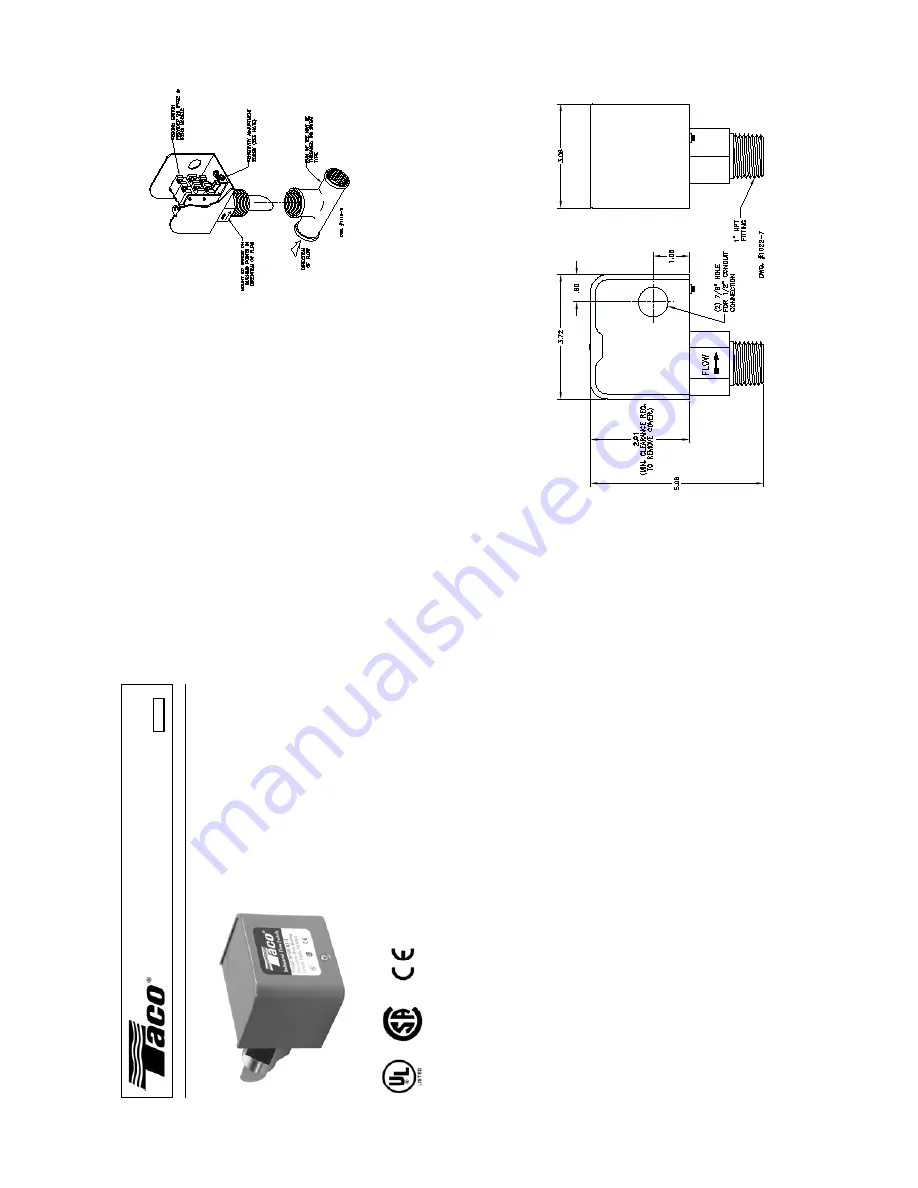
Listings/Approvals:
•
UL Guide (NKPZ) for industrial control
equipment per UL Standard 508 Industrial
Control Equipment
•
UL Guide (MFHX) for heating/cooling ap-
pliance switch per UL Standard 353 Limit
Controls
•
CSA Class (321106) for industrial control
equipment per CSA Standard C22.2 No.
14-M Industrial Control Equipment
Maximum Service Pressure:
250 PSI
Enclosure:
NEMA Type 1 (For indoor use only)
Formed sheet metal with powdercoat finish.
Not for use in hazardous locations.
