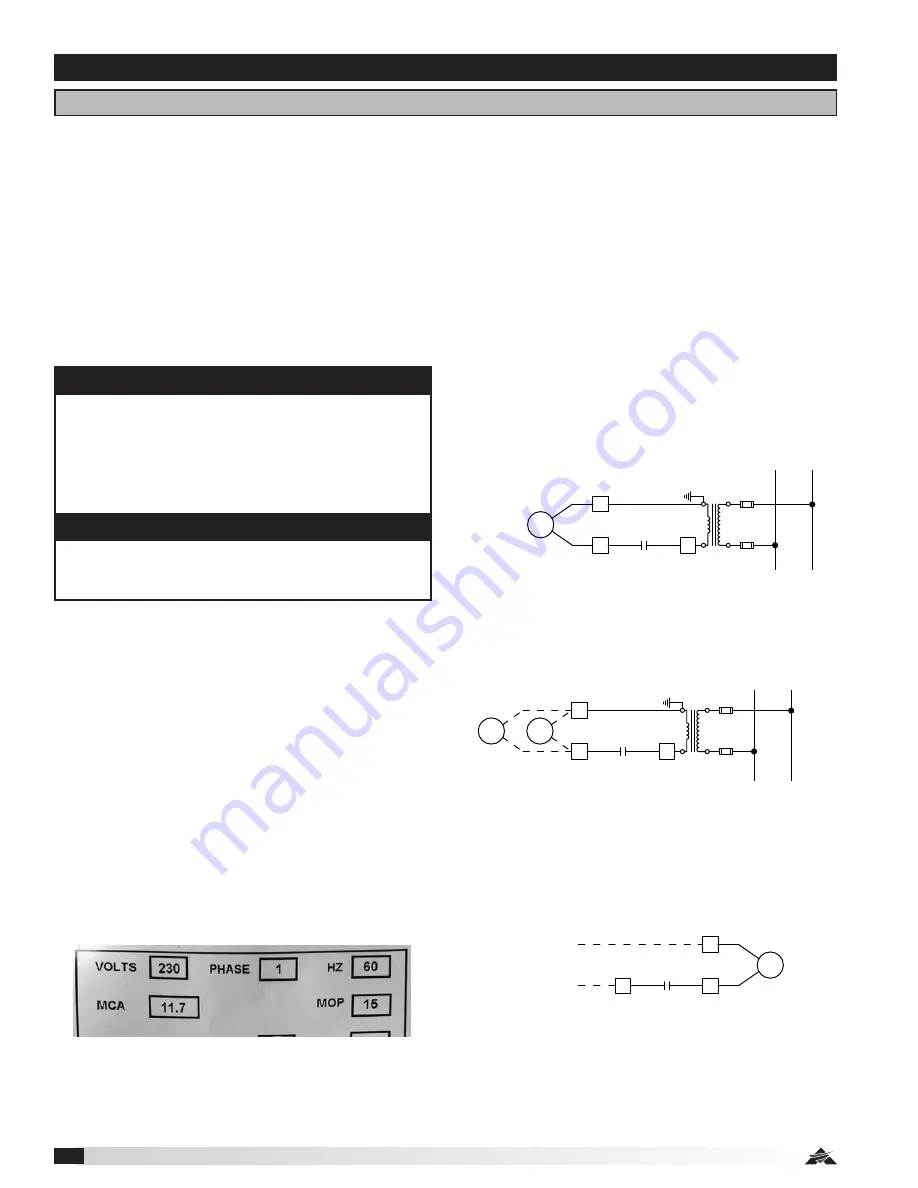
Direct Gas Make-Up Air
12
1. Determine the Size of the Main Power Lines
The unit’s nameplate states the voltage and the unit’s
MCA. The main power lines to the unit must be sized
accordingly. The nameplate is located on the outside of
the unit on the control panel side.
2. Provide the Opening(s) for the Electrical
Connections
Electrical openings vary by unit size and arrangement
and are field-supplied.
3. Connect the Main Power
Connect the main power lines to the disconnect switch
and main grounding lug(s). Torque connections to
disconnect according manufacturer specifications.
