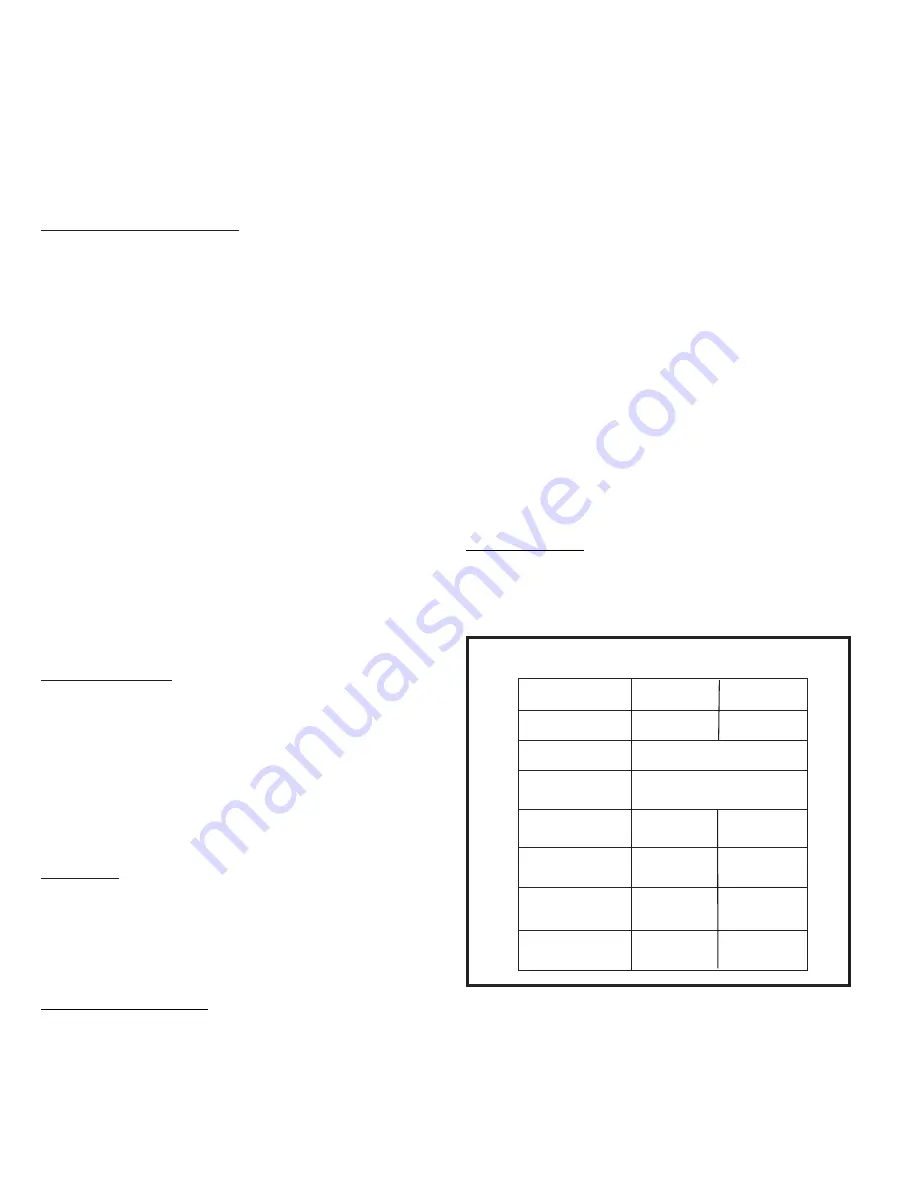
Page 16 of 24
506762-01
Issue 1143
During a single demand cycle, the defrost control will lock
out the unit after the fifth time that the circuit is interrupted
by any pressure swtich wired to the control board. In addition,
the diagnostic LEDs will indicate a locked-out pressure switch
after the fifthe occurrence of an open pressure switch (see
Table 11). The unit will remain locked out until power to the
board is interrupted, then re-established, or until the jumper
is applied to the TEST pins for 0.5 seconds.
NOTE: The defrost control board ignores input from the
low pressure switch terminals as follows:
During the TEST mode
During the defrost cycle
During the 90 second start-up period
For the first 90 seconds each time the reversing valve
switches heat/cool modes
If the TEST pins are jumpered and the 5 minute delay is
being bypassed, the LO-PS terminal signal is not
ignored during the 90 second start-up period.
Diganostic LEDs
The defrost board uses two LEDs for diagnostics. The LEDs
flash a specific sequence according to the condition as
shown in Table 11.
Mode
Green LED
Red LED
No Power
to Board
Normal Operation/
Power to Board
OFF
OFF
Anti-Short Cycle
Lockout
Simultaneous Slow Flash
Low Pressure
Switch Fault
Low Pressure
Switch Lockout
High Pressure
Switch Fault
High Pressure
Switch Lockout
Alternating Slow Flash
OFF
OFF
OFF
OFF
Slow Flash
Slow Flash
ON
ON
Table 11
Defrost Control Board Diagnostic LEDs
The control provides automatic switching from normal
heating operation to defrost mode and back. During the
compressor cycle (call for defrost), the control accumulates
compressor run time at 30, 60, 90 minute field adjustable
intervals. If the defrost thermostat is closed when the
selected compressor run time inter ends, the defrost relay
is energized and the defrost begins.
Defrost Control Timing Pins
Each timing pin selection provides a different accumulated
compressor run time period during one thermostat run cycle.
This time period must occur before a defrost cycle is initiated.
The defrost interval can be adjusted to 30 (T1), 60 (T2), or
90 (T3) minutes. The defrost timing jumper is factory
installed to provide a 90 minute defrost interval which is the
optimum efficiency setting. If the timing selector jumper is
not in place, the control defaults to a 90 minute defrost
interval. The maximum defrost period is 14 minutes and
cannot be adjusted.
A test option is provided for troubleshooting. The test mode
may be started any time the unit is in the heating mode and
the defrost thermostat is closed or jumpered. If the jumper
is in the TEST position at power-up, the control will ignore
the test pins. When the jumper is placed across the TEST
pins for 2 seconds, the control will enter the defrost mode.
If the jumper is removed before an additional 5-second period
has elapsed (7 seconds total), the unit will remain in defrost
passed. If the jumper is not removed until after the additional
5-second period has elapsed, the defrost will terminate and
the test option will not functioin again until the jumper is
removed and reapplied.
Compressor Delay
The defrost board has a field-selectable function to reduce
occasional sounds that may occur while the unit si cycling in
and out of the defrost mode. The compresor will be cycled
off for 30 seconds going in and out of the defrost mode when
the compressor delay jumper is installed.
NOTE: The 30-second “OFF” cycle is deactivated if the
TEST pin is removed.
Time Delay
The timed-off delay is 5 minutes long. The delay helps to
protect the compressor from short cycling in case the power
to the unit is interrupted or a pressure switch opens. The
delay is bypassed by placing the timer select jumper across
the TEST pins for 0.5 seconds.
Pressure Switch Circuit
The defrost control includes two pressure switch circuits. A
high pressure switch is connected to the board’s HI-PS
terminals. The low pressure, or loss-of-charge pressure,
switch is connected to the LO-PS terminals.