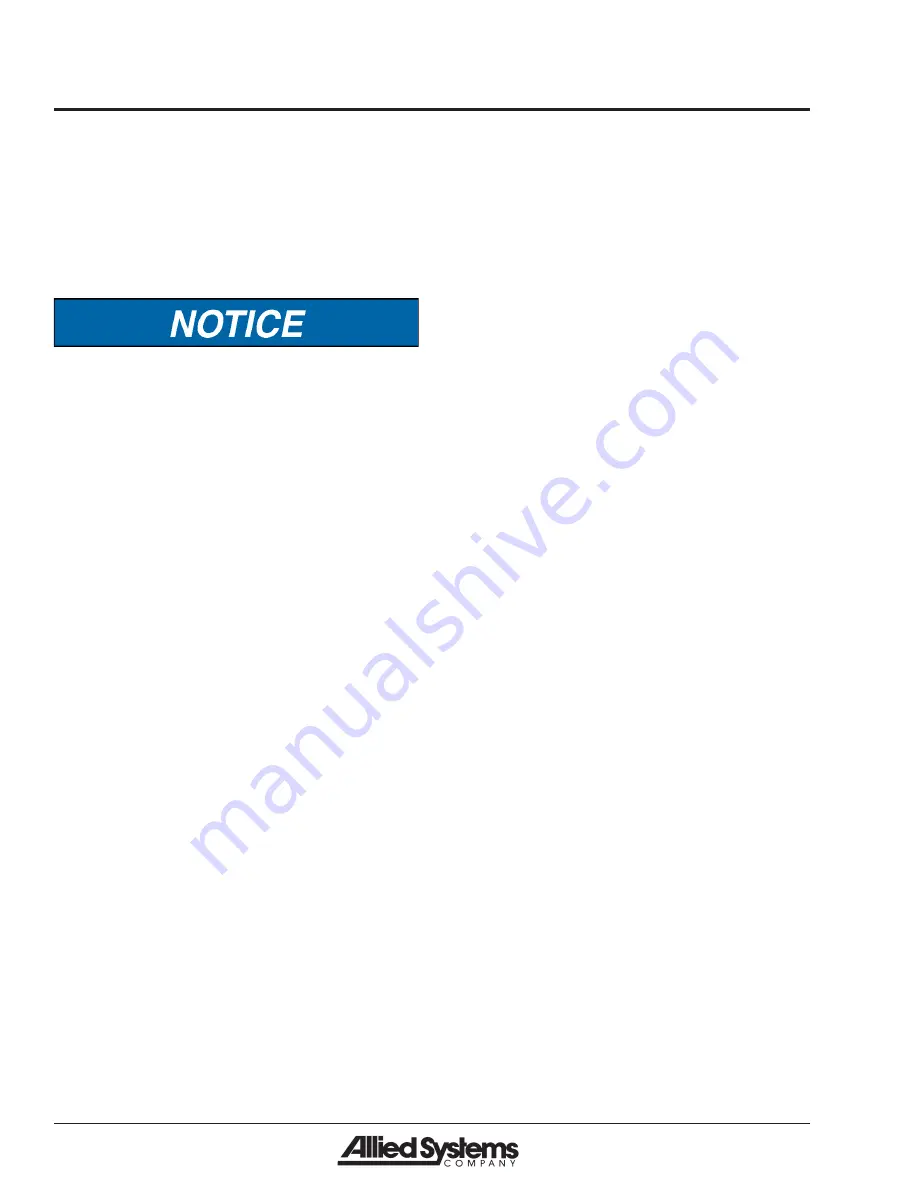
10
45-074, REV. 5/18
3.15 Industry Standards
ANSI/ITSDF B56.1-2016 is the published sequence and
direction standard for lever- and hand-type controls.
The chart on the following page shows
industry standards. Your equipment may
be different. If you do not routinely operate
this equipment, refresher training is
recommended. You must reacquaint
yourself with this manual and the equipment
before starting, and then proceed slowly.
Special controls such as automatic devices should be
identified, preferably according to the recommendations
in Figure 3-6.
When a function is controlled by a pair of push buttons,
they should operate in the same sense as the lever con-
trols. For example, pushing a button located to the rear
(relative to the operator’s position) should serve the same
function as moving a control lever to the rear.
3.16 Clamp Open Control
Effective October 7, 2010, safety standard ANSI/ITSDF
B56.1, Section 7.25.7 covers all lift trucks with a load
bearing clamp (paper roll clamp, carton clamp, etc.),
and requires the driver to make two distinct motions
before opening or releasing the clamp. For example,
you must press a switch and then move a lever to
unclamp the load. This requirement applies to new
and used attachments being mounted on trucks which
shipped from the factory after October 7, 2010, and is a
recommended feature to be installed on dealer orders
and existing applications.