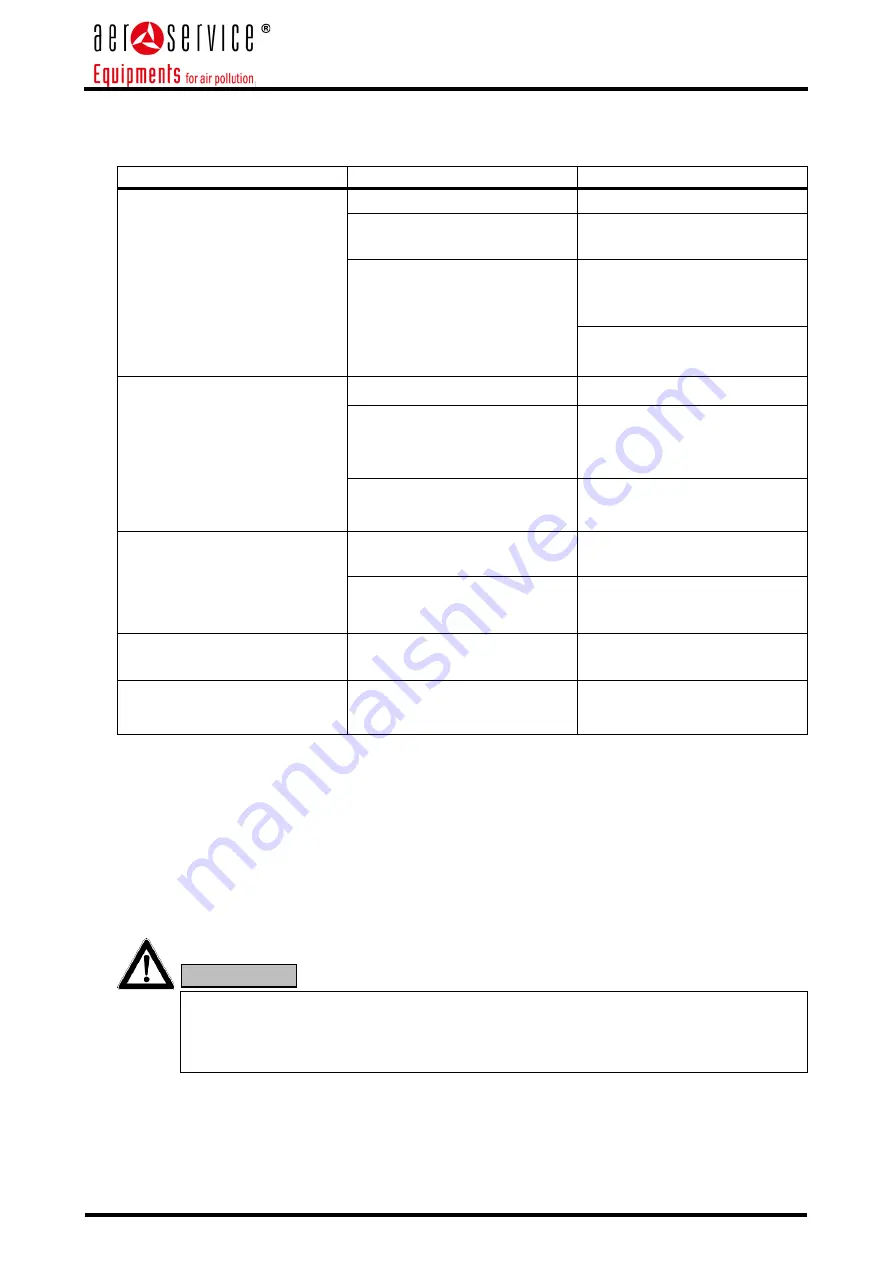
Instruction manual for use and maintenance - EN
Rev.: 0
–
aggiornato al 06/11/2020
| Con riserva di modifiche tecniche e salvo errori |
Pag.
22
di
39
7.5.
Troubleshooting
FAILURE
POSSIBLE CAUSE
ACTION REQUIRED
The unit does not turn on
No power supply
Contact an electrician
Pc board protection fuse is
blown
Replace the 5x20 3.15A fuse
The Start / Stop sensor is
connected but does not detect
any current
Ensure that the ground cable of
the welding unit is correctly
clamped on the filter units
Start welding, if you have not
yet
The extraction capacity is poor
Presence of dust in the air
expulsion grid
Filters are dirty
Replace filters
Wrong rotating direction of the
motor (three-phase 400V
version)
Consult an electrician to
reverse two phases in the CEE
plug
The extraction hose is blocked
Clean or replace the extraction
hose
Not all fumes are captured
Inclination of the welding gun is
wrong
Read ch. 6.3 of this manual
Bypass valve on the torch is
open
Close the bypass valve
The expulsion grid is dusty
Filter is ruined
Replace the cartridge filter
The differential switch of the
mains supply trips
The unit is provided with an
inverter with EMC filter
Install a differential switch
suited for an inverter
7.6.
Emergency measures
In the event of a fire in the unit or in its suction device, proceed as follows:
•
Disconnect the unit from the mains supply, removing the plug from the socket, if possible.
•
Try to extinguish the outbreak of fire with a standard powder extinguisher.
•
If necessary, contact the fire brigade.
Do not open the inspection doors of the unit.
Possibility of flare-ups!
In case of fire, do not touch the unit for any reason without suitable protective gloves.
Danger of burns!
WARNING