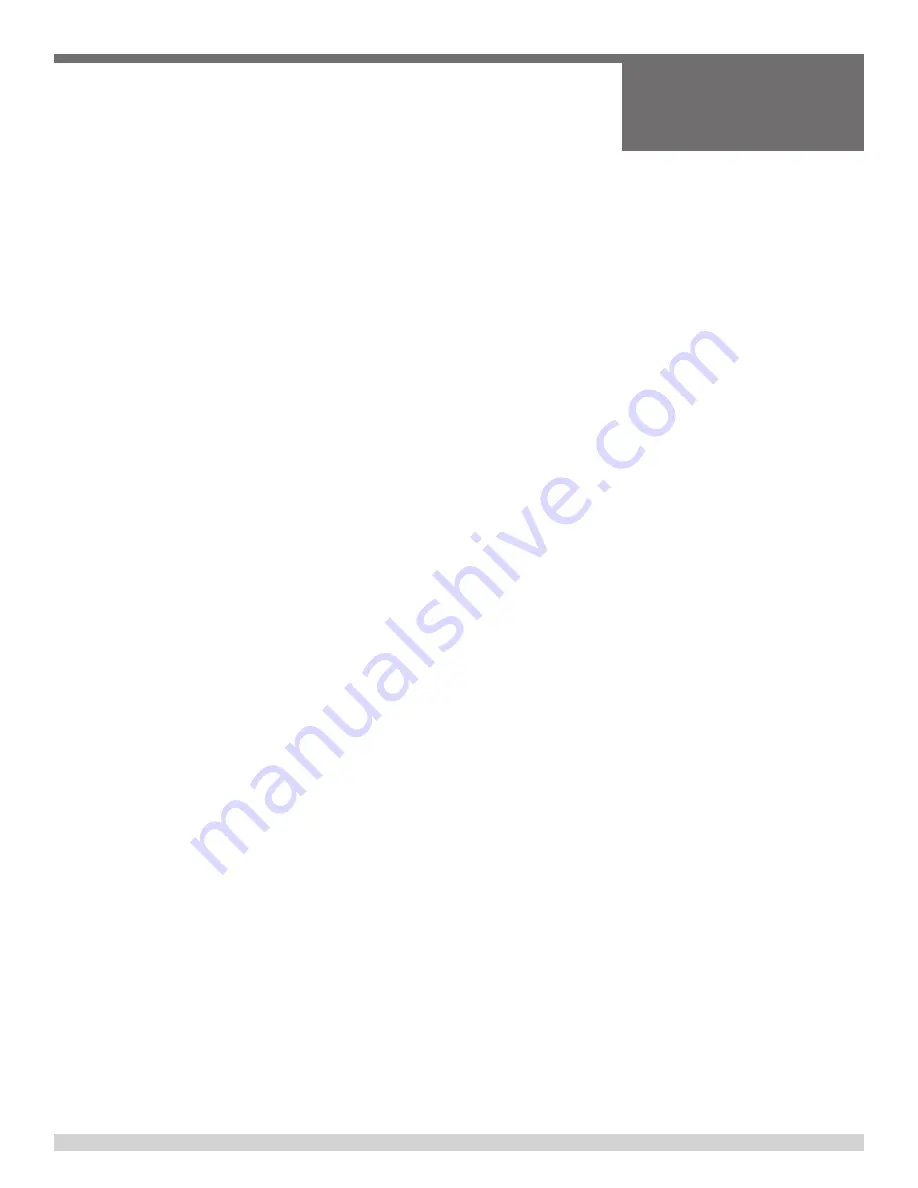
• Make sure the hitch and coupling of the towing vehicle are rated equal to, or greater than the trailer “gross vehicle
weight rating.”
• ALWAYS
inspect the hitch and coupling for wear. Never tow a trailer with defective hitches, couplings, chains, etc.
•
Check the tire air pressure on both towing vehicle and trailer. Trailer tires should be inflated to 50 psi cold. Also check
the tire tread wear on both vehicles.
• ALWAYS
make sure the trailer is equipped with a safety chain.
• ALWAYS
properly attach trailer’s safety chains to towing vehicle.
• ALWAYS
make sure the vehicle and trailer directional, backup, brake and trailer lights are connected and working
properly.
• DOT Requirements include the following:
- Connect and test electric brake operation.
- Secure portable power cables in cable tray with tie wraps.
• The maximum speed for highway towing is 55 MPH unless posted otherwise. Recommended off-road towing is not to
exceed 15 MPH or less depending on type of terrain.
•
Avoid sudden stops and starts. This can cause skidding, or jack-knifing. Smooth, gradual starts and stops will improve
towing.
• Avoid sharp turns to prevent rolling.
• Trailer should be adjusted to a level position at all times when towing.
• Raise and lock trailer wheel stand in up position when towing.
• Place chock blocks underneath wheel to prevent rolling while parked.
• Place support blocks underneath the trailer’s bumper to prevent tipping while parked.
• Use the trailer’s swivel jack to adjust the trailer height to a level position while parked.
• Use tie downs to ensure machine does not move during transportation.
SECTION 1
SAFETY
069971
Page 21
Transportation Safety