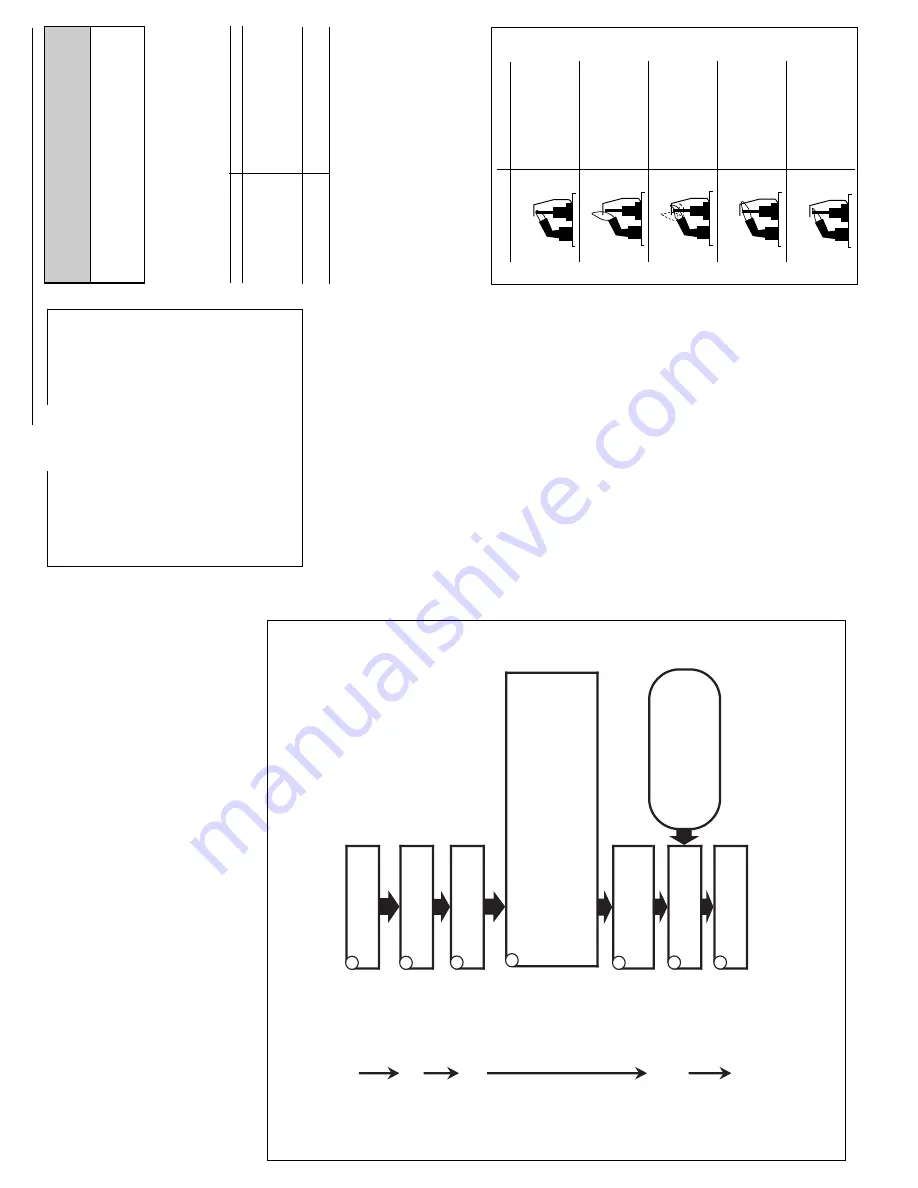
WARNING
When performing the following steps, do not touch
stripped end of jumper or SPARK terminal. The
ignition circuit generates over 10,000 volts and
electrical shock can result.
■
Energize the module and immediately touch one end of
the jumper firmly to the GND terminal on the module. Move
the free end of the jumper slowly toward the SPARK
terminal until a spark is established.
■
Pull the jumper slowly away from the terminal and note the
length of the gap when sparking stops. Check table below
.
ARC LENGTH
ACTION
N
o
a
rc
o
r a
rc
l
e
s
s
Check
external
fuse,
if
provided.
than 1/8 inch [3 mm]
Verify power at module input
terminal.
Replace module if fuse and
power okay.
Arc 1/8 inch [3 mm]
Voltage output is okay.
or longer.
STEP 4: Check pilot and main burner lightoff.
■
Set the thermostat to call for heat.
■
Watch the pilot burner during the ignition sequence. See
if:
•
Ignition spark continues after the pilot is lit.
•
The pilot lights and the spark stops, but main burner
does not light.
•
S8610B,H; S8670D only:
The pilot lights, the spark stops
and main burner lights, but the system shuts down.
■
If so, ensure adequate flame current as follows.
•
Turn off furnace at circuit breaker or fuse box.
•
Clean the flame rod with emery cloth.
TROUBLESHOOTING
IMPORTANT
1.
The following service procedures are provided as
a general guide. Follow appliance manufacturer’s
service instructions if available.
2.
On lockout and retry models, meter readings
between gas control and ignition module must be
taken within the trial for ignition period. Once the
ignition module shuts off, lockout models must be
reset by setting the thermostat down for at least
one minute before continuing. On retry models,
wait for retry or reset at the thermostat.
3.
If any component does not function properly,
make sure it is correctly installed and wired before
replacing it.
4.
The ignition module cannot be repaired. If it mal-
functions, it must be replaced.
5.
Only trained, experienced service technicians
should service intermittent pilot systems.
Perform the checkout on page 12 as the first step in
troubleshooting. Then check the appropriate troubleshoot-
ing guide (Fig. 15 or 16) and the schematic diagram (Fig .