Contacts:
IFS01: One SPDT (Form C) switch
IFS02: Two sets of SPDT (Form C) switches
to provide versatility in wiring two separate
circuits.
15 Amps at 125/250VAC
.5 Amps at 125VDC
.25 Amps at 250VDC
Motor Ratings :
120VAC
240VAC
Horsepower :
1/8
1/4
AC F.L.A. :
3.8
2.9
AC L.R.A. :
22.8
17.4
Pilot Duty Rating :
125 VA
120/240
VAC
IFSH1/2 Contacts:
IFSH1: One SPDT (Form C) switch
IFSH2: Two sets of SPDT (Form C) switches
to provide versatility in wiring two separate
circuits.
22 Amps at 125/250VAC
Motor Ratings :
120VAC
240VAC
Horsepower :
1/2
1
AC F.L.A. :
9.8
8.0
AC L.R.A. :
58.8
48.0
Pilot Duty Rating :
125 VA
120/240
VAC
Ambient Temperature Range:
32°F/176°F (0°C/80°C)
Media Temperature Range:
32°F/250°F (0°C/121°C)
Pipe Connections:
1" NPT Brass on models IFSxx
B
1" NPT 316 Stainless Steel on models
IFSxx
S
Conduit Entrance:
Two openings for 1/2" conduit
Usage:
For pipe sizes 1" - 8"
Caution:
This device is not intended for applica-
tions in explosive environments.
Note:
IFSW Series available with NEMA 4 enclo-
sure for outdoor use. (See bulletins
#102-026 & #102-027 or Catalog 100-8.2).
GENERAL
The Model IFS is a flow switch used in liquid
flow lines carrying water or any fluid not harmful
to brass, stainless steel, EPDM or fluorosilicone,
and not classified as a hazardous fluid.
This switch can serve as a way to start and stop
electrically operated equipment when a flow or no
flow condition occurs in a variety of applications.
This device is designed for use only as an operat-
ing control. Where an operating control failure
would result in personal injury and/or loss of prop-
erty, it is the responsibility of the installer to add
devices (safety, limit controls) that protect against,
or systems (alarm, supervisory systems) that warn
of control failure.
Instruction Sheet
Industrial Flow Switch
SUPERCEDES: 102-122 DATED January 1, 2002
# 5401110-REV E
EFFECTIVE: March 17, 2004
102-022
(IFS01 &
IFS02 ONLY)
MOUNTING AND INSTALLATION
The Model IFS may be mounted in a horizontal
pipe line or a vertical pipe line with upward liquid
flow. It is not recommended for installations
where flow is downward. When mounted in a
horizontal pipe line the switch will trip at a lower
flow rate than shown in Fig. 7.
Mount the device in a section of pipe where there
is a straight run of at least 5 pipe diameters on
each side of the flow switch. Do not locate adja-
cent to valves, elbows or orifices. The switch
should be mounted so the terminals or wire leads
are easily accessible for wiring.
IFS models with flexible paddles are furnished
with 4 paddles. Rigid paddle models are fur-
nished with 2 paddles. For pipe sizes 1", 2", 3" or
6", use the paddles provided. Intermediate sizes
may be trimmed from the appropriate paddle
using the paddle template in Fig. 5. The paddle
must not touch the inside of the pipe or bind in
any way. Paddles smaller than the actual pipe
size should be used for added support and higher
sensitivity, see Fig. 3. The paddles must be prop-
erly attached and the screw that holds the paddle
must be securely tightened.
For a 1" pipe application mount in a standard 1" x
1" x 1" tee. Use a reducing tee for larger sizes of
pipe to keep flow switch close to pipe and provide
adequate paddle length in the flow stream.
Example: Use a 2" x 2" x 1" tee for 2" pipe. A
weldolet may also be used. Screw the device into
the tee fitting as shown in Fig. 4. The flat of the
paddle must be at a right angle to the flow. The
arrow on the side of the bushing must point in the
direction of flow, see Fig. 1.
FIG. 1
Sensitivity Adjustment Note:
Turn screw clockwise to increase the flow rate
required to activate the switch.
Turn screw counter-clockwise to decrease the
flow rate required to activate the switch.
FIG. 2