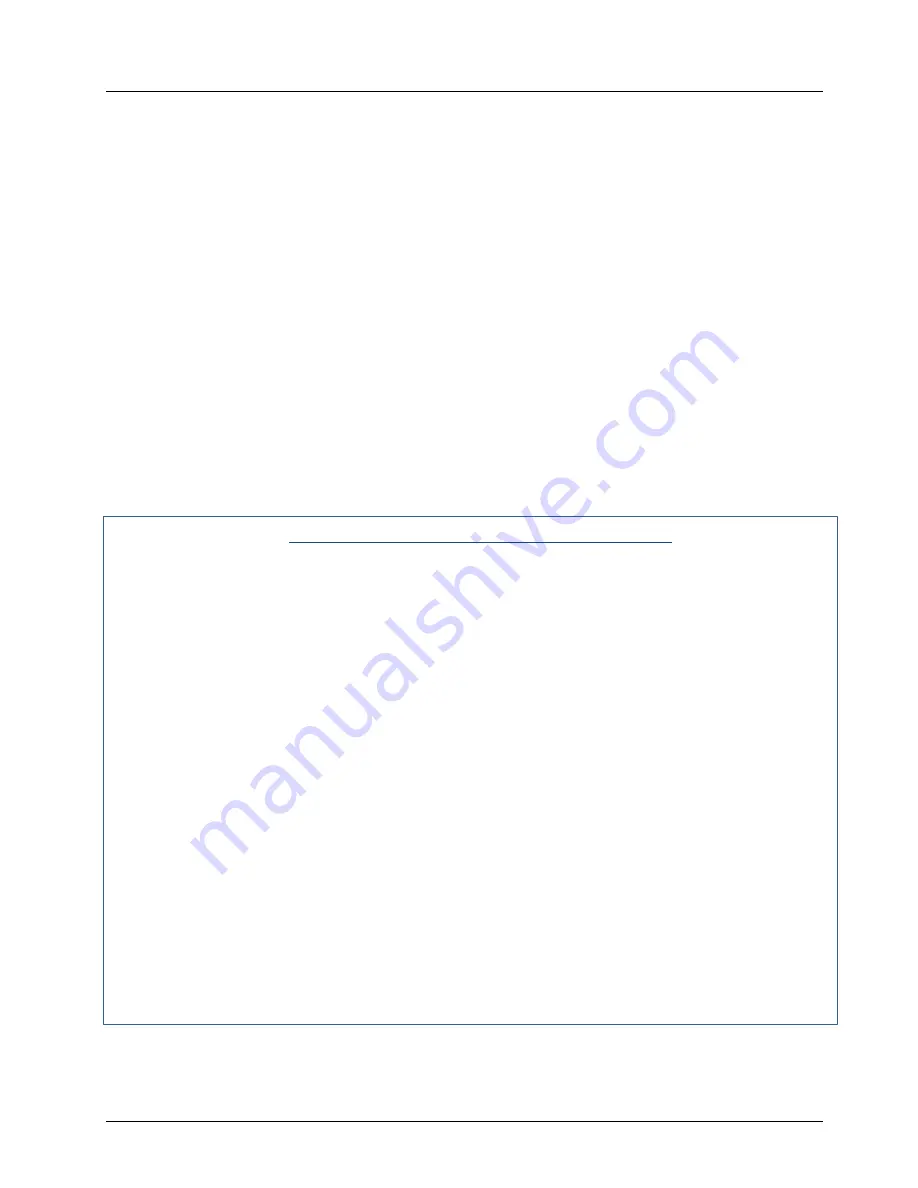
Innovation Water Heaters Installation, Operation & Maintenance Manual
CHAPTER 4 – INITIAL START-UP
OMM-0078_0M
AERCO International, Inc.
•
100 Oritani Dr.
•
Blauvelt, NY 10913
Page
57
of
216
GF-128
Phone: 800-526-0288
09/11/2015
4.3 NATURAL GAS COMBUSTION CALIBRATION
IMPORTANT
The instructions in this section do not apply to Innovation units being installed in
Korea. If you are installing the unit in Korea, please skip this section and instead
complete the instructions in Appendix J, sections J-1 and J-3.
IMPORTANT
The unit is shipped from the factory set up for either Natural Gas or Propane as
specified by the Style Number on the Sales Order.
Complete the instructions
below only if your unit has been set up to run on NATURAL GAS.
Innovation Water Heaters are combustion calibrated at the factory prior to shipping. However,
recalibration is necessary as part of initial start-up due to changes in the local altitude, gas BTU
(kW) content, gas supply piping and supply regulators. Start-Up & Registration Test Data sheets
are shipped with each unit. These sheets must be filled out and returned to AERCO for proper
Warranty Validation.
It is important to perform the calibration procedure as outlined below. This will keep
readjustments to a minimum and provide optimum performance.
NATURAL GAS Combustion Calibration
1.
Open the water supply and return valves to the unit and ensure that the system pumps are
running.
2.
Open the
NATURAL GAS
supply valve(s) to the unit.
3.
Set the control panel ON/OFF switch to the
OFF
position.
4.
Turn on external AC power to the unit.
5.
Enter the password
6817
to continue.
6.
Set the unit to the MANUAL mode by pressing the
AUTO/MAN
key. A flashing
MANUAL
VALVE POSITION
message will be displayed with the present position in %. Also, the
MANUAL
LED will light.
7.
Adjust the air/fuel valve position to
0%
by pressing the ▼ arrow key.
8.
Ensure that the leak detection ball valve downstream of the SSOV is open.
9.
Set the ON/OFF
switch to the
ON
position.
10.
Change the valve position to
28%
using the ▲ arrow key. The unit should begin its start
sequence and fire.
11.
Using the ▲ arrow key, increase the valve open position to
100%
and then allow the valve
position to reach 100%.
12.
With the valve position at 100%, insert the combustion analyzer probe into the 1/8” (3.18
mm) port at the rear of the exhaust manifold. Allow enough time for the combustion
analyzer to settle.