17 or 18) to pinpoint the cause of the problem. If trou-
bleshooting indicates an ignition problem, see Ignition
System Checks below to isolate and correct the problem.
Following troubleshooting, perform the checkout proce-
dure (page 12) again to be sure system is operating
normally.
IGNITION SYSTEM CHECKS
STEP 1: Check ignition cable.
Make sure:
■
Ignition cable does not run in contact with any metal
surfaces.
■
Ignition cable is no more than 36 inches [0.9 meters]
long.
■
Connections to the ignition module and to the igniter or
igniter-sensor are clean and tight.
■
Ignition cable provides good electrical continuity.
STEP 2: Check ignition system grounding.
Nuisance shut-
downs are often caused by a poor or erratic ground.
■
A common ground, usually supplied by the pilot burner
bracket, is required for the module and the pilot burner/
igniter-sensor.
•
Check for good metal-to-metal contact between the
pilot burner bracket and the main burner.
•
Check the ground lead from the GND(BURNER)
terminal on the module to the pilot burner. Make sure
connections are clean and tight. If the wire is dam-
aged or deteriorated, replace it with No. 14 through
No.18 gauge, moisture-resistant, thermoplastic insu-
lated wire with 105
°
C [221
°
F] minimum rating.
—
Check the ceramic flame rod insulator for cracks
or evidence of exposure to extreme heat, which
can permit leakage to ground. Replace pilot burner/
igniter-sensor and provide shield if necessary.
—
If flame rod or bracket are bent out of position,
restore to correct position.
STEP 3: Check spark ignition circuit.
You will need a short
jumper wire made from ignition cable or other heavily
insulated wire
.
■
Close the manual gas valve.
■
Disconnect the ignition cable at the SPARK terminal on
the module.
16
Fig. 14—Examples of unsatisfactory pilot flames.
LAZY YELLOW FLAME
WAVING BLUE FLAME
NOISY LIFTING BLOWING FLAME
HARD SHARP FLAME
SMALL BLUE FLAME
CHECK FOR LACK OF GAS FROM:
• CLOGGED ORIFICE FILTER
• CLOGGED PILOT FILTER
• LOW GAS SUPPLY PRESSURE
• PILOT ADJUSTMENT AT MINIMUM
CHECK FOR LACK OF AIR FROM:
• DIRTY ORIFICE
• DIRTY LINT SCREEN, IF USED
• DIRTY PRIMARY AIR OPENING,
IF THERE IS ONE
• PILOT ADJUSTMENT AT MINIMUM
CHECK FOR:
• EXCESSIVE DRAFT AT PILOT
LOCATION
• RECIRCULATING PRODUCTS
OF COMBUSTION
CHECK FOR:
• HIGH GAS PRESSURE
THIS FLAME IS CHARACTERISTIC
OF MANUFACTURED GAS
CHECK FOR:
• HIGH GAS PRESSURE
• ORIFICE TOO SMALL
M2233A
APPEARANCE
CAUSE
TRIAL FOR IGNITION
Pilot Ignition
Following prepurge timing (S8670), or on the call for heat
(S8610), the module energizes the first main valve opera-
tor. The first main valve opens, which allows gas to flow to
the pilot burner. At the same time, the electronic spark
generator in the module produces an over 10,000 volt spark
pulse output. The voltage generates a spark at the igniter
(S8610A,B) or igniter-sensor (S8610F,H; S8670) that lights
the pilot.
If the pilot does not light, or the pilot flame current is not
at least 1.0
μ
A and steady, the module will not energize the
second (main) valve and the main burner will not light.
S8610A,F will continue to spark as long as the thermostat
calls for heat, or until the pilot lights.
Safety Lockout (S8610B,H; S8670D)
These modules provide 100 percent shutoff and safety
lockout. A timer in these models starts timing the moment
the trial for ignition starts. Ignition spark continues only until
the timed trial for ignition period ends. Then the module
goes into safety lockout. Lockout de-energizes the first
main valve operator and closes the first main (pilot) valve in
the gas control, stopping pilot gas flow. The control system
must be reset by setting the thermostat below room tem-
perature for one minute or by turning off power to the
module for one minute.
MAIN BURNER OPERATION
When the pilot flame is established, a flame rectification
circuit is completed between the sensor and burner ground.
The flame sensing circuit in the module detects the flame
current, shuts off the spark generator, and energizes the
second main valve operator. The second main valve opens
and gas flows to the main burner, where it is ignited by the
pilot burner. On lockout models, the flame current also
holds the safety lockout timer in the reset (normal) operat-
ing condition.
When the call for heat ends, both valve operators are de-
energized, and both valves in the gas control close.
Fig. 13—S8670 normal operating sequence.
69-0523
15
M550
START
THERMOSTAT
PREPURGE
SPARK GENERATOR POWERED
PILOT BURNER OPERATION
OR
Pilot burner lights.
S8670 senses flame current.
Pilot burner does not light.
After 15 or 90 sec , system
locks out; must be manually reset.
Lockout timing is
stamped on module.
a
a
STAGE 1
PREPURGE
STAGE 2
TRIAL FOR IGNITION
STAGE 3
MAIN BURNER
OPERATION
END
FLAME CURRENT SENSED
MAIN BURNER OPERATION
Module monitors pilot flame
current.
THERMOSTAT SATISFIED
Valves close, pilot and main
burners are off.
POWER INTERRUPTION
System shuts off, restarts when power is
restored.
PILOT FLAME FAILURE
Main valve closes.
S8670 starts trial for ignition.
Spark generator off.
Second valve operator (main)
opens.
•
•
1
2
3
4
5
6
7
CALLS FOR HEAT
Combustion air blower starts.
First valve (pilot) operator opens.