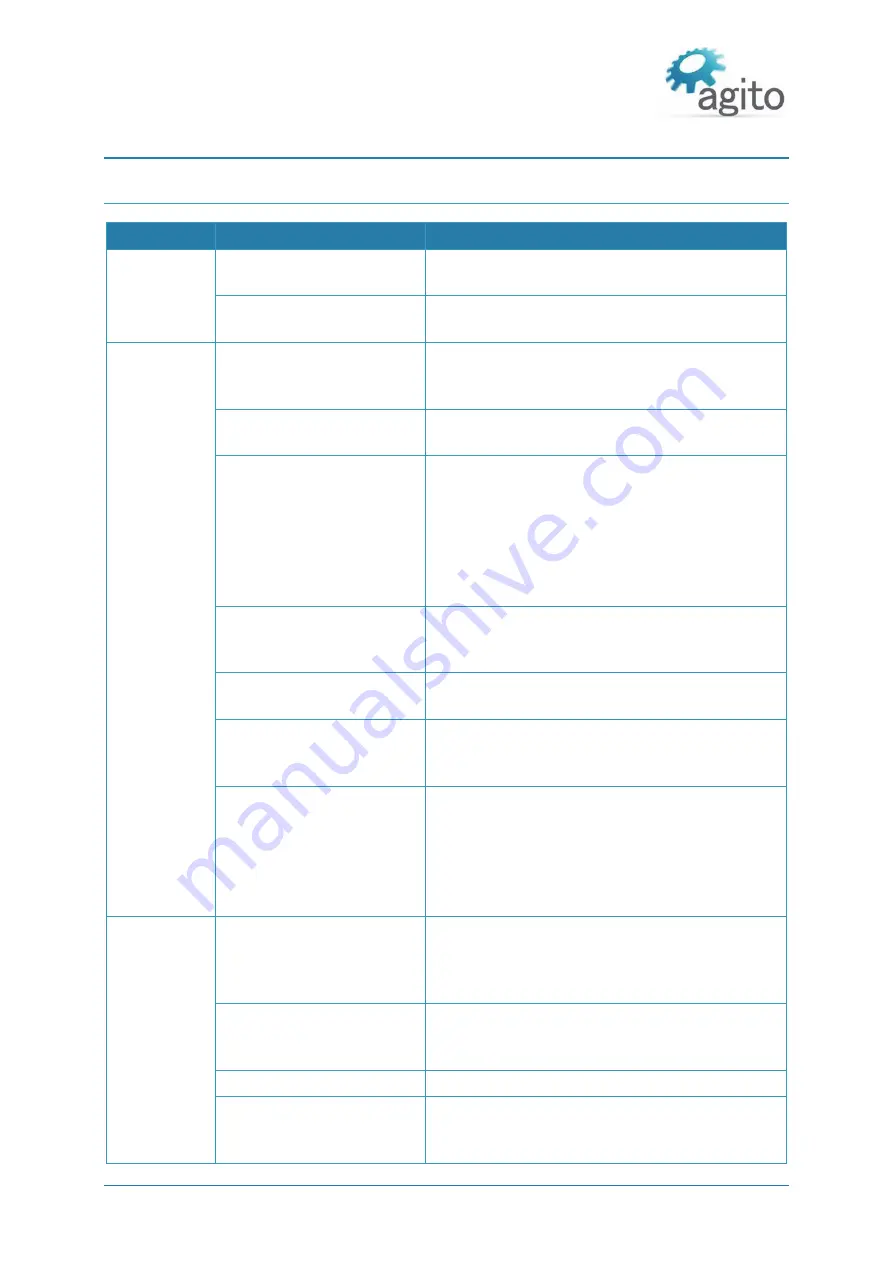
Troubleshooting
AGD155 Product Manual Rev.2.2
Page 56
5 Maintenance and Servicing
5.1 Troubleshooting
Condition
Potential Cause
Possible Resolution
Power is On
but no LED
light
Power connector is loose
Check power connector, measure power supply
voltage using a voltmeter.
Firmware is corrupted
Turn on DIP switch #2, power cycle, and download
firmware using Agito PCSuite.
Motor is
oscillating or
out of control
(free wheel)
The position feedback sensor
(encoder) is faulty or
disconnected
Check wiring.
Position feedback sensor is
configured in wrong direction
Go to Agito PCSuite’s CONFIG > FDBK page, toggle
the
Invert direction
setting.
Encoder signal is interfered
by EMI noise in the system,
resulting in lost counts or
incorrect position feedback
Verify if the encoder signal is drifting even when the
motor is physically locked or not moving. Check
electrical grounding, shielding and PE in the system
to ensure there are no ground-loop in the system.
Set EncFilt from Agito PCSuite’s CONFIG > FDBK
page to a frequency setting that is just above the
required motion speed.
Control loops’ gains are too
high
Go to Agito PCSuite’s Tune page, select CURR
and/or PIV page to reduce the gains to half. If the
situation improved, redo tuning for the axis.
Velocity or Acceleration
command is set too high
Reduce the acceleration, deceleration, smooth and
speed setting.
Noise introduced in
calculation of velocity from
position feedback
Add a software low pass filter from Agito PCSuite’s
TUNE > PIV, Velocity Filters tab.
Mechanical resonance.
Add a software low pass filter from Agito PCSuite’s
TUNE > PIV, Velocity Filters tab.
Do advanced auto tuning to allow Agito PCSuite
identify and apply a suitable filter. Perform TUNE >
IDEN and TUNE > DESI (Expert > Expert Tune mode
for best result).
Cannot
achieve the
required
speed
Acceleration and/or
deceleration and/or speed is
set too low, or smooth is set
too high.
Adjust acceleration, deceleration and smooth
settings.
Current and voltage limits are
set too low
Check current limits are according to motor’s
datasheet and maxPWM, under CONFIG->POW
page, is set to between 90% and 95%.
Improper control loops gains Re-tune the motor
The load inertia or friction is
too high for the motor
Check motor and driver sizing for this axis to ensure
the motor force, current and voltage of power
supply is sufficient to achieve the motion.