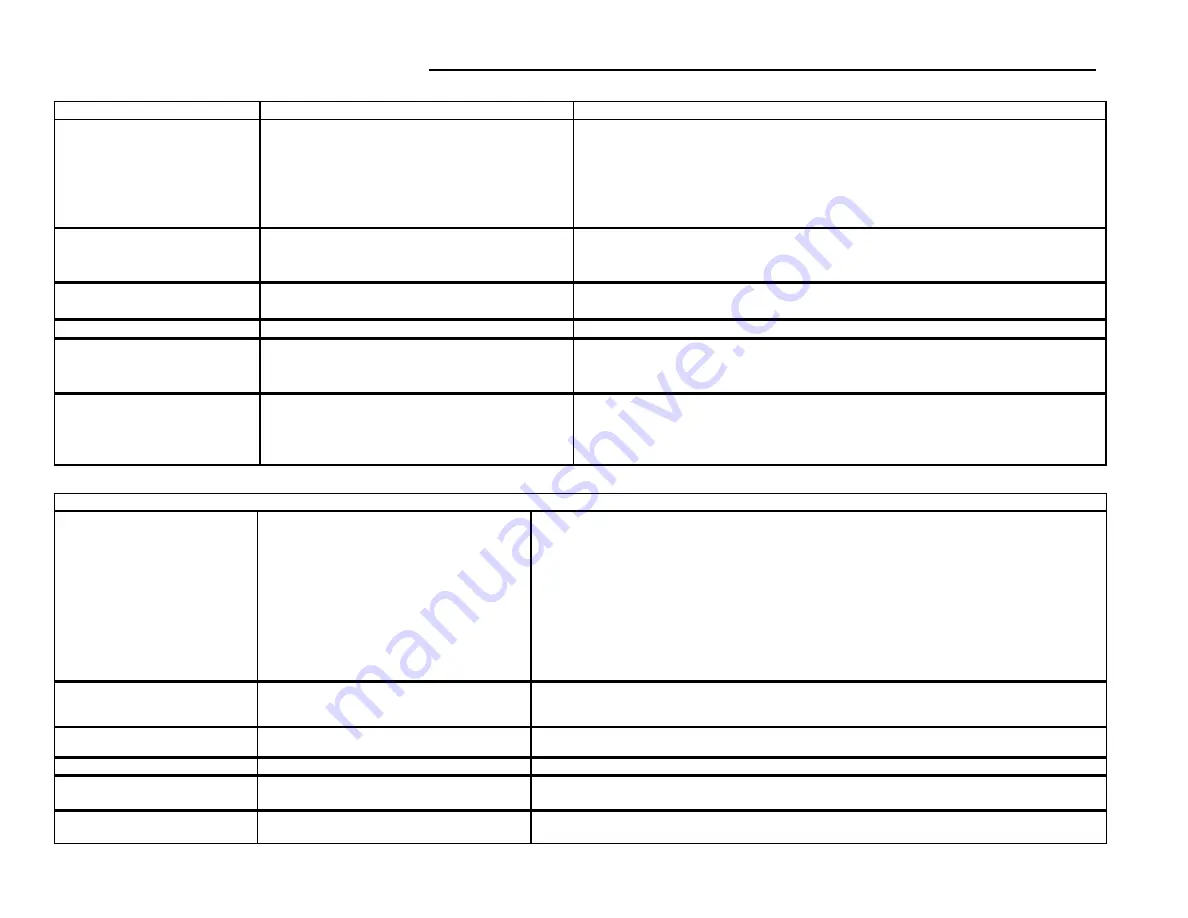
14
TROUBLE SHOOTING GUIDES CONTINUED
General Refrigeration Circuit Continued
SYMPTOM
POSSIBLE CAUSE
REMEDY
1. Refrigerant undercharge or leak in system.
1. Check subcooling and check for leaks.
2. Evaporator plugged with dirt or ice.
2. Check evaporator, airflow and filter.
3. Improperly adjusted or defective expansion valve.
3. Check superheat and adjust TXV, check bulb.
4. Defective compressor.
4. Check compressor for proper operation.
5. High discharge pressure.
5. See “high discharge pressure” above.
6. Airflow is too high.
6. Check external static pressure.
1. Airflow is too low.
1. Check evaporator coil, filter, check for closed dampers, grills, drive for loose parts, belts,
misalignment, check external static pressure.
2. Return air temperature too low.
2. Check entering air wet bulb conditions.
1. Refrigerant undercharge.
1. Adjust the charge by subcooling.
2. High discharge pressure.
2. See “high discharge pressure” above.
Q. Liquid line frosted or wet.
1. Restriction in liquid line.
1. Restriction upstream of point of frosting.
1. Insufficient evaporator air flow.
1. Check airflow, check drive for loose parts, belts, closed dampers.
2. Restriction in suction or liquid line.
2. Restriction upstream of point of frosting.
3. Malfunctioning or defective expansion valve.
3. Check bulb of TXV.
1. Improper wiring.
1. Check wiring diagrams.
2. Defective motor.
2. Check motor and controller.
3. Defective thermostat or control circuit.
3. Check control circuit.
4. Motor off on overload protector.
4. Allow motor to cool, check amperage.
S. Blower motor not running.
N. Supply air temperature too high.
O. Supply air temperature
P. Liquid line too hot.
R. Suction line frosting.
Varispeed™ Condenser Head Pressure Control
SYMPTOM
POSSIBLE CAUSE
REMEDY
1. Input pressure is below operating range.
1. No problem, normal operation.
2. No 24 volt control voltage
2. Check for 24 V AC at control.
3. No input pressure to control.
3. Check alignment of capillary fitting. Schrader valve depressor must depress Schrader valve enough to allow
pressure into capillary.
4. Bad fan motor.
4. Disconnect power. Place a jumper from L1 to M1 and connect power. If fan does not start, motor is bad and
should be replaced.
5. Pressure transducer problem.
5. Disconnect 6 pin connector from right side of control. Place a jumper wire between third pin from the top and
bottom pin on the control (not the cable). If fan goes to full speed, check for input pressure. If it has been
determined there is adequate pressure, the transducer is bad and the control must be replaced.
B. Fan stops when pressure reaches
the high end of the operating range.
1. Control is not wired correctly.
1. See wiring diagrams.
C. No fan modulation (On-Off
Operation)
1. Control is not wired correctly.
1. See wiring diagrams.
D. Fan starts at full speed.
1. Control is not wired correctly.
1. See wiring diagrams.
1. Control is not wired correctly.
1. Check to see if control voltage (24 V AC) is on same phase as motor.
2. Dirty or blocked condenser coil.
2. Clean condenser coil.
F. Fan motor is cycling on thermal over 1. Dirty or blocked condenser coil.
1. Clean condenser coil.
2. Wrong motor for fan speed control application.
2. Replace with motor approved for fan speed control application.
A. No fan operation.
E. Erratic fan operation.
Содержание B
Страница 19: ...19 ...