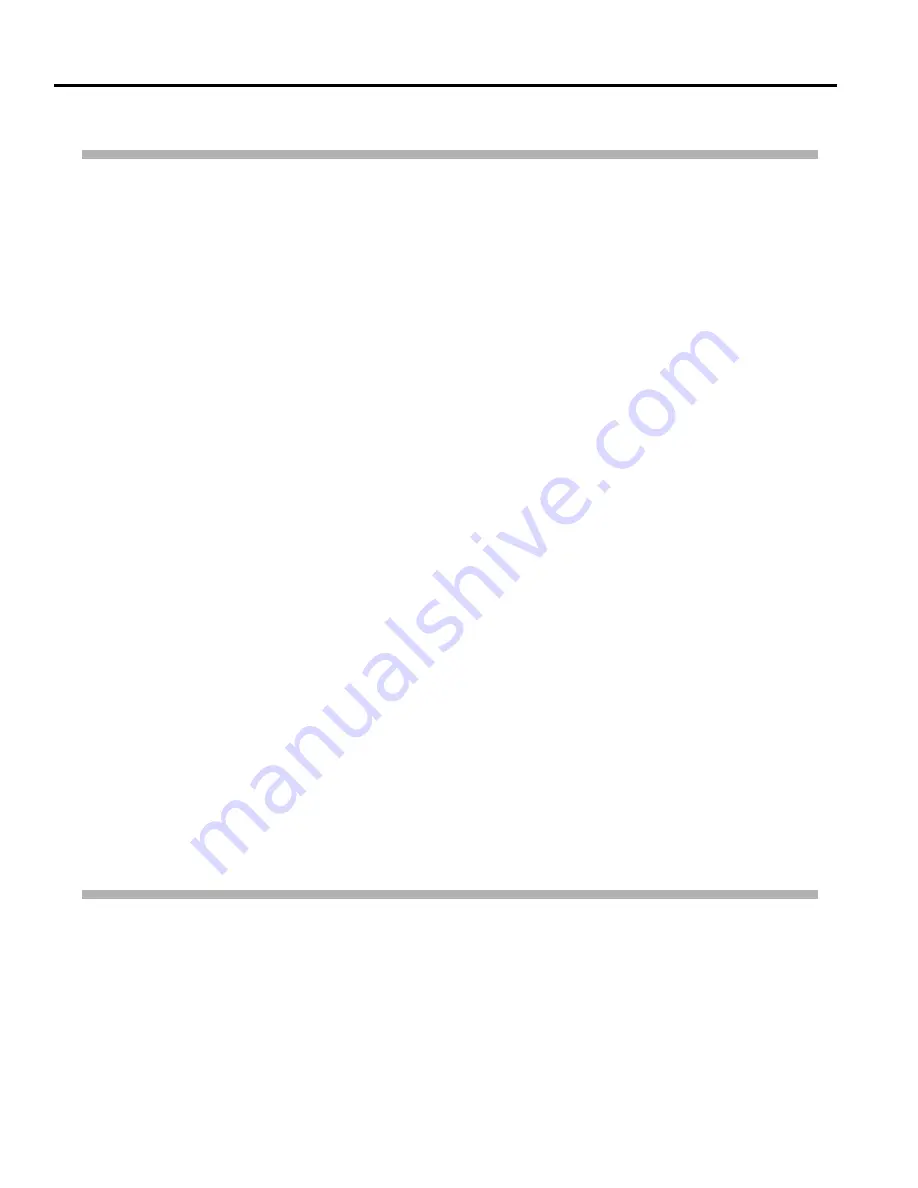
34
AT2000 XR Film Quality Troubleshooting
TROUBLESHOOTING
7.
FILM HAS SPOTS / APPEAR DIRTY
A. Confirm the following initial requirements for AT2000XR Automatic film processing. Make sure to use
the proper handling of pre-processed films - The films must not come in contact with any wet surface
(ie; hands, counter surface, etc...) and should be handled along edges.
1. Intensifying screens are not worn, outdateds and/or dirty.
2. Film used is designed for Automatic Processing
3. Confirm that a CLEANING FILM has been processed after the READY light illuminates. This done
at the daily start up, and every 2 hours of idle time.
4. Chemistry used is designed for roller transport processors.
5. Check the wash drain tube DOES NOT have a rubber washer.
6. Check the solution levels are at the proper height.
B. Check the TRANSPORT ASSEMBLIES for "Caked" deposits;
1. Deposits only on DEVELOPER TRANSPORT Rack - Silver and/or gray staining on gears
2. Developer chemistry is contaminated - Refer to AVOIDING CHEMISTRY CONTAMINATION
provided on page 37 to clean.
3. Deposits only on FIXER TRANSPORT Rack - Silver deposits present
4. Fixer chemistry is exhausted - Change the chemistry
5. Thoroughly clean the rack assembly per the MAINTENANCE requirements in the USER'S MANUAL.
6. Confirm the Replenishment Bottles did not run dry, if so then change the chemistry and reiterate -
Monitoring of levels in the bottle are necessary, and the chemistry level should never be below 1"
from the bottom of it's respective bottle.
7. Deposits on either FIXER TRANSPORT or WASH/DRY TRANSPORT Rack for any white staining
on Fixer Rack exit or Wash/Dry entry rollers
8. Check the baffles in the Wash/Dry rack, verify they are installed correctly. Refer to the detail view
of assembly in the Roller Transport Parts illustration (page 58). Note the inner baffle is installed
before the outer baffle.
C. Check the CHEMISTRY REPLENISHMENT level control and pumping rateby analyzing the chemistry
replenishment for insufficient amounts per the check sequence listed in TROUBLESHOOTING GUIDE
SECTION 1- REPLENISHER PUMP PROBLEMS provided on page 26.
D. Check the WASH WATER for inadequate, or no flow of water into wash tank by analyzing the wash
water for insufficient amounts per the check sequence listed in TROUBLESHOOTING GUIDE
SECTION 1 - WASH WATER PROBLEMS provided on page 28.
8.
FILM HAS "BRANCH-LIKE'~ ARTIFACTS / SMUDGES
A. Static electricity discharges onto the film and imposes an artifact - Reiterate safeguards;
1. Removal of films and film wrappers slowly from cassettes and boxes.
2. The room should have appropriate floor covering.
3. Increase the humidity level in the room.
Содержание A/T2000 XR
Страница 1: ...AUTOMATIC FILM PROCESSOR SERVICE MANUAL...
Страница 20: ...20 SYSTEM SCHEMATIC...
Страница 40: ...40 BASE ASSEMBLY TOP VIEW OVERHEAD VIEW DETAIL A BASE ASSEMBLY 45200...
Страница 42: ...42 BASE ASSEMBLY BOTTOM VIEW SINGLE FUSE CONFIGURATION 5A...
Страница 49: ...49 ROLLER TRANSPORTS WASH DRY TRANSPORT P N5510 DEVELOPER TRANSPORT P N45500 FIXER TRANSPORT P N 45505...