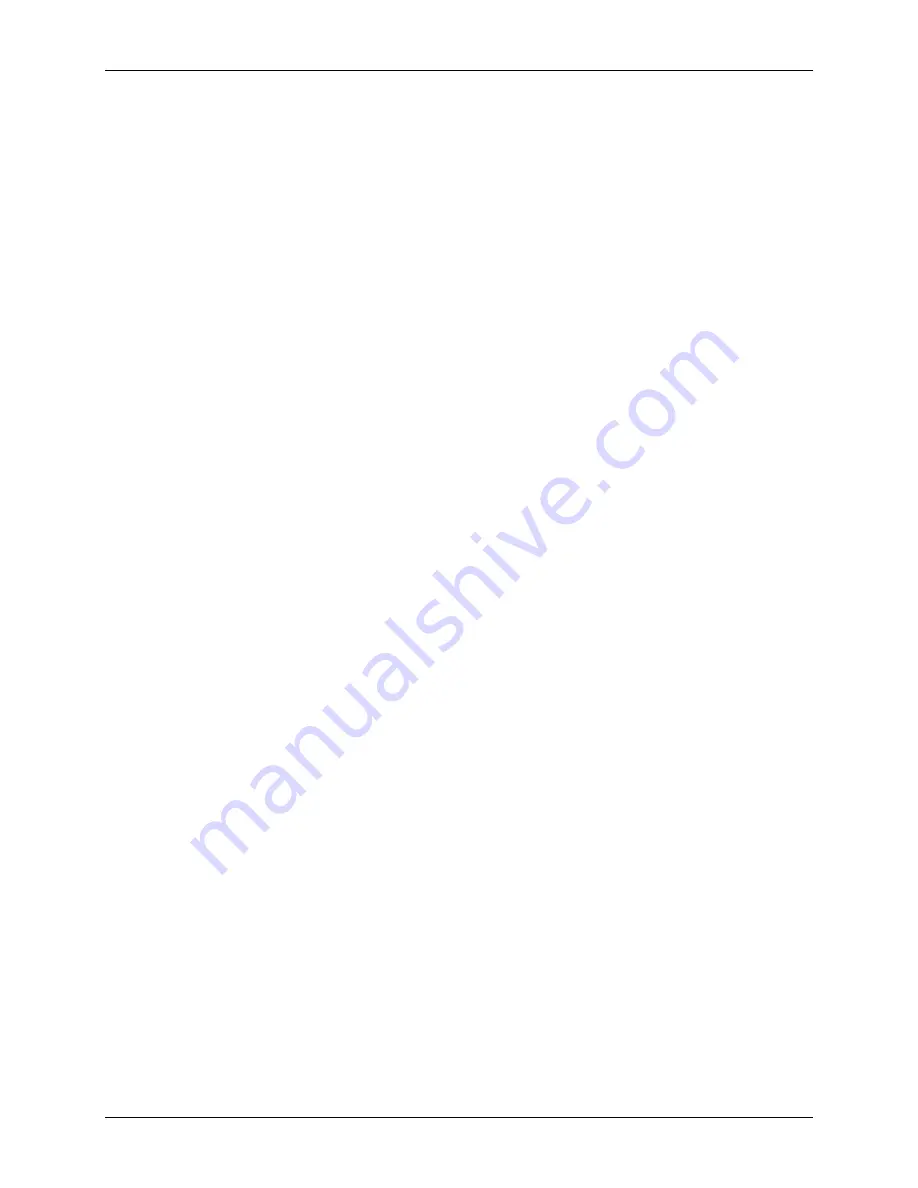
6
4. SPECIFICATIONS
Order
number
36646
Pump
Oil-lubricated
direct
drive
Motor
1,5 HP/1,1 kW
Voltage Single Phase
230 Volt
Air tank capacity
5 litres
Oil
tank
capacity
0,25
litres
Cut-in Pressure
6 bar
Cut-out Pressure
8 bar
Max. charge
30% per 60 minutes
Sound
pressure
77
dB(A)/7
m
Air intake capacity
215 l/min.
Weight
21
kg
Model changes reserved.
All compressors are provided with Euro-Norm (CE-Choice)
5. PARTS & FEATURES (page 1)
Drain valve :
used to drain condensation from the air tank. Located at bottom of
the tank.
Motor thermal overload:
the motor has an automatic thermal overload
protector. If the motor overheats, this protector will shut off the motor. The motor
must be allowed 30 minutes to cool before restarting.
Pressure switch:
this controls the power to the motor and also the cut-in/cut-
out pressure settings. This switch serves as the Auto-On/Off positions for the
unit.
Air intake filter:
provides clean air to the pump and must always be kept free of
debris. Check on a daily basis or before each use.
Air compressor pump
: oil lubricated direct driven pump that compresses air,
which is distributed to the tack.
Check valve:
when the pump is not in operation the valve closes to retain air
pressure inside the tank.
Pressure relief valve:
the pressure relief valve located behind the pressure
switch is designed to automatically release compressed air when the air
compressor reaches cut-out pressure. The release air should only escape
momentarily and the valve should then close.
Tank safety valve:
used to allow excess tank pressure to escape into the
atmosphere. This valve
should only open when the tank pressure is above the maximum rated pressure.
Outlet pressure gauge:
Indicates the outgoing air pressure to the tool and is
controlled by the regulator
Tank pressure gauge
Indicates the reserve air pressure in the tank.
Regulator:
the regulator controls the air pressure coming from the air tank. To
increase the pressure, turn the knob clockwise and to decrease the pressure
turn the knob counterclockwise.
Содержание LHR 215/5
Страница 1: ...COMPRESSOR LHR 215 5 36646 Instruction manual ...
Страница 3: ...1 Compressor 36646 Versie 02 2006 ...
Страница 19: ...COMPRESSOR LHR 215 5 Version 02 2006 ...