4. Wire the Optional Convenience Outlet
The convenience outlet requires a separate 115V power
supply circuit. The circuit must include short circuit
protection supplied by others.
5. Wire Evaporative Cooling Pumps
Reference the unit wiring diagram attached to the
inside of the unit control center door. Locate the “Evap
Pump(s)” on the wiring diagram. If they are connected
with solid lines indicating factory wiring, no field wiring
is required.
If the evaporative pump(s) are shown with dashed lines
indicating field wiring, wire the pumps to the terminals
indicated in the unit control center.
Larger units may require a separate 115 VAC power
source. If this is necessary, it will be indicated on the
wiring diagram. Wire a separate 115 VAC power supply
as indicated on the wiring diagram to power the pumps.
Installation
Line Voltage Electrical Wiring
Before connecting power to the unit, read and
understand the following instructions and wiring
diagrams. Complete wiring diagrams are attached on
the inside of the control center door(s).
All wiring must be done in accordance with the latest
edition of the National Electrical Code NFPA 70 and any
local codes that may apply. In Canada, wiring must be
done in accordance with the Canadian Electrical Code.
The equipment must be properly grounded. Any
wiring running through the unit in the airstream must
be protected by metal conduit, metal clad cable or
raceways.
Manufacturer’s standard control voltage is 24 VAC.
Control wire resistance must not exceed 0.75 ohms
(approximately 285 feet total (86.9 m) length for
14 gauge wire; 455 feet (138.7 m) total length for
12 gauge wire). If the resistance exceeds 0.75 ohms,
an industrial-style relay must be wired in place of the
remote switch. The relay must be rated for at least
5 amps and have a 24 VAC coil. Failure to comply with
these guidelines may cause motor starters to chatter or
not pull in, resulting in contactor failures and/or motor
failures.
LEGEND
GREENHECK
Building Value in Air.
CAUTION
UNIT SHALL BE GROUNDED IN ACCORDANCE WITH N.E.C.
POWER MUST BE OFF WHILE SERVICING.
NOTES
USE COPPER CONDUCTORS ONLY
60° C FOR TERMINALS RATED LESS THAN 100 AMPS.
75° C FOR TERMINALS RATED 100 AMPS OR MORE.
FIELD CONTROL WIRING RESISTANCE SHOULD
NOT EXCEED 0.75 OHM.
FIELD WIRED
FACTORY SUPPLIED AND WIRED
WIRE COLOR CODE
Wiring Diagram Code:
BK
BLACK
BL
BLUE
BR
BROWN
GY
GRAY
LT BL LIGHT BLUE
O
ORANGE
PK
PINK
PR
PURPLE
R
RED
W
WHITE
Y
YELLOW
GD11N601A001A00NM16
Wiring Template: M16
AMP AMPLIFIER
DS1 MAIN DISCONNECT SWITCH
FSC FIRE SYSTEM CONTACT
FSG FLAME SAFE GUARD
FU# FUSE
M#
MOTOR
MOD MODULATING VALVE
OL# MOTOR OVERLOAD
P#
EVAP PUMP
PS2 AIR PROVING SWITCH
RC
COOL RELAY
RF
SUPPLY FAN RELAY
RH
HEAT RELAY
S2
FAN SWITCH
S4
HEAT AND COOL SWITCH
ST# MOTOR STARTER
TR# TRANSFORMER
TS2 DISCHARGE AIR SENSOR
V2
MAIN VALVE
L3
L2
L1
DS1
S4
SUPPLY FAN
MOTOR
ST1 O.L.
G
96
95
ST1 O.L.
OFF
ST1
A2
A1
SUPPLY FAN
14
11
RF
PINK
M1
PINK
BROWN
RF
A2
A1
SUPPLY FAN RELAY
21
RF
LT. BLUE
Y1
LT. BLUE
A2
A1
COOLING
24
RED
RC
GROUND
TO UNIT
MAIN POWER
460V
S2 FSC
24V
TR1
C
R
BLU
E
WH
ITE
75 VA
111
112
T3
T2
T1
(24V)
VALVE
FSG
SPARK
21
SENSE
SENSOR
SPARK
TR6
V2
37
39
38
ORANGE
22
23
11
RH
14
RED
RED
HLC1
24
TH/24V
PS2
PS2
NC
C
C
NO
27
1
MOD
5
6
AMP
7
8
TS2
3
4
1
2
10 SEC
DISCHARGE STAT.
BLAC
K
WH
ITE
BLU
E
BLU
E
INT
1
2
TEMP RANGE
55-90° F
BLUE
YELLOW
30 VA
24 VAC
WHITE
ORANGE
13
ST1
W1
RED
RH
A2
A1
POST HEAT
14
40VA
22
21
24V
R
R
EVAP PUMP
P1
RED
BLACK
RED
250VA
TR3
FU7
101
116
11
RC
14
115V
102
WHITE
BLACK
BLACK
TR5
DIRECT GAS CONTROL
O
BL
GND
GND
(BURNER)
L1
T1
L2
T2
L3
T3
4
PINK
2A,600V
CLASS
CC
Evap Pump Factory Wiring Example
Refer to wiring diagram for unit specific wiring
LEGEND
GREENHECK
Building Value in Air.
CAUTION
UNIT SHALL BE GROUNDED IN ACCORDANCE WITH N.E.C.
POWER MUST BE OFF WHILE SERVICING.
NOTES
USE COPPER CONDUCTORS ONLY
60° C FOR TERMINALS RATED LESS THAN 100 AMPS.
75° C FOR TERMINALS RATED 100 AMPS OR MORE.
FIELD CONTROL WIRING RESISTANCE SHOULD
NOT EXCEED 0.75 OHM.
FIELD WIRED
FACTORY SUPPLIED AND WIRED
WIRE COLOR CODE
Wiring Diagram Code:
BK
BLACK
BL
BLUE
BR
BROWN
GY
GRAY
LT BL LIGHT BLUE
O
ORANGE
PK
PINK
PR
PURPLE
R
RED
W
WHITE
Y
YELLOW
Wiring Template: M16
AMP AMPLIFIER
DS1 MAIN DISCONNECT SWITCH
FSC FIRE SYSTEM CONTACT
FSG FLAME SAFE GUARD
FU# FUSE
HLC HIGH LIMIT CONTROL
M#
MOTOR
MOD MODULATING VALVE
OL# MOTOR OVERLOAD
P#
EVAP PUMP
PS2 AIR PROVING SWITCH
RC
COOL RELAY
RF
SUPPLY FAN RELAY
RH
HEAT RELAY
S2
FAN SWITCH
S4
HEAT AND COOL SWITCH
ST# MOTOR STARTER
TR# TRANSFORMER
TS2 DISCHARGE AIR SENSOR
V2
MAIN VALVE
L3
L2
L1
DS1
S4
SUPPLY FAN
MOTOR
ST1 O.L.
G
96
95
ST1 O.L.
OFF
ST1
A2
A1
SUPPLY FAN
14
11
RF
PINK
M1
PINK
BROWN
RF
A2
A1
SUPPLY FAN RELAY
21
RF
LT. BLUE
Y1
LT. BLUE
A2
A1
COOLING
24
RED
RC
GROUND
TO UNIT
MAIN POWER
460V
S2 FSC
24V
TR1
C
R
BLU
E
WH
ITE
75 VA
111
112
T3
T2
T1
(24V)
VALVE
FSG
SPARK
21
SENSE
SENSOR
SPARK
TR6
V2
37
39
38
ORANGE
22
23
11
RH
14
RED
RED
HLC1
24
TH/24V
PS2
PS2
NC
C
C
NO
27
1
MOD
5
6
AMP
7
8
TS2
3
4
1
2
10 SEC
DISCHARGE STAT.
BLAC
K
WH
ITE
BLU
E
BLU
E
INT
1
2
TEMP RANGE
55-90° F
BLUE
YELLOW
30 VA
24 VAC
WHITE
ORANGE
13
ST1
W1
RED
RH
A2
A1
POST HEAT
14
40VA
22
21
24V
R
R
EVAP PUMPS
P2
P1
RED
BLACK
RED
500VA
FIELD CONNECTED
NETURAL
HOT
TR3
FU7
101
116
11
RC
14
115V
102
WHITE
BLACK
BLACK
TR5
DIRECT GAS CONTROL
O
BL
GND
GND
(BURNER)
L1
T1
L2
T2
L3
T3
4
PINK
2A,600V
CLASS
CC
DOC NUMBER: ----
REV: ----
GD11N601A001L00NM16
Evap Pump Field Wiring Example
Refer to wiring diagram for unit specific wiring
LEGEND
GREENHECK
Building Value in Air.
CAUTION
UNIT SHALL BE GROUNDED IN ACCORDANCE WITH N.E.C.
POWER MUST BE OFF WHILE SERVICING.
NOTES
USE COPPER CONDUCTORS ONLY
60° C FOR TERMINALS RATED LESS THAN 100 AMPS.
75° C FOR TERMINALS RATED 100 AMPS OR MORE.
FIELD CONTROL WIRING RESISTANCE SHOULD
NOT EXCEED 0.75 OHM.
FIELD WIRED
FACTORY SUPPLIED AND WIRED
WIRE COLOR CODE
Wiring Diagram Code:
BK
BLACK
BL
BLUE
BR
BROWN
GY
GRAY
LT BL LIGHT BLUE
O
ORANGE
PK
PINK
PR
PURPLE
R
RED
W
WHITE
Y
YELLOW
Wiring Template: M16
AMP AMPLIFIER
DS1 MAIN DISCONNECT SWITCH
FSC FIRE SYSTEM CONTACT
FSG FLAME SAFE GUARD
FU# FUSE
HLC HIGH LIMIT CONTROL
M#
MOTOR
MOD MODULATING VALVE
OL# MOTOR OVERLOAD
P#
EVAP PUMP
PS2 AIR PROVING SWITCH
RC
COOL RELAY
RF
SUPPLY FAN RELAY
RH
HEAT RELAY
S2
FAN SWITCH
S4
HEAT AND COOL SWITCH
ST# MOTOR STARTER
TR# TRANSFORMER
TS2 DISCHARGE AIR SENSOR
V2
MAIN VALVE
L3
L2
L1
DS1
S4
SUPPLY FAN
MOTOR
ST1 O.L.
G
96
95
ST1 O.L.
OFF
ST1
A2
A1
SUPPLY FAN
14
11
RF
PINK
M1
PINK
BROWN
RF
A2
A1
SUPPLY FAN RELAY
21
RF
LT. BLUE
Y1
LT. BLUE
A2
A1
COOLING
24
RED
GROUND
TO UNIT
MAIN POWER
460V
S2 FSC
24V
TR1
C
R
BLU
E
WH
ITE
75 VA
111
112
T3
T2
T1
(24V)
VALVE
FSG
SPARK
21
SENSE
SENSOR
SPARK
TR6
V2
37
39
38
ORANGE
22
23
11
RH
14
RED
RED
HLC1
24
TH/24V
PS2
PS2
NC
C
C
NO
27
1
MOD
5
6
AMP
7
8
TS2
3
4
1
2
10 SEC
DISCHARGE STAT.
BLAC
K
WH
ITE
BLU
E
BLU
E
INT
1
2
TEMP RANGE
55-90° F
BLUE
YELLOW
30 VA
24 VAC
WHITE
ORANGE
13
ST1
W1
RED
RH
A2
A1
POST HEAT
14
40VA
22
21
24V
R
R
RED
BLACK
RED
EVAP PUMP(S)
P1
FIELD CONNECTED
TR5
(NEUTRAL)
(115 VAC BY OTHERS)
EVAP PUMP(S) POWER
131
116
11
RC
14
132
BLACK
BLACK
(HOT)
RC
DIRECT GAS CONTROL
O
BL
GND
GND
(BURNER)
L1
T1
L2
T2
L3
T3
4
PINK
DOC NUMBER: ----
REV: ----
GD11N601A001C00NM16
Separate Power Wiring Example
Refer to wiring diagram for unit specific wiring
CAUTION
If replacement wire is required, it must have a
temperature rating of at least 105ºC.
Any wiring deviations may result in personal injury or
property damage. Manufacturer is not responsible
for any damage to, or failure of the unit caused by
incorrect field wiring.
DANGER
High voltage electrical input is needed for this
equipment. This work should be performed by a
qualified electrician.
Electrical Nameplate