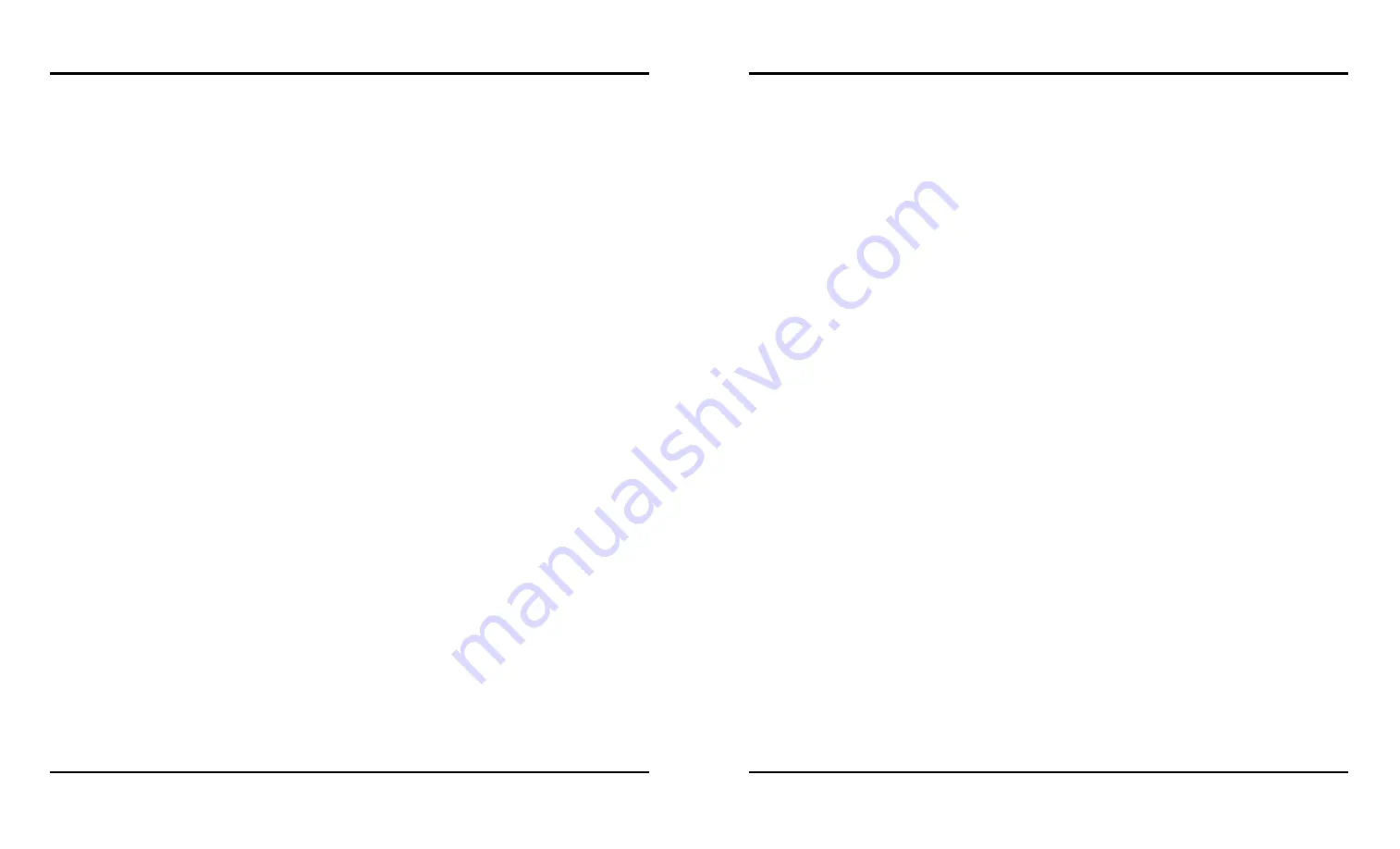
Section 7: Maintenance
Airmetrics
51
7 MAINTENANCE
Ideally, records reflecting the history of maintenance (including all replacement
parts, sup plies, costs, expend itures) shou ld be kep t for each M iniVol, alo ng with
an inven tory of on-h and spa re equipm ent.
Check sheets should be used to record preventative and/or corrective maintenance
activities and the subsequent sampler calibration curve.
The sampler is comprised of four basic components: preseparator/filter holder
assembly, flow control system, tim er, and battery pack . Following are
recom mend ed, routine mainten ance pro cedures for the sam pler’s basic
components.
Presep arator /Filter H older A ssemb ly
I
MPACTOR
C
LEANING
The preseparator/filter holder assembly should be dismantled and the impactor
cleaned and grea sed at regu lar intervals
)
i.e.
, every se venth sam ple to start, bu t if
heavy loadings are observed on the target disk, as often as appropriate.
1.
Unm ate the pre separato r sections fro m the filter a ssemb ly and rem ove the ra in
cap (see Figure 4.3 and 4.4).
2.
Pushing with the thumb from the bottom, remove the impactor through top of
the tube into the palm of your free hand.
3.
Rinse the impactor from top to bottom w ith a solvent (hexane, white gas,
lantern gas) using a squeeze bottle, paying particular attention to the impaction
target disks. An acceptable alternative method of cleaning involves the use of
an ultrasonic bath with mild soapy water solution.
Impaction plates on the impactor(s) should be removed prior to regreasing.
The impaction plate is attached to the impactor jet by spring tension only and
may be separated by simply pulling the jet from the impaction plate (see
Airmetrics MiniVol Users Guide
52
Airmetrics
Figure 7.1.
Regreasing PM
2.5
Impactor
Figure 7.1).
4.
Let the impactor air-dry.
5.
Prepare a mixture of solvent
and impactor grease in a
dropper bottle until tho roughly
mixed and of a flu id
consistency. Use a 1-inch
length of grease to 30 ml of
solvent. Vigorously shake the
mixture until an opaque,
uniform suspension, free from
grease globs, is obtained.
Other low-v apor pressure
greases, such as silicone, are acceptable. However, removing the dirty grease
from the impacto r parts ma y be m ore difficult.
6.
Put two or three drops of the cloudy solution on the target disk. The drops
should saturate the disk, flowing freely to the edge.
7.
Let the targ et disk "dr y" by allo wing the solvent to v olatilize, leav ing a thin
film of grease on the target disk.
8.
I n sp e c t t h e O - r in g s on t he i m pa c to r fo r fi tn e s s a n d re p la c e if n ec e s sa r y. O -
rings should be coated with a thin film of silicone lubricant prior to use.
Remove any extraneous, loose, or hair-like shredded material from the exterior
of the impactor unit since this material could fall onto the filter below and
cause erroneous gravimetric results. Carefully re-insert the impactor into the
top of the preseparator tube until the top of the impactor is flush with the top
of the tube.
Flow Control System
Tubing, pulse dampener, and fittings must be routinely checked for crimps, cracks,
or obstructions. Fittings should be inspected periodically for cross-threading and
tightness. The flowmeter should be cleaned or replaced if it indicates no flow, low
flow, excessive flow, or erratic flow. The flowmeter can be easily cleaned using