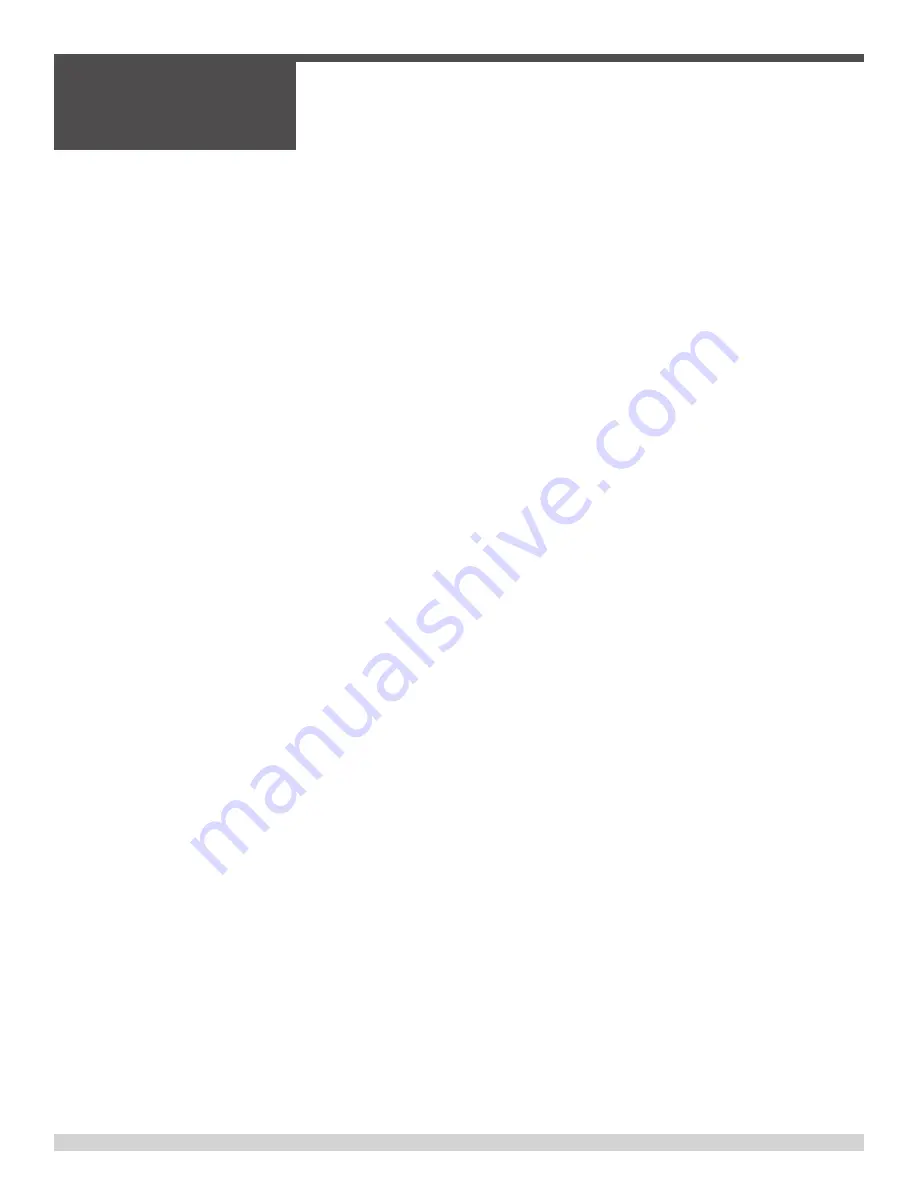
SECTION 3
SERVICE
064633
Page 42
The following list contains information regarding the maintenance and operations procedures that must be adhered to
improve the life of your machine. A well maintained piece of machinery will provide you years of satisfaction.
• Use Loctite anti-seize MIL A 907D to lubricate the top pipe coupler threads before assembly.
• Oil winch bushings at 10 hr. operation intervals. Use light lubricating oil.
• CAUTION! Change worn or frayed cables - cables under tension may snap and cause severe injury. Use proper
methods illustrated in this manual to properly attach cables. ALWAYS connect cables properly - wrap cable under last
form pin then connect cable hook to the next form pin towards the screed.
• DO NOT hook cables to a stake driven into the ground, the stake can tilt and allow cable under tension to snap back
and cause severe injury.
• CAUTION! For Screeds over 75ft. in length consult the factory.
• ALWAYS make sure that the drive shaft is aligned properly. To make sure that you do this correctly you will need to
utilize AEC tool part number 020255.
•
When connecting drive shafts, assemble with all the weights on each section facing the bull-float blade. if weights
are mis-matched, the screed will no vibrate properly. Match the key-ways on the drive shafts and the connectors.
• Do not over speed, engine RPM must not exceed 3600 RPM. Shaft speed will not exceed design limits if engine speed
maximum is adhered to.
•
DO NOT crown or invert without universal joints or flex couplers on the shaft connectors.
• Maintain engine in accordance with the manufacturer’s instructions.
• Grease screed bearings at 40 hr. operation intervals. Use one stroke of a hand grease gun. Use SHell Alvonia #21,
Texaco L-15, Chevron SR1. Clean fittings before greasing. For low temperatures, use Dow Molykote BR-2. DO NOT
OVER GREASE.
•
For cold weather operations, use bearing lubricant Allen BR-2. This grease flows at amients of -22°F~ thru 356°F.
• CAUTION! When installing pillow block bearings, be sure that the bottom flat surface does not have nicks or deep
marks. this can cause the bearing to ride off of the mounted surface; when vibration occurs this small deformation
can wear off quickly, allowing the bearing to loosen. With the bearing loose on its mounting, failure can occur.
Periodic Maintenance Schedule
Содержание SE12
Страница 17: ...SECTION 1 SAFETY 064633 Page 17 SECTION 1 SAFETY ...
Страница 18: ...SECTION 1 SAFETY 064633 Page 18 State Regulations Proposition 65 Warning ...
Страница 19: ...SECTION 1 SAFETY 064633 Page 19 Federal Regulation Respiratory Hazard ...
Страница 30: ...SECTION 1 SAFETY 064633 Page 30 Notes ...
Страница 31: ...SECTION 2 OPERATIONS 064633 Page 31 SECTION 2 OPERATIONS ...
Страница 41: ...SECTION 3 SERVICE 064633 Page 41 SECTION 3 SERVICE ...
Страница 45: ...SECTION 4 PARTS 064633 Page 45 SECTION 4 Parts ...
Страница 72: ...SECTION 4 PARTS 064633 Page 72 4 13 End Mount Engine Assembly Illustration